Abstract
This dissertation is about health and safety of workers in the workplace. The methodology includes review of the literature and qualitative analysis using survey questionnaires emailed to workers of Kent Industries Incorporated. The questionnaires were sent to the sample participants who were chosen through random sampling.
The answers of the participants revealed that, as a whole, Kent Industries has been implementing health and safety measures as embodied in the Workplace Regulations 1992. The law states that it is the primary responsibility of management of manufacturing businesses to provide a safe and healthy environment, with a comfortable temperature for the workers.
The participants in the survey suggested that health and safety of workers can be successfully produced with the collaboration of both management and employees, although there should be motivation coming from the management first.
Introduction
When we speak of health and safety, it covers a broad range of topics and areas of study which may include regulations, practices, culture, risk and environmental management, and surveys on people in the workplace of their experiences and ideas on health and safety. Most of all, we are dealing with risks.
In the workplace, workers are plagued with risks, safety hazards and unhealthy environment, particularly in manufacturing plants and small businesses. Workers and individuals performing various tasks meet accidents and suffer illnesses from hazards and risks. These situations could have been minimized or avoided with the right application of risk management, appropriate planning with good and positive safety measures accompanied with a valuable study.
Life has become complicated because of new inventions, technology, complicated goals, and globalization. Risk management went along the flow of modernization; it has become complicated too. Risk management in the midst of intense globalization has to be well planned and well studied. Experience and innovations help. Moreover, technological inventions provide areas for possible risk encounter, for example the industrial revolution characterized by major events which introduced a lot of changes in the workplace and organizations. In small manufacturing businesses, risks are multiplied. Environmental problems, accidents and deteriorating health of workers are some of the risks.
Small manufacturing businesses have become a major sector in the world economy. Currently, small manufacturing industries with less than 100 employees offer bigger employment opportunities. But many employees in this sector encounter work related injuries and illnesses. At times, fatal accidents occur resulting into loss of lives.
The government has set up various requirements which must be met to ensure the health and safety of workers in small and large manufacturing industries. Health inspectors conduct routine inspections on these industries to ensure that safety standards and regulations are met and followed at all times. In addition, employees also have the right to ensure compliance with the regulations by management before signing contracts to work with them.
In the UK, government representatives usually visit business premises for the purpose of checking on the risks of health and safety measures instituted inside the business premises. (Perry, 2003, p. 3)
Objectives
The specific objectives of the project include the following:
- To determine the measures being undertaken by small business manufacturing for the safety and health of their workers;
- To assess the major causes of accidents and the emergency care procedures in place at the industry;
- To assess the conditions of the working environment for compliance with health and safety standards;
- To recommend an effective strategy for improvement of health and safety of workers in small manufacturing businesses.
Methodology
The methodologies applied in this study are qualitative research and descriptive/analysis method. Qualitative research uses questionnaires and interviews. Review of the literature using case study involves analysing data and information from research studies already conducted by well known authors and experts in the field.
This study will also use surveys or the qualitative method which is “often regarded as providing rich data about real life people and situations and being more able to make sense of behaviour and to understand behaviour within its wider context” (De Vaus, 2002, p. 5).
Bogdan and Biklen (1998, cited in Fraenkel and Wallen, 2006, p.431) state that qualitative researchers are concerned with context, which can be attained through questionnaires. In this kind of research, qualitative data are collected “in the form of words or pictures rather than numbers” (Fraenkel and Wallen, p. 431).
Another method consists of a review of the literature from secondary sources. The literature review used secondary sources of authors and experts on the subject of health and safety in the workplace. Studies and researches from reliable sources, peer reviewed articles and journals were sourced from online sources and databases. From the literature, we conducted an analysis of the findings.
Qualitative research was conducted using questionnaires sent to workers of Kent Industries. Questionnaires were sent through emails.
Study design
An evaluative case study approach was employed in this project. A case study method is used by researchers to learn about a complex situation based on the objectives and the hypothesis of the study. A researcher has an understanding of that particular instance and intends to provide comprehensive analysis and description of that situation basing it on one particular area. Evaluative case studies are essential where broad and to some extent complex questions are to be answered.
Based on qualitative approach, case studies allow for investigation of a real intervention by focusing on the reasons that caused a certain intervention to succeed or fail. This study focused on health and safety interventions available at Kent industries.
Questionnaires
The research questions were based on an in-depth evaluation of the research objectives and the target company, the Kent Industries Incorporated. Open ended questions were used to give the respondents a chance to provide their opinion and observation about health and safety. But the research also utilised both open and closed questions to collect the required information from the participants. Questionnaire method is considered and found to be effective since the questionnaires are only sent through emails and collected at a later date. The reason for choosing both open and closed questions is that it provided the participants an opportunity to freely answer the questions. The researcher was able to collect information from the company on health and safety in the workplace.
Some questions were general in nature, i.e. they were about risk management, touching on key areas of safety and health in the workplace. But other questions were specific, addressed to managers and workers with respect to their opinion on the company’s programs of health and safety.
Secondary data
To further supplement the questionnaires, the researcher utilized other online journals, books, written articles and magazines on health and safety issues in the process of collecting data (Rigas, 2001, p. 56). This was based on the fact that through it, the researcher would be able to link theoretical perspectives with research purposes, and that the data collected would elicit findings of the analysis. (Greengard, 1999, p. 8)
Sample size and the sampling strategy
First, a letter request, in the form of email, was sent to the management of Kent Industries, requesting permission to conduct the survey on health and safety in the workplace, which the company has implemented or practiced through the years. The Researcher acquired a positive feedback from management, and so a list of workers was requested and obtained, along with their email addresses. E-mails were then sent to the workers requesting their approval of the planned research.
It was explained to the participants that the survey was to be conducted with confidentiality in which they would be provided with numerical codes to protect their identity. Their answers to the questions would not be revealed and that the objective of the study was to simply gather data and information on the subject of health and safety, along with risk management being conducted in the company.
Purposive sampling strategy was employed in identifying the sample population who were employees of Kent Industries Incorporated. Random sampling was used because of its effectiveness and efficiency, in addition to its superiority in obtaining sample from the population. (Preston, 2008, p. 150)
Fraenkel and Wallen (2006, p. 95) argued that the “key to obtaining a random sample is to ensure that each and every member of the population has an equal and independent chance of being selected.” Therefore from the list of workers and managers, random numbers were assigned to each name of person from Kent Industries. From the selected random numbers, a sample was attained. They were then sent emails informing (or requesting) them about the planned research. The list was reduced depending on the response rate of the prospective participants. Twenty-five workers positively responded to our emails. This comprised the sample.
Literature Review
The literature review will cover definitions and related topics on the subject of health and safety in small manufacturing businesses.
Small manufacturing businesses referred to in this dissertation are the small manufacturing firms employing not more than 20 employees (Mazharsoolok et al., 1998, p. 509). Small manufacturing firms are in great demand in the UK because of less competition among large firms. It is these firms which experience demand for labor. (Doi and Cowling, 1998, p. 283)
Small firms have a big role to play in the UK economy, thus studies on safety and health of workers in the workplace of small manufacturing businesses, are of paramount importance (Johnson, 2003, p. 3). Moreover, the role of SMEs in the international economy in the age of globalization is ever growing. (Organisation for Economic Development, 1997, p. 283)
Small businesses have become a major sector in the economy of many countries in the world (Hindley, 1984, p. 42). Currently, small manufacturing industries with less than 100 employees offer bigger employment opportunities to the residents than any other sector. Many employees in these small manufacturing businesses encounter various work related injuries and other illnesses just like employees in larger businesses. At times, fatal accidents occur resulting into loss of lives. (Hughes, 1993, p. 16)
Health and Safety in the workplace
Legislations on health and safety in the workplace provide that the workplace environment should have clean and fresh air. This is provided by the Workplace Regulations of 1992, which provides various environmental issues in the workplace, including construction work and manufacturing. The Regulations provide that workplaces should be provided with adequate ventilation wherein fresh and clean air enter the work area, and the place is not overcrowded. The workers should have adequate clothing; there should be controlled temperature, and workers experience ‘thermal comfort’. (Health and Safety Executive, 2007)
According to this law, there is no exact thermal environment because it should depend on the kind of work the workers are engaged in. For example, the work demands less physical effort, for example in the office, the temperature should be at least 16°C, but if there is much physical effort needed, e.g. in manufacturing of products, it should be at least 13°C, unless provided by other laws. (Health and Safety Executive, 2007)
The risk increases when the workplace produces high temperatures which can result in heat stress for workers. Workers in foundries, glass works and laundry shops are exposed to high air temperatures, while those working in cold stores and plants which produce extreme cold temperature are exposed to cold stress. There should be regular assessment of the workers’ health. Their personal safety should be of prime importance by providing adequate clothing and control of their exposure to the different kinds of temperature.
The Health and Safety Executive (2007) recommends measures that should be undertaken by managers of small manufacturing businesses, shops and SMEs involved in product manufacturing. These measures include introducing engineering features and new technology that can control hot or cold temperature, safety measures by restricting the distance of workers or allowing them to be in safe places, regular medical check-up of workers to determine their fitness for work, use of protective clothing suitable to their kind of work, allowing the workers to acclimatize themselves first before doing any prolonged work, adequate training and development, and expert supervision to ensure that workers are safe in their jobs. (Health and Safety Executive, 2007)
Safety means protection from hazards or danger in the workplace. Hazard is a risk which may cause accident in the workplace, resulting in injuries and ill health. The terms peril, hazard, danger, and jeopardy are used interchangeably with each other and with the term risk. (Gallati, 2003, p. 11)
Health of workers means a sound mind and body. During work or while inside the manufacturing plant, workers must not be subjected to situations which may jeopardize their health, for instance inhalation of toxic substances or being exposed to hazardous chemicals. (Health and Safety Executive, 2009)
The Dangerous Substances and Explosive Atmosphere Regulations 2002 (DSEAR) and the Explosives Atmosphere Directives 99/92 EC (ATEX 137) (Legislation.gov.uk., n.d.), provide for the proper handling and disposal of hazardous and dangerous substances in the workplace (DSEAR and ATEX Regulations, n.d.).
Under the Regulatory Reform (Fire Safety) Order 2005, managements of business premises, including small manufacturing businesses, must ensure that structures are constructed and maintained within the guidelines for the protection and safety of workers. (Grice, 2009, p. 23)
Small-and-medium enterprises (SMEs)
The occurrence of accidents in workplaces is dependent on behavioral characteristics of the employees and also the quality and condition of their working environment. According to Brosseau and Yahui (2005, p. 20), not much is known on the determinants which influences the owners’ intentions accorded to safety and health at work places.
Many of the accidents in small factories occur due to inefficiencies in enforcing proper and legal procedures in risk management which ensure safety and health in the workplace (Gardner et al., 1999, p. 6). Also, the machines in use may not be well maintained and the employees are not well trained to handle the machines and equipment thereby causing injuries on the workers.
Many small industries have no adequate resources essential to increase levels of safety. This includes human resource, technical resources and economic. They employ few workers who do not have enough expertise and are overworked which can contribute to injuries at the workplace (Utton, 1984, p. 5). Most have technological resources that are less effective compared to large enterprises. According to Champoux and Brun (2002, p. 306), the health and safety methods formulated for large industries cannot be directly applied to smaller industries.
Health and safety in the construction industry in Britain is not quite good. Accidents are among the highest of all the industrial groups, resulting in a third of all work fatalities (Health and Safety Commission, cited in Pritchard, 2004, p. 172). Also, those who work in the construction industry are at a greater risk than the general population of a variety of sicknesses like cancer. (Pritchard, 2004, p. 172)
Risks and hazards in the workplace can be in found manufacturing plants. Common injuries and exposure to chemicals are found in metal manufacturing. Aluminium alloys are melted and mixed with oil while heated. The workers are exposed to intoxication of the hazardous substances and skin absorption. (Nordberg, 1998, p. 63.2)
In the soft drink manufacturing, there is not much hazards and danger because mostly manufacturing operation has been introduced with automation. However, the size of the plant does matter too. Workers should wear clothing to protect them from over exposure to heat. (Ward, 1998, p. 65.2)
Designs of buildings and premises for manufacturing plants should be provided enough study to ensure the health of workers. Risk management planning for workplace environment include design assumption risk, fire and safety risk, structural development risk, and environment uncertainty risk. These are associated with the construction of the building and need to be managed effectively in order to reduce the danger to the safety of the employees and the structure and premises. (Lisø, 2006, p. 2)
Safety aspects of buildings are of paramount importance for the persons working within the premises. Risks associated with safety and health includes appropriate risk management to fire, explosion risk, chemical substances, and waste disposal. (Jeynes, 2000)
Electrical connections can cause accidents and fire. This can be avoided through careful planning and design of the building. The design, construction, layout and furnishing of buildings play a key role in any fire safety management strategy. (Debizet and Symes, 2009, p. 197)
Risk management
“Risk management starts and ends with quality.” (Kent, 2004, p. 31)
Management has the responsibility to protect workers from risks and injuries in the manufacturing plant. Risk managers should devise ways to minimize risks by applying a scientific approach to deal with risk. This may require a step-by-step process. (Gallati, 2003, p. 11)
Managing risks involves taking care of the safety and security of individuals or organizations. (Saied, 1990, p. 46)
When we talk of risk, we talk of the outcome or result. However, the results can be modified by at least determining what these risks are. This can be done through management and planning. (Craighead, 2009, p. 4)
Risks cannot be avoided, even if they “can be transferred, accepted, managed, minimized, or shared” (Latham, 1994 cited in Rahman and Kumaraswamy, 2002, p. 131). Businesses face risks everyday in the course of their operations. These risks can range from economic downturn and adverse market conditions to losses arising from natural calamities or man-made accidents, fire, or as a result of corrupt practices of employees and managers of companies. (Kent, 2004)
Each contingency may generate financial losses that undermine businesses in achieving what must, no matter what other objectives are pursued, be regarded as the primary objective – namely maximising profits. (Brewer & Huque, 2004, p. 78)
Risk management means early identification of the threat of risks in the premises and finding out the proper solution to the identified risks. Risk management process is one of the most important tasks for any company, business, or organisation. (Furness and Muckett, 2007, p. 14)
In the United States, professionals see the significance of joining hands in implementing health and safety rules in the workplace, and partnerships of the private and public sectors. (Minter, 2004, p. 37)
In the UK, the manufacturing industry has coordinated and networked with the Health and Safety Executive (HSE) in order to have a strong base and cooperation to provide expertise in the field of health and safety, including quality advice and consultations with member companies. (Works Management, 2006)
The EEF is a support organisation of manufacturers in the United Kingdom which aims to help manufacturers cope in the fast changing world of globalisation. The EEF also promotes health and safety in the manufacturing world, advising and providing resources for the protection of workers in the workplace. (EEF, 2010)
Environmental Management System (EMS)
Manufacturing firms must be able to introduce an environmental management system in order to protect the health of their workers. An environmental management system is a way of addressing the impact on the environment by issuing guidance to organisations, manufacturing firms, businesses, and governments for the purpose of controlling environmental abuse. (Brady, 2005, p. 160)
An EMS answers the environmental compliance regulations, lowering environmental costs, reducing risks, and other relevant activities for environmental best practice. (Andrews, 2001, p. 31)
Every organisation that seeks ISO 14001 certification should have an EMS Manual. The manual is an important core element of an EMS and is a guide borne out of an effective environmental management system. An EMS aims for sustainable development in the community, and minimise waste and hazardous materials in manufacturing plants. (Whitelaw, 2004, p. 280)
Furthermore, an EMS is a set of rules and requirements that sets up a policy for environmental promotion. It can be effectively implemented through the guidelines set by ISO 14001. (Christini et al., 2004)
ISO promotes application of environmental management systems which can provide guidelines not just for environmental preservation but also for avoidance of industrial accidents. (Watson, 2006, p. 280)
Data Analysis and Presentation
Kent Industries Incorporated is a company which supplies industrial products of different brands. It manufactures products, but also distributes other brands of motors like the Moeller brand motors and motor controls. Other motors include the Siemens, Benshaw, Lovato, Micron, and many other quality industrial products. (Kent Industries Incorporated, 2011)
The main concern of this study is the question: how are safety and health promoted and enhanced at the Kent Industries Incorporated? The question was addressed to the participants. This question is expressed in the succeeding diagram.
The participants’ answers were a reflection of the kind of safety and health measures that Kent Industries Incorporated has implemented in the manufacturing plant.
Some of the participants’ answers are enumerated below.
Five of the participants with supervisory jobs said:
“The workplace is conducive to work, where there is clean and fresh air. Environmental issues and problems are quickly addressed by management.”
But one participant answered, “Accidents sometimes occur which put the lives of workers in danger.”
Three workers said that risk management is quite effective at Kent since dangers and hazards have been dealt with effectively. There has been no report of accidents. There were some accidents however but these were small ones and did not involve any injury.
Most of the participants said that company benefits are quite sufficient; health benefits are also answered by the company. But one responded said this comment:
“Sick leave and benefits are not correctly afforded the workers.”
Some other answers of participants include the following:
“There is close cooperation between the workers and management in implementing right and effective risk management.”
Three workers who work on machines said:
“Our machineries are quite old, but they are properly maintained.”
The comments above are some of the positive responses provided by the participants. However, there are some negative comments which put the company’s integrity into question. Some of these comments include the following:
Two participants commented: “Some of the old workers are getting sick due to wastes which are not properly disposed of.”
One commented negatively on the condition of the equipment:
“Some machines are too old that it seems maintenance is not sufficient to provide safety. Replacement is the answer.”
Two participants commented: “There is no cleanliness and correct safety measures in our plant.”
Fifteen participants – a majority – provided a very positive answer on question number 8:
Is a guide to health and safety possible at Kent Industries? Majority answered ‘yes’.
“A guide to health and safety of workers can be successfully produced with the collaboration of both management and employees, although there should be motivation coming from the management first.”
There were five participants who provided the negative comments above, but majority (n = 20) were optimistic of the kind of safety and health measures being introduced and implemented inside the Kent Industries manufacturing plant.
Steps undertaken by management to ensure safety in the workplace, per participants’ answers:
- Maintenance of machines and equipments every six months
- Fire safety and strategy installed and instituted annually
- Issuance of clothing, gloves and workers’ paraphernalia
- Adequate supervision by the manager.
The participants listed several causes of accidents in the workplace.
Table 1: Causes of accidents
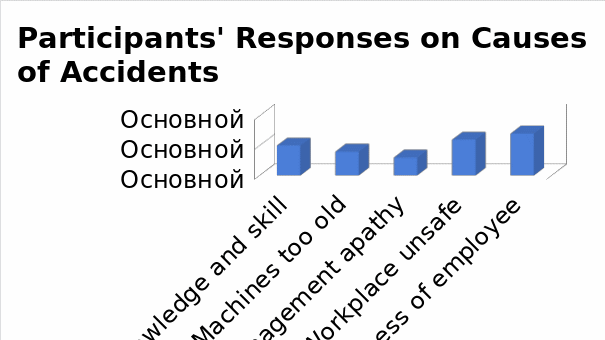
Table 1 and Figure 1 show the participants’ responses as to the causes of accidents in the workplace. From the responses of the participants, carelessness is the number one cause of accident; ranked number 2 is workplace unsafe; next is lack of knowledge; this is followed by machines too old, and the last is management apathy.
To analyse the answers of the participants, we can say that majority blame carelessness and not mismanagement as the primary cause of accident in the workplace. They pay more attention to the employee’s attitude and the unsafe features of the workplace.
From the responses of the participants, lack of knowledge and skill and workplace unsafe are the primary causes of accidents. This is followed by ‘machines too old; then management apathy and careless of employee garnered the same score.
Demographic information was taken to determine whether this has influence on the results of the study. The information provided the gender, age, marital status, and educational level of the participants. However, the responses of the participants showed that the demographic information had no influence on the health and safety of the respondents.
Conclusion/Recommendations
Conclusion
From the responses of the participants, which were taken through questionnaires sent to them through emails and sent back to this Researcher for evaluation, majority do not blame management for accidents in the workplace, but the employees’ behavior.
The participants also answered that the company has implemented safety and health measures in the manufacturing plants. They have a particular guide which is in accord with existing regulations on risk management and safety in the workplace.
A comprehensive and effective guide for health and safety of workers in the workplace can be produced through a cooperation and partnership amongst the different stakeholders of the company, for instance, the owners, the workers and employees, and the community in which the business thrives.
The literature review provided information and data on health and safety in the workplace. There are those small manufacturing businesses which find it difficult to provide health and safety measures. As a result, employees encounter accidents and injuries due to poor implementation of the health and safety regulations.
Recommendations
The following are recommended safety measures to avoid accidents and risks of injuries in the workplace:
- Machineries and equipments must have emergency circuit breakers and safely situated inside the manufacturing plant or factory. Cooking equipments and other flammable appliances should be kept from hazardous chemicals and materials.
- Housekeeping and cleanliness in the workplace must be properly administered, keeping away hazardous materials.
- Building architecture must be properly planned, taking into consideration safety measures, fire exits, appropriate lighting and other precautionary measures to promote safety in the workplace.
The causes of accidents and injuries listed by the participants should be considered in building a guide for health and safety in the workplace.
References
Andrews, R., 2001. Environmental management systems: history, theory, and implementation research. In C. Coglianese and J. Nash, Regulating From the Inside: Can Environmental Management Systems Achieve Policy Goals?. Washington DC: Resources for the Future.
Brady, J., 2005. Environmental management in organizations. UK: The Institute of Environmental Management and Assessment (IEMA).
Brewer, B. and Huque, A. S. Performance measures and security risk management: a Hong Kong example. International Review of Administrative Sciences 2004; 70; 77.
Brosseau, L. and Yahui Li, S., 2005. Small business owners’ health and safety intentions: A cross-sectional survey. Environmental Health: A Global Access Science Source, 4 (23), 4-23
Champoux, D. and Brun, J., 2002. Occupational Health and Safety management in small size enterprises: an overview of the situation and avenues for intervention and research. Safety Science, 41 (4), 301-318
Christini, G., et al., 2004. Environmental management systems and ISO 14001 certification for construction firms. Journal of Construction Engineering and Management, ASCE, Web.
Craighead, G. 2009. High-Rise Security and Fire Life Safety (Third Edition). New York: Elsevier Inc.
Debizet, G. and Symes, M., 2009. Expertise and methodology in building design for sustainable development: a Franco-British comparison. In I. Cooper and M. Symes, Eds., Sustainable Urban Development 4: Changing Professional Practice. Oxon: Routledge.
De Vaus, D., 2002. Surveys in social research (5th Edition). Oxon: Taylor & Francis Group.
DSEAR and ATEX Regulations (n.d.). What do DSEAR and ATEX stand for? Web.
Doi, N. and Cowling, M., 1998. The evolution of firm size and employment share distribution in Japanese and UK manufacturing: a study of small business presence. Small Business Economics [e-journal] Available through: City University London.
EEF, The Manufacturers’ Organization, 2010. Who we are. Web.
Fraenkel, J. and Wallen, N., 2006. How to design and evaluate research in education (sixth edition). New York: McGraw-Hill Companies, Inc.
Furness, A. and Muckett, M, 2007. Introduction to Fire Safety Management. Burlington, MA: Butterworth-Heinemann.
Gallati, R., 2003. Risk management and capital adequacy. New York: McGraw Hill Publishing, Inc.
Gardner, D. et al., 1999. Mechanical equipment injuries in small manufacturing businesses. Safety Science, 33 (1-2), 1-12
Greengard, S., 1999. Putting HR software to work: human resources management. Workforce, 78 (9), 4-8
Grice, A., 2009. Fire risk: fire safety law and its practical application. London: Thorogood Publishing Ltd.
Health and Safety Executive, 2007. Workplace health, safety and welfare: a short guide for managers. Web.
Health and Safety Executive, 2009. The Dangerous Substances and Explosive Atmospheres Regulations 2002 [online]. Web.
Hindley, B., 1984. Economics and small enterprises. In: C. Levicki, Ed., Small business: theory and practice. Great Britain: The Gresham Press.
Hughes, A., 1993. Industrial concentration and small firms in the United Kingdom: the 1980s in historical perspective. In: Z. Acs and D. Audretsch, Eds., Small firms and entrepreneurship: an east-west perspective, p. 16. Great Britain: Press Syndicate of the University of Cambridge.
Jeynes, J., 2000. Practical health and safety management in small businesses. Woburn, MA: Reed Educational and Professional Publishing Ltd.
Johnson, P., 2008. The formation and development of small businesses. United States of America: Routledge.
Kent, J., 2004. Risk management. [e-journal] Web.
Kent Industries Incorporated, 2011. Kent store. Web.
Legislation.gov.uk., n.d. The Regulatory Reform (Fire Safety) Order 2005 [online]. Web.
Lisø, K. R., 2006. Integrated approach to risk management of future climate change impacts. [e-journal], Web.
Mazharsolook, E., Robinson, D., and Seferis, K., 1998. IT-based problem solving: helping small manufacturing companies. In S Björgvinsson, 1998, Changing the ways we work: shaping the ICT-solutions for the next century, p. 509. Oxford, England: IOS Press.
Minter, S., 2004. The future of safety. Occupational Hazards [e-journal], Web.
Nordberg, G., 1998. Metals: chemical properties and toxicity. In J. M. Stellman, Ed., Encyclopaedia of occupational health and safety: fourth edition. Geneva: International Labor Organization.
Organisation for Economic Development, 1997. Globalisation and small and medium enterprises (SMEs) (Vol. 2 Country Studies). France: Publication Services, OECD.
Perry, P., 2003. Fire safety questions and answers: a practical approach. London: Thomas Telford Publishing.
Preston, L., 1986. Business and public policy. Journal of Management, 12 (5), 261–275
Pritchard, C. Building for health? The construction managers of tomorrow. The Journal of the Royal Society for the Promotion of Health 2004; 124; 171.
Rahman, M. and Kumaraswamy, M., 2002. Risk management trends in the construction industry: moving towards joint risk management. Engineering, Construction and Architectural Management 2002 9/2, 131-151. Blackwell Science Ltd.
Rigas, D., 2010. The Business of airline, the twenty first century. England: Routledge.
Saied, J., 1990. Approaches to risk management. Cornell Hotel and Restaurant Administration Quarterly 1990; 31; 45.
Utton, M., 1984. Concentration, competition and the small firm. In: C. Levicki, Ed., Small business: theory and practice. Great Britain: The Gresham Press.
Ward, L., 1998. Beverage industry. In J. M. Stellman, Ed., Encyclopaedia of occupational health and safety: fourth edition. Geneva: International Labor Organization.
Watson, M. Protecting the environment: the role of environmental management systems. The Journal of the Royal Society for the Promotion of Health 2006; 126; 280.
Whitelaw, K., 2004. ISO 14001: Environmental systems handbook. Burlington, MA: Elsevier Ltd.
Works Management, 2006. Two-pronged lead on health and safety [e-journal], Web.
Appendix A: Questionnaire
- Is the workplace conducive to good working conditions such as clean and fresh air, controlled temperature, and free of waste and hazardous materials?
- Has management undertaken steps to ensure health and safety in the workplace?
- What are these steps?
- Do you work with a ‘comfortable temperature’ at Kent Industries?
- Are there many risks to the health and safety of workers in the workplace?
- What are the causes of accidents in the workplace?
- In your experience with the company, has there been any accident in the workplace?
- Is a guide to health and safety possible at Kent Industries?
- Do you enjoy sick leaves and other benefits at Kent Industries?
- What suggestions can you recommend to improve health and safety of workers at Kent?