Introduction
Earlier theories relating to competitive strategies of manufacturing organizations depended on several rational assumptions such as (a) basic reason for the existence of a firm is to produce something of value, (b) manufacturing has a critical role to perform in the creation of that value, (c) since a firm has different ways of competing, it becomes essential that the firm links its competitive strategy to manufacturing and (d) there is the need for an explicit and well-defined strategic planning process to design and implement a strategy leading to strong competitive position (Skinner, 1969). However, actual management practice has been found to be inconsistent with these assumptions. This process is driven by operational necessity and available technical opportunities (Abernathy and Clark, 1995). The slow process can be attributed to the efficiency of the traditional tools available for designing and implementing manufacturing strategies. This review attempts to present ideas from the manufacturing strategy literature for identifying the gaps in implementing lean manufacturing strategies to improve organizational performance. The review also extends to the study of factors influencing the application of lean manufacturing strategy in the context of developing countries.
Concept of Manufacturing Strategy
The work of Wickham Skinner has formed the philosophical foundation of the concept of manufacturing strategy. Later other scholars and academicians developed other dimensions to the concept (Hayes and Wheelwright, 1979). For example, Wheelwright (1978) elaborated manufacturing strategy into competitive criteria, Leong et al. (1990) into competitive priorities and Hill (1985) into order winners. These research works identified the influence of industry, corporate, business and functional strategies on manufacturing competitiveness. Skinner identified other important variables such as “costs, deliveries, lead times, quality levels and reliability, changing schedules, new product introduction or low investment.” The following figure represents the evolution of different competitive criteria supporting manufacturing strategy.
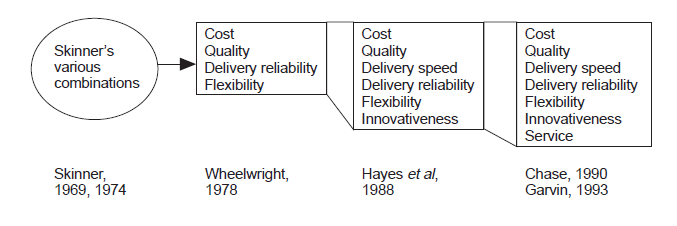
In studying the concept of manufacturing strategy, the relationship between business strategy and business performance have played a significant role (Cool and Schendel, 1987; Banker at al. 1996). Although the body of literature on manufacturing strategy is not large, there are number of studies, which deal with the testing of some concepts, model building and operationalizing the models connected with manufacturing strategy. The key focus of many of these studies was to examine manufacturing strategies and business performance in terms of their influence on the manufacturing. One of the frequent questions is on the influence that a characteristic of the manufacturing strategy may have on the business performance. Existence of a correlation between manufacturing strategy and business performance has received ardent support from the manufacturing strategy literature. For example, the work of Swamidoss and Newell (1987) exhibited the positive relationship between business performance and manufacturing strategy represented by its element of “flexibility”. There are other studies, which have identified the link between quality and good performance. For example, Ferdows and DeMeyer (1990) and Noble (1995) have postulated that quality forms the basis for effective manufacturing strategies. Literary works focusing on world-class manufacturing suggest that manufacturing capabilities are the foundation on which major players compete with each other (Ward et al. 1996).
The work of Skinner (1969) on manufacturing strategy prescribes the links among environment, competitive strategy and manufacturing strategy to enable the organization to achieve improved business performance. Findings from the study by Williams et al. (1995) provide support to the relationship between competitive strategy and manufacturing strategy. The study also found the relationship between manufacturing strategy and organizational performance. Gupta and Lonial (1998) developed a conceptual model to test the linkages among business strategy, manufacturing strategy and organizational performance. Most of the research scholars concur on the point that the key objective of developing a manufacturing strategy is to provide support to the business strategies of an organization so that the organization can pursue its competitive advantage (Platts et al. 1988; Slack, 1991; Hill 1993; Fine and Hax 1985). According to Hill (1993), corporate strategy forms the basis of business strategy, which in turn drives marketing strategy and other functional areas within the organization. However, there has not been a strong focus on the process of formulation of manufacturing strategies in the literature as they focused on the content, objectives and decision areas connected with manufacturing strategy. The authors in the field of manufacturing strategy focus mainly on the strategic objectives and decision areas, which approach according to Leong et al. (1990), “depends on breaking manufacturing down into a number of decision areas and making the goals of manufacturing explicit in terms of a number of performance criteria.” Research findings of manufacturing objectives, strategic decision areas and strategy processes lay the foundation for further research on manufacturing strategy.
Definition of Manufacturing Strategy
Definition of manufacturing strategy by Skinner (1969) is the earliest, which explains the strategy as the exploitation of “certain properties of the manufacturing function” to be used as the competitive tool by the organizations. Hayes and Wheelwright (1984) looked at manufacturing strategy as a “consistent pattern of decision making” in the area of manufacturing and they established the linkage of manufacturing strategy to business strategy. Cox and Blackstone (1998) defined manufacturing strategy as “a collective pattern of decisions that acts upon the formulation and deployment of manufacturing resources. To be most effective, the manufacturing strategy should act in support of the overall strategic directions of the business and provide for competitive advantages.” For the purpose of this paper, manufacturing strategy is defined as “a pattern of decisions, both structural and infrastructural, which determine the capability of a manufacturing system and specify how it will operate to meet a set of manufacturing objectives which are consistent with overall business objectives” (Platts, 1990). Various definitions and previous research work carried out focusing on manufacturing strategy have found the importance of manufacturing strategy in the overall organizational success.
Thus, the concept of manufacturing strategy has been defined in a number of ways over the years. The following table presents examples of connotations to manufacturing strategy.
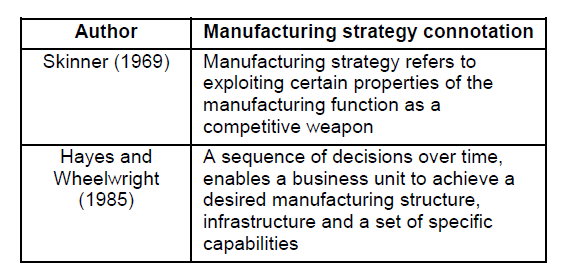
Elements of Manufacturing Strategy
Manufacturing strategy can be divided into its elements of content and process, where content refers to the decision areas, which a strategy should comprise and the basis on which decisions are made. Process in the context of manufacturing strategy includes the process of designing and implementing a manufacturing strategy, which is based on the content. The following sections describe the content and process of manufacturing strategy.
Manufacturing Strategy Content
Manufacturing strategy contents represent the manufacturing capabilities, described in terms of competitive priorities. Contents also include strategic choices connected with manufacturing processes and infrastructure and best practices (Hill, 1993). Best practices in manufacturing strategies include the application of techniques like JIT or MRP. “Manufacturing strategy content embodies the choice of the most beneficial set of manufacturing capabilities for a business unit and the investments needed to build that set of capabilities” (Ward et al., 1996). It also includes the investment needed to build the selected capabilities. These capabilities are considered as the best strategic assets accumulated by the business through a pattern of investments made over a period and in addition, other players in the industry cannot replicate these capabilities, nor they can find any good substitutes (Dierickx & Cool, 1989). “Thus, the capabilities such as low cost, quality, flexibility, and delivery performance that a manufacturing possesses are stocks of strategic assets which have been accumulated through a flow of investments in capability building programs over time.”
Competitive Priorities
Authors in manufacturing literature have used different terms to describe the manufacturing capabilities; but in general, they have been described as “competitive priorities” (e.g. Hayes and Wheelwright, 1984). “Hill (1994) classifies such capabilities as order winners and qualifiers, according to their importance in gaining customers” (Ward et al, 1996). Even though literature has used different terms, there is general agreement in the literature about the dimensions of competitive priorities, which are generic in nature and includes “cost, quality, delivery performance and flexibility.” Leong et al. (1990) support this assertion. These dimensions can be termed as competitive manufacturing capabilities as opposed to the use of the term “priorities”.
Competitive capabilities represent elements present within a firm, which are aimed at improving firm value and these capabilities, are the elements of distinction between a firm and other players in the marketing competing with the firm. The management cannot directly control these variables, as they normally are the outcomes of critical management decisions. Innis and LaLonde (1994) and Koufteros (1995) have identified a set of competitive capabilities, which characterize the ability of an organization to meet the customer needs and preferences. These include “price offered, product quality, product line breadth, order fill rate, order cycle time, order and shipment information, and frequency of delivery.” It is essential that the firm maintain a low-cost structure so that it would be able to offer its products at a price, which is comparable to that offered by the competitors. Alternatively, the product must be of a higher value so that it can fetch a premium price in the market. “Product quality and product line breadth (variety) must meet or exceed customer expectations. The organization should have high order fill rates, short order cycle times, accurate order and shipping information, and frequent deliveries.” These manufacturing capabilities should be able to help the firms achieve a superior level of customer satisfaction and improved market performance.
Decision Areas
Firms often make their “manufacturing capability building program” choices based on their strategic manufacturing decisions. Hayes and Wheelwright (1984) have observed that the manufacturing strategy of an organization is formulated through a series of key choices, which are focused around a few substantive business functional areas. Ward et al. (1988) have found empirical support in the literature for a set of strategic choices that help build manufacturing capabilities by firms. These include “(1) process technology (2) capacity, facilities, and
vertical integration (3) quality systems (4) production planning/inventory management systems (5) work force management, and (6) manufacturing organization.”
The following figure represents a content model of manufacturing strategy, which incorporates competitive manufacturing capabilities and strategic manufacturing decision areas.
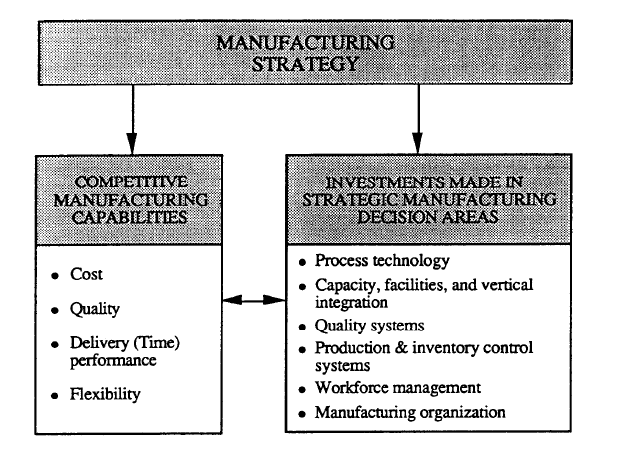
Decision areas are better described as decision categories. These decision categories have impact on the firm at corporate level as well as at the production unit level in the long run. Based on the possibilities of altering these decision categories, they can be classified into structural and infrastructural decisions. The structural decisions are those, which involve large financial investments, and which the management would not like to change. On the other hand, the infrastructural decisions comprise of organizational changes, which can be altered easily. Strategic decision areas are those which are critical and which make up a manufacturing strategy. According to Wheelwright (1984), the collective patterns of decisions in these areas determine the structure and in addition, they are responsible for determining the manufacturing capabilities of a firm. Any firm, which makes effective choices in the structural and infrastructural decisions, will be able to achieve excellence in its manufacturing capabilities. The following table presents a summary of strategic decision areas as suggested by various authors in the literature.
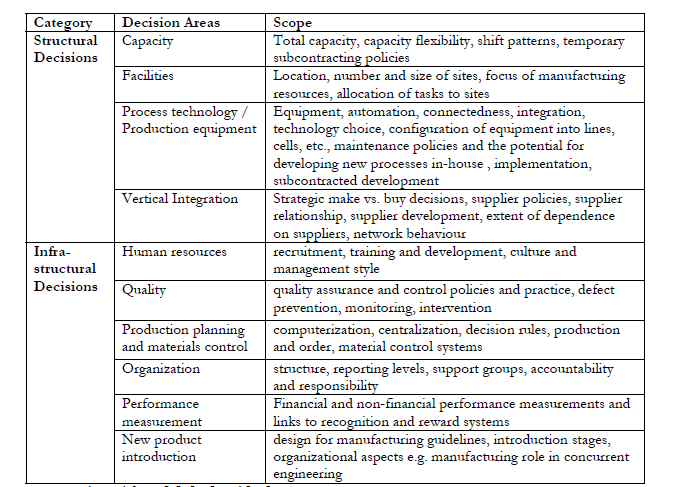
The manufacturing strategy content can also be divided into “process choice” and “infrastructure”. While process choices suggest the appropriate physical processes to carry out the manufacture, infrastructure is intended to provide support to the physical processes. “The base for all strategic manufacturing decisions is the order winners and qualifiers connected to the competitive priorities.”
There is another way of addressing the strategic decision areas, by using strategic questions, which are divided into structural and infrastructural questions. These questions concern different hierarchical levels in the firm. While the top management is expected to deal with strategic decisions such as facility placements, the factory management is authorized to handle local questions. The following table illustrates the decision areas as divided into structural and infrastructural decisions.
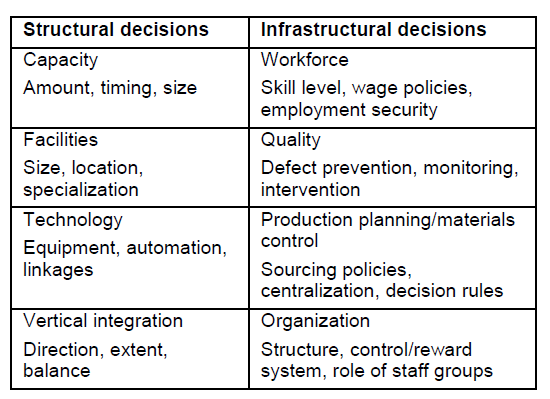
Manufacturing Strategy Process
Generally, the process of designing and implementing manufacturing strategies can be addressed from two different perspectives – resources possessed by firms or market capabilities of the firms. Resources-based strategies are based on the existing capabilities of the firm. In this process, management selects certain core capabilities of the firm and analyzes them through market tests. The objective of these tests is to ensure that the capabilities can provide a sustainable competitive advantage to the firm. Based on the analysis the firm decides on business diversification and other capability development strategies and develops them to improve business performance. Since the resource-based strategy process is of recent origin, there are no established models to substantiate the potential benefits arising from this process.
“The market-based approach includes the design, formulation and implementation of the manufacturing strategy beginning by defining the business strategy and customer needs.” Hill (1994) has developed the most popular process model. This process begins with defining the corporate objectives and developing the manufacturing strategies based on the corporate strategies already established. As the next step, the market segments, volume of sales, and market mix elements are stated. In the final step, the competitive factors are identified including the competitive priorities that the manufacturing strategy needs to address and fulfill.
Manufacturing Strategy Frameworks and Models
“Considering manufacturing strategy in its larger strategic context has been thematic in conceptual literature in operations but relatively neglected in empirical studies, thus leaving predominant conceptual models of manufacturing strategy largely untested” (Ward & Duray 2000). Most of the conceptual manufacturing strategy models have followed a traditional approach focusing on the idea of matching manufacturing structure and infrastructure with business strategy. The models attempt this matching through a process of formal planning (Skinner, 1969). In the conceptual strategic models, the choice of specific strategy dimensions is influenced by the market demand for the product and the actions of competitors (Pun, 2004). The following sections illustrate a few manufacturing strategy models including the basic conceptual model. The second model discussed is the latest thinking, which looks at developing a manufacturing strategy model using a balanced scorecard approach.
Conceptual Model of Manufacturing Strategy
From a detailed review of the literature covering the manufacturing strategy area, a basic conceptual model of manufacturing strategy can be developed. This model suggests that both competitive strategy and manufacturing strategy are subjected to environmental dynamism. In this model, competitive strategy is placed in a mediating relationship. This is because the competitive strategy has a role to intervene between environmental dynamism and manufacturing strategy (Venkatraman, 1989). In this model, competitive strategy has a direct influence on the manufacturing strategy.
Principles of Conceptual Model
Firms develop competitive priorities based on the scheme that they develop corporate strategy initially followed by business strategies, with the objective of seeking a competitive position in the industry. As a next step, firms “operationalize these strategies by bundling of competitive priorities at an appropriate level of performance.” It must be noted that competitive priorities represent strategic variables, which need to follow a logical sequence in their development. “Whereas the competitive advantage and the value of the product can be determined logically at a business strategy level using appropriate competitive priorities, it can be only physically realized by operationalizing the competitive priorities at the manufacturing task level.” However, the fact remains that garnering a competitive advantage or the acceptance of the products of the firm may not necessarily ensure the continuance of the business of the firm. It is true that a firm can survive and grow only when the organization maintains its competing ability or the acceptance created by the firm above the cost incurred by the company in developing such ability or acceptance.
It must be noted that competitive priorities by themselves do not entail any cost on the firm, as they are after all logical variables. In order to understand the impact on cost in attaining the competitive advantage or acceptance of the products, it is necessary that the firm operationalize the competitive priorities at the physical level in the form of manufacturing.
The purpose of accumulating competitive priorities at a particular level of performance is to ensure that adequate market demand for the product is created and the value, which enables the product to sustain its demand. This also creates a necessity for the manufacturing system to be operated at a level of performance, at which level the system should provide for its associated operating costs. It must also be recognized that there are multiple competitive priorities, which enable the operation of multiple manufacturing tasks. Therefore, the multiple manufacturing cost factors determine the cost of operating at the target level of performance of the competing priorities. These multiple manufacturing cost factors are referred to as the “economies of manufacturing.” “The ultimate success of the manufacturing strategy process lies in the fact that the value of the product line to achieve competitive advantage in the industry should be more than the cost due to the Economies of Manufacturing.” The following figure presents the conceptual manufacturing strategy model.
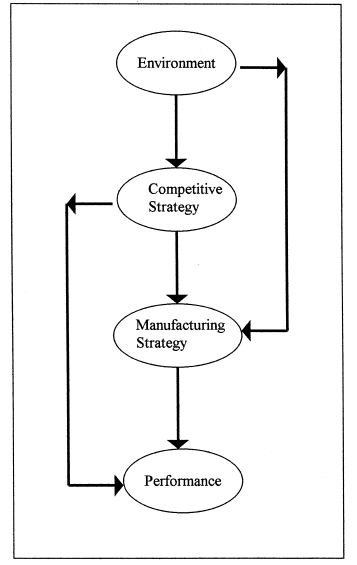
The origin of this conceptual model can be traced to the work of Skinner (1969) on manufacturing strategy. As observed earlier, the work of Skinner (1969) provided a detailed account of the links among “environment, competitive strategy and manufacturing strategy” to accomplish significant improvement in organizational performance. Anderson et al (1989 and Leong et al (1990) provided large support to the conceptual model proposed by Skinner. However, they could not produce much empirical support to the application of the model in real-life situations. Even the subsequent conceptual model developed by Hill (1994) was not provided any empirical support to the interrelation between environment, “competitive strategy and manufacturing strategy.” A review of the related literature also does not produce any evidence to support simultaneous empirical tests focusing on the connections among these three variables.
Although there is no empirical study that focused on the linkage among all the dimensions represented in the conceptual model, there are few studies, which have tested pieces of the conceptual model. For example, Vickery et al. (1993) found a correlation between the variables of competitive strategy and production competence and their positive impact on organizational performance. Miller and Roth (1994) presented an empirical study showing the association between competitive and manufacturing strategies. Gupta and Lonial (1998) made use of a path model to examine the connection among different strategies. Studies by Swamidass and Newell (1987) and Ward et al. (1995) empirically explored the linkage between environmental dynamism and manufacturing strategy and their influence on business performance. Both these studies exhibited a positive relationship between environmental dynamism and manufacturing flexibility. According to Miller and Friesen (1983),
”Environmental dynamism refers to the degree of turbulence in products, technologies, and demand for products in a market” (Ward, 2000).
Model of Strategic Manufacturing Management System
Borges de Menezes et al. (2010) presented this model, which combines the manufacturing processes at different levels. This model attempted to establish a coherent set of production processes to improve the productivity of the processes. The novelty of this model is that it is designed to include a Balanced Scorecard approach focusing on the creation of rationalities for planning, implementing and controlling different methodologies. The model encompasses an analytical base expanding to concepts relating to manufacturing strategy, the balanced scorecard technique, features of the Performance Dimensions Model developed by Neely et al (1994), Performance Measurement framework proposed by Martins (2000).
The manufacturing strategy formulation process prescribed by Platts (1994) supports the development of the model and it possesses characteristics of strategic learning proposed by Harrison & Boyle (2006) which integrates planning and execution. The model adopts strategic management principles recommended by Fernandes et al. (2006) and strategic manufacturing performance management models proposed by Chenhall (2005) and Paranjape et al (2006). The Strategic Manufacturing Management System (SMMS) has taken into account the issues involved in manufacturing design, deployment of resources and management of manufacturing activities. The purpose of the model is to enable managers to understand and convert the manufacturing objectives into actions that can run as a program on the shop floor level for ensuring better performance. “This improved performance should be represented by the evolution of those indicators related to the fulfillment of those goals set out by the deployment of business strategy, which will be defined by the SMMS.)
The objectives of SMMS are:
- “Improve the manufacturing performance through achievement or positive development of the most representative indicators, as defined by the business and manufacturing strategies.
- Align efforts for the development and achievement of the manufacturing objectives, creating synergies and avoiding (or reducing) the effects of the search for local results to the detriment of the whole.
- Communicate the strategies to employees at the operational level, allowing them to understand goals and up to what extent their actions may affect the entire company.” (Borges de Menezes et al., 2010)
The development of the model followed a process comprising of four different stages. Checkpoints were established at the end of each planning stage. On these check points, there could be either “change” or “follow” action is possible.
The steps involved are:
- Establishing the Perceived Vision and Strategy – during this stage, the manufacturing objectives are recognized and distributed in respect of the four dimensions of the balanced scorecard. Execution of this step involves consideration of the assessment of the organizational environment, objectives covered under the process of manufacturing strategy and the manufacturing vision.
- Defining the Diagnostics and Improvement Programs – at this stage, there is an evaluation of individual measures and their relationship with the environment. Manufacturing competitive dimensions such as “quality, time, cost and flexibility” become the factors on which the measures are balanced.
- Designing the Performance Management System – using the balanced scorecard approach. Under this stage, the results of steps 1 and 2 become handy. The objective of this step is to define and confirm the corporate strategy already developed and the manufacturing goals established now. This step also confirms the relationship of corporate and manufacturing strategy with the indicators established under steps 1 and 2.
- Organizing for actions is the final step in the process. The goal of this step is to transform the manufacturing strategy objectives into processes. This step translates the manufacturing strategy into understandable and measurable actions, which are easy to follow by the workers. This step establishes a procedure for managing the measurements that the performance management system develops.
The following figure illustrates the four steps in the Strategic Manufacturing Management model.

The gap in Manufacturing Strategy Literature
Even though Skinner (1969) identified the missing link in corporate strategy that connects manufacturing strategies with business strategies even as early as at the beginning of the 1970s, many of the studies involving manufacturing strategies carried out since then have been observed NOT to have considered the real-world operational issues. This implies that there are problems between the development of strategic management models and their implementation and application (Platts, 1990).
Sousa et al. (2006) observe that there is a serious gap between the knowledge that is developed about the strategic management models and their proper implementation to improve organizational performance. Many firms have found it difficult to manage their performance in a strategic way (Bourne et al.2005; Franco-Santos and Bourne, 2003). The reason for facing such difficulties is that they do not adopt a systematic approach (Najmi et al. 2005). This is the case especially in respect of manufacturing strategies, where it is important to comprehend the logic of performance. It is also important to define the dimensions of manufacturing strategies and their integration into overall corporate strategy (Bond, 1999).
Prior literature has emphasized that firms must develop their manufacturing strategies within the broader context of organizational-level strategies. In order to improve the organizational performance firms are expected to align their resources and capabilities with their competitive strategy. Demands and preferences of customers and actions of the competitors were the key elements in the firms deciding on the specific strategic dimensions (Pun, 2004). Theoretical contributions to past literature dealing with the concept of manufacturing strategy argue that either market requirements or the manufacturing resources available with the firms are the prime bases on which firms have to formulate their manufacturing strategies. However, Kumar et al (2009) argue that the existing studies failed to examine another comprehensive set of variables that could influence the formulation of manufacturing strategy. For example, the studies have not focused on the role of innovation orientation in combination with the resources and market orientation of the participating firms. There are no adequate empirical tests about the adoption of innovation as a manufacturing strategy, even though much of the recent literature highlights the role of innovation in formulating manufacturing strategies (Kumar et al. 2009). This paper considers that innovation has an increased role in devising the manufacturing strategies by firms and therefore, this is a serious gap in the literature to have short-focused on innovation.
Another most important concept, which the manufacturing strategy literature has not covered widely, is lean manufacturing, which has a significant role to play in improving the manufacturing capabilities of firms. A number of tools have been developed to support lean manufacturing; nevertheless, lean has not been provided a wider recognition in the manufacturing strategy literature. Although there were a number of studies subsequently undertaken in the area, there has been no clarity of the concept and features distinguishing lean principles (Shah and Ward, 2007). Recent works have added precise definitions to lean production in manufacturing (Narasimhan et al. 2006). Nevertheless, the developments have not identified the lean practices that can be associated with services, as they have in manufacturing (Shah and Ward, 2003).
Lean Manufacturing as a Manufacturing Strategy
The Toyota Production System: Beyond Large Scale Production by Taiichi Ohno (1988) and Lean Thinking by Womack and Jones (1996) are the two important works in the area of lean concept. Ohno (1988), one of the creators of TPS identified two criteria to complement lean production. They are Just in Time (JIT) and autonomation. JIT is a production system in which the production at each step will not start until the customer signals the requirement. Ohno also developed the concept of Kanban with six accompanying rules to support JIT. Autonomation signifies following autonomous automation. Implementing the concept of autonomation is to focus on obtaining the highest value parts of lean practices.
In their work Lean Thinking, Womack and Jones (1996) developed the concept of lean management further and grouped it into five different categories – “Value, Value Stream, Flow, Pull and Perfection”. Value denotes the use customer derives from the product and works backward to design the production process efficiently. To improve and sustain their competitive ability, firms design their production process by creating a value stream so that each step of the production process provides value. Flow ensures that processes are in place so that the products move smoothly through the steps that create values. Pull recognizes the step of customer calling output from the previous step on demand (Hopp and Spearman, 2004). There is the need for perfection, which requires constant striving to meet the needs of the customer and improve the processes with zero defects.
“Lean production is most frequently associated with the elimination of waste commonly held by firms as excess inventory or excess capacity (machine and human capacity) to ameliorate the effects of variability in supply, processing time, or demand,” (Shah and Ward,2007). Anupindi et al. (1999) observe that based on Little’s law, a firm might be able to reduce inventory in its manufacturing system either by keeping over capacity or by reducing process time. Excess capacity is a type of waste and is against the adoption of lean principles to manufacturing strategy. Therefore, the adoption of the technique of lowering throughput time for reducing inventory is the preferred method. Lowering of throughput time can be accomplished by following the continuous or one-piece flow without frequent stop and go flow process, which is the characteristic of traditional manufacturing systems of batch and queue systems. Continuous workflow can be achieved by developing a “flexible, dedicated and engaged workforce.” Therefore, pursuing a lean manufacturing strategy and minimizing inventory, firms have to handle variability in supply, variations in processing time and demand (Hopp and Spearman, 2004: De Treville and Antonakis, 2006). This also requires firms to manage their social and technical systems effectively and simultaneously.
“To manage variability in supply, processing time, and demand, firms pursuing lean production must become attentive to them and the underlying causes” (Shah and Ward, 2007). According to Womack et al. (1990), in order to manage variability in supply, processing time and demand
Waddington et al. (2001) observe that the advantages of lean can be better derived in situations of low demand, where cost is the main determinant for winning orders. Hobbs (2003) states “lean manufacturing methodologies are a series of techniques that allow product to be produced one unit at a time, at a formulated rate, while eliminating the non-value-adding time, queue time or other delays” (p. 23). Lean principles can be applied to the total manufacturing chain, which extends from product design and development until the completion of manufacturing. In some cases, it even embraces distribution (Cooney, 2002). Kilpatrick (2003) reports that lean are the systematic identification and elimination of waste through continuous improvement and this improvement can be achieved using the pull production leading to perfection. “Lean is a manufacturing philosophy that shortens the lead-time between a customer order and the shipment of the parts ordered by the elimination of all forms of waste” (Manos, 2002).
“The benefits of lean manufacturing are evident in factories across the world and companies report improved product quality, reductions in cycle time, reduced work-in-progress (WIP), improved on-time deliveries, improved net income, decreased costs, improved utilization of labor, reduction in inventories, quicker return on inventory investment, higher levels of production, improved flexibility, improved space utilization, reduction in tool investment, a better utilization of machinery, stronger job focus, and better skills enhancement” (Pavnaskar et al., 2003 quoted in).
Sanchez and Perez (2001) have established different principles and techniques while framing the conceptual framework for lean production.
Lean manufacturing focuses predominantly on one-piece flow or continuous flow. This implies that the ideal batch size for lean production is fixed differently from the traditional manufacturing process, where it is based on individual manufacturing processes or the ability of production to handle materials. Marcado (2007) reports that one-piece flow needs work cells, which are organized based on the product rather than process.
In the lean manufacturing process for reducing cost and improving customer value, waste is a crucial issue that needs to be focused on. Liker (2004) argues that in manufacturing “a process is seen as a time line of activities, material and information flows,” in which the amount of waste is far in excess of the value-added activity. There are different elements, which form part of the lean manufacturing process and which help in enhancing customer value when lean manufacturing strategies are implemented. The following section discusses the issue of waste and its implications in lean manufacturing.
From a practical perspective, one of the assumptions made by the Lean management concept is that organizations are comprised of processes. Therefore, any improvement made in a Lean context is most likely to optimize the process, which represents the journey of the customer towards the product of the organization, rather than increasing the efficiency of the individual departments. This perspective is the widely accepted “process-based view” of the organizations.
Womack et al. (1996) report the objective of lean production is the elimination of every action in the production process that does not enhance value to the produced items. For example, the accumulation of inventories represents a symptom of inefficiency in a firm’s operations, because inventory does not add value to the products (Sanchez and Perez, 2001). “Furthermore, inventories also hide other problems on many occasions, preventing their solution like, for example, a defective maintenance that focuses the accumulation of stocks to prevent bottlenecks in the machines which break down frequently.” Therefore, the focus of lean manufacturing is centered towards reducing inventories of raw materials and finished goods stored by the firm. This concept implies that excess inventory makes the firm incur an additional cost, which ultimately increases the cost of production. Just in Time (JIT) has been recognized as one of the effective management strategies for ensuring continuous improvement, in which the organization will be able to identify non-value adding activities and remove them to reduce costs and improve quality.
Lean Manufacturing Strategy and Organizational Performance
Organizations are in a position to build a competitive advantage by ensuring superior manufacturing or service delivery. However, organizations face tough challenges in sustaining their competitive advantage over time. This calls for the implementation of several manufacturing strategies, which are not only innovative but also could work towards minimization of the cost. “The increasing pace of technological change and the accelerating globalization of business has meant that competitive advantage for many corporations now lies in their ability to effectively implement on-going product, service, and process innovations.” Lean manufacturing, a system derived from the operation of the Toyota Production System, has been seen by many leaders and managers as a key management technique, which helps firms, improve their competitive advantage. Educating employees and managers in engaging effective strategies in product and design capabilities is one of the essential prerequisites for the successful implementation of lean manufacturing strategies.
Many manufacturing operations have been made to adopt the principles of lean manufacturing and these principles have been successfully applied in many disciplines of service delivery (Poppendieck, 2002). According to Shah and Ward (2007), lean manufacturing focuses on the elimination of seven different types of waste “to ameliorate the effects of variability in supply, processing time or demand.” Shah and Ward (2003) observe that lean manufacturing has been developed as an integrated system. This system is comprised of elements, which are highly interrelated with each other. There is a wide variety of manufacturing practices including “just in time, (JIT), quality systems, work teams, cellular manufacturing,” which facilitate the implementation of lean manufacturing strategies. Implementation of lean manufacturing principles enables organizations to enhance their productivity and reduce the lead-time for production and delivery as well as a reduction in the cost of production. Significant improvement in the quality of products is also experienced by the engagement of lean manufacturing (Karlsson and Ahlstrom, 1996). Being an integrative concept, the adoption of the lean manufacturing concept presupposes the operation of a set of key areas or factors. These key areas represent a broad array of practices, which are assumed critical for the implementation of lean principles. Wong et al. (2009) identify these factors as “scheduling, inventory, material handling, equipment, work processes, quality, employees, layout, suppliers, customers, safety and ergonomics, product design, management and culture and tools and techniques.”
Despite significant benefits resulting from the application of lean management principles and practices as highlighted by theory, not many companies are able to implement the system successfully in reality. There are numerous challenges faced by firms in the implementation of lean manufacturing. Many researchers are of the opinion that the misunderstanding of the real concept of lean manufacturing and its purpose is the main cause for the failure of lean manufacturing. According to some of the researcher’s cultural differences, which occur during transition or translation of lean manufacturing is the main reason for the misunderstanding of the concept of lean. There may arise further challenges such as piecemeal adoption of lean tools and techniques because of the presence of this type of misunderstanding. There may also be a lack of development of effective lean culture to support the successful implementation of lean manufacturing strategies. Studies show that a company, which is in the initial stages of implementing lean manufacturing strategies, must maintain an effective communication process at all levels for ensuring successful implementation of the lean strategies. A good communication process is an essential prerequisite for the effective implementation of lean manufacturing strategies.
Group Technology as a Lean Manufacturing Strategy
The recent problems associated with the manufacturing of products such as “stagnation, energy crisis, pollution, skillful labors, rapid changes in product design and technical innovation” necessitate the production systems to implement effective systems to eliminate waste and redundancies to improve the manufacturing performance. “The development of manufacturing systems and changes and variety of customers’ interests, push companies to produce various products with high capacities. Therefore, manufacturing systems must be changed from job shop and mass production systems to new systems” (Shahin & Janatyan, 2010). In this context, many of manufacturing companies have started adopting Group Technology (GT). “It is the best production system to produce various products in large amounts with high productivity” (Shahin & Janatyan, 2010). Nomden and Van der Zee (2008) developed a new concept of “Cellular Manufacturing” as an application of Group Technology. Cellular manufacturing assumes
“physical groupings of machines, each grouping or cell is dedicated to the manufacturing of a product family. The similarities in manufacturing requirements for members of a product family lead to reduced set-ups, less material handling, and more. However, instead of a physical re-allocation of machines, CM-VCM aims to reduce set-up times by grouping similar jobs in production planning and control. Considering the literature review, it is concluded that it seems most of investigations assume GT and CM as synonyms. Although in such resources, CM is addressed as a technique of lean manufacturing, it also seems to be one of the principles of GT is described as physical groupings of machines, each grouping or cell being dedicated to the manufacturing of a product family (Nomden and Van der Zee, 2008)” (Shahin & Janatyan, 2010).
Group Technology can assist firms in achieving the goals of lean production. Shahin and Janatyan (2010) attempted to develop a conceptual model establishing the relationship between GT and lean manufacturing. This model is developed based on the possible impacts of GT on lean production.
First, the part family element of GT concept, in which grouping, classifying and coding of products is undertaken helps in the implementation of the lean manufacturing system. The processes of grouping, classifying and coding involved in GT provide the basis for the identification of products rapidly in the system. This grouping function to reduce the time for preparation, storing, takt time and lead-time and such reduction empowers the operation to contribute to reducing over production. Reduction of excess or over production leads to elimination of waste, which is one of the main objectives of lean production and in turn, productivity is increased.
Second, GT facilitates design conformance, which enhances the application and utility of lean manufacturing strategies. “After grouping the products and constituting part families, an important step is, reviewing the design and refining the design information and justifying the design” (Shahin & Janatyan, 2010). During this time, the justification of design also takes place. “Design conformance includes standardizing process plan, scheduling for groups of products, grouping tools, equipment and improving inventory purchasing requirements,” (Shahin & Janatyan, 2010). These tasks can be expected to reduce operation time and they will contribute to a reduction in work in process inventories. There will be a possible improvement in material handling and an increase in the power of operation leading to an increase in the overall organizational efficiency. “Group scheduling can reduce the time of the process (lead time and takt time) by grouping tools; and equipment and applying proper jig and fixtures to the part family can reduce the setup time” (Shahin & Janatyan, 2010). These two activities when undertaken will lead to the elimination of extra movements, redundancies and unnecessary processes. This will eventually lead to the designing of the jig and fixtures in such a way that makes the work easy for labor. It avoids complexity in the system and improves inventory procurement routines. In addition, there will be a decrease in the size of batch material and space requirement in the system. All these will result in further reduction of inventories and complexities. Reduction in extra movement and redundancies, which are the waste elimination objectives of lean manufacturing are greatly achieved by the design conformance element embedded in GT. When there is a possible reduction in the addressed elements, it will go to increase the productivity of the system.
Third, GT contributes to enhanced automation in production, which improves the utility of lean manufacturing strategies. Computer-Aided Designs (CAD) and Computer-Aided Manufacturing (CAM) consisted in Computer Integrated Manufacturing (CIM) enables the application of GT with a bank of computerized information including design, production and management information. CIM works to integrate computing technology and manufacturing to gain improvement in productivity and quality. “Automated factory systems are increasingly using new technologies such as direct numerical control systems, computer numerical control machines that control the production processes by a central computer. These mechanisms can improve quality because of reducing defects and errors and eliminating waste in a lean production system.”
Manufacturing Strategies for Developing Countries
In both industrially advanced countries and developing countries, manufacturing firms are made to face considerable changes in their manufacturing strategies. These changes are necessitated by “mass customization, shortening product life cycles, increasing technological change and the entry of international competitors” into the markets of these countries. Developing countries face a situation in which the markets for products and services are becoming increasingly international. This situation is faced in the automobile manufacturing and electronics industry among other manufacturing areas. Since firms have to meet to the demands of international markets or globalization, they need to adopt strategies, which are more international in nature. At the same time, firms have to ensure that the organizational culture is adapted to the local conditions, so that firms can take advantage of implementing the new manufacturing strategies. In this context, it is to be mentioned that globalization affects manufacturing both at the local level and at the international level. Globalization has widened the marketplace and has resulted in increased competition. With the increased demand and widening of the marketplace, customers place greater demands on the firms to enhance “quality, serviceability, and flexibility.” At the same time, they have the pressure to keep the costs low.
This review found that Hill (2000) has identified several order qualifiers and order winners in the context of competing priorities. “Order qualifiers” represent the conditions, which a firm must comply to be regarded as a good supplier. “Order winners” represent the conditions, which will help the company to face competition effectively.
For providing order qualifiers, firms need only to meet the same characteristics and capabilities of the competitors. However, for providing order winners, firms need to be superior to their competitors. While developing order winners and qualifiers, firms must adopt different strategies for different marketplaces by the level of their importance. With the changes in market conditions, there have been several changes in the basis of competition. For example, quality has been considered more as an order qualifier, whereas other competitive criteria such as flexibility, responsiveness and innovation have become order winners. A number of empirical studies, which focused on the specific manufacturing strategies in the context of developing countries like Hungary, Brazil and Ghana, have been reported in the literature. Studies focusing on innovation as a manufacturing strategy, especially in the context of developing countries are limited. Nevertheless, innovation has become a strong competitive strategy to ensure firms produce superior quality and compete effectively in global markets. Developing countries focus mainly on achieving lower labor costs to achieve a competitive advantage over the competitors from industrially advanced countries. This attitude is typical for manufacturing firms while migrating to adopt advanced manufacturing strategies from traditional types of strategies. However, it must be remembered that labor cost advantage may vanish in a short period. Therefore, it is imperative that manufacturing firms search for alternative sources of competitive advantage. Innovation would serve as one of the manufacturing strategies, which provide manufacturing firms in developing countries adequate opportunities for matching the competitive strengths of the competitors from developed countries.
Based on the findings of Leong et al (1990), competitive priorities of quality, delivery, cost, flexibility and innovativeness can be considered critical in the context of developing countries. Many of the further studies on manufacturing strategies have included cost, delivery, flexibility and quality as the key components of manufacturing strategy. Therefore, the current study defines manufacturing strategy to include cost, delivery, flexibility and quality as the critical components of manufacturing strategy in developing countries.
In respect of competitive strategies, this study uses cost leadership and differentiation strategies, as these are the commonly used strategy dimensions by many of the studies reported in the literature. However, it is important to recognize the fact that firms operating in developing countries implementing differentiation strategy do not stop with focusing on a single dimension of differentiation but tries to include several dimensions such as image, customer loyalty, quality, innovation and level of service at the same time (Kim et al, 2004). Thus, firms adopting a differentiation strategy in a developing country will strive to create customer loyalty, by distinguishing their products by different and unique product image by undertaking intensive marketing and image management. Simultaneously, such firms will create products, which are innovative, durable and serviceable. Cost leadership, on the other hand, implies that firms would generate competitive advantage by achieving the lowest cost of production. Firms strive to achieve cost leadership by exercising stringent cost control and improving efficiency in all functional areas of operation (Porter, 1980).
The following figure represents the conceptual model in respect of the manufacturing and competitive strategies that might be adopted by the firms in developing countries.
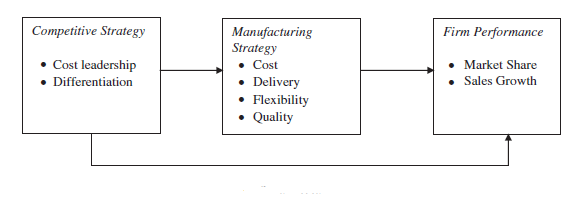
From the figure, it may be observed that manufacturing strategy directly affects the firm performance and it has an additional effect on firm performance because of the impact of the competitive strategies acting on it. This relationship in the context of a developing country might hold well, because for the manufacturing firms to achieve success in improving their performance must ensure a consistency between the competitive and manufacturing strategies with competitive strategies driving the manufacturing strategies. For example, the model developed by Ward and Duray (2000) has proposed that competitive strategy has an influence on the manufacturing strategy.
Study by Amoako-Gyampah, & Acquaah, (2008) of manufacturing strategy in Ghana, has found that among the four manufacturing strategy components – cost, quality, flexibility and delivery – low-cost manufacturing strategy appeared to have the strongest link with cost leadership strategy. This finding was in agreement with the earlier findings of Ward and Duray (2000). The findings of the study in Ghana reveal that manufacturers following a cost leadership strategy must necessarily implement a low-cost manufacturing strategy to become successful. In any developing country, the manufacturers cannot ignore the other components of the manufacturing strategy. Firms have to ensure the quality of the products and providing reliable deliveries would not only reduce the expediting costs and inventory-related costs but also will improve the customer relationship and reputation of the firms.
Implementation of lean production as a manufacturing strategy in developing countries may face some barriers in the form of employee resistance because of differences in the national and organizational culture, lack of understanding and awareness of lean systems, lack of effective communication and inadequate attention and involvement of top management. While larger firms in the developing countries are operationally complex with centralized decision-making, smaller firms suffer from financial and human resources constraints to implement lean manufacturing strategies. Because of these constraints, firms in countries like China or India are unable to grow as rapidly as the firms do in the United States. Frequent supply interruptions for want of infrastructure facilities prohibit manufacturing companies from adopting lean manufacturing strategies. Lack of educated workers and poor infrastructure are the other constraints for adopting lean principles in manufacturing. Diffusion of technology for making lean a success is slow in developing countries and legal and institutional frameworks may not provide any incentives to the firms to adopt best industry practices. For example, the employer may be barred from adopting a performance-based employment policy or firing erring employees may be difficult because of the prevalence of labor laws favoring employees. Because of these and various other constraints, lean manufacturing has been found to be adopted less in the context of developing countries.
Conclusion
The foregoing discussions indicate a serious gap in the literature about the role of lean manufacturing as a successful manufacturing strategy. This review focused on various facets of manufacturing strategy and its relationship with competitive strategy, along with a detailed discussion on lean manufacturing strategy. The review also found a strong relationship between competition and manufacturing strategy. Based on the discussions, it is reported that successful differentiators in developing countries need to pursue a portfolio of manufacturing strategies to make their product offerings unique in the marketplace. Along with different ways to differentiate their products, firms may use their manufacturing resources to enhance their strategic thrusts in a selective way.
References
Abernathy, W.; Clark, K. (1985). Innovation: Mapping the Winds of Creative Destruction, Research Policy, 14, pp. 3-22.
Amoako–Gyampah, K. & Acquaah, M. (2008). Manufacturing strategy, competitive strategy and firm performance: An empirical study in a developing economy International Journal of Production Economics, 111 (2), 575-592.
Banker, R.D., Chang, H.-H., Majumdar, S.K., (1996). A framework for analyzing changes in strategic performance.Strategic Management Journal 17, 693–712.
Bond, T. C. (1999), “The role of performance measurement in continuous improvement”, International Journal of Operations and Production Management, Vol. 19, No. 12, pp. 1318-1335.
Bourne, M.; Kennerley, M. and Franco-Santos, M. and (2005), “Managing through measures: a study of the impact on performance”, Journal of Manufacturing Technology Management, Vol. 16, No. 4, pp. 373-395.
Chenhall, R. (2005), “Integrative strategic performance measurement systems, strategic alignment of manufacturing, learning and strategic outcomes: an exploratory study”, Accounting, Organisations and Society, Vol. 30, No. 5, pp.395– 422.
Cool, K., Schendel, D., (1987). Strategic group formation and performance: the case of the US pharmaceutical industry, 1963–1982. Management Science 33 (9), 1102–1124.
Cox, J.F., III, and Blackstone, J.H., Jr., eds. (1998), APICS Dictionary, Ninth Edition, Alexandria, VA: APICS.
Dangayach, G.S. and Deshmukh, S.G. (2001) ‘Manufacturing Strategy: Literature Review and Some Issues’, International Journal of Operations and Production Management 21(7): 884-932.
Dierickx, I. and Cool, K. (1989). “Asset Stock Accumulation and Sustainability of Competitive Advantage”, Management Science. 35: 1504-1511.
Ferdows, K., de Meyer, A., (1990). Lasting improvements in manufacturing performance: In search of a new theory. Journal of Operations Management 9 (2), 168–184.
Fernandes, K.; Raja, V. and Whalley, A. (2006), “Lessons from implementing the balanced scorecard in a small and medium-size manufacturing organization”, Technovation, Vol. 26, No. 5/6, pp. 623-634.
Fine, C.H. and Hax, A.C., (1985), Manufacturing in a New Perspective, Working Paper No. 86/42, Insead, Fontainebleau.
Franco-Santos, M. and Bourne, M. (2003), “Factors that play a role in managing through measures”, Management Decision, Vol. 41, No. 8, pp.698–710.
Gupta, Y. P. and. Lonial S. C. (1998). Exploring linkages between manufacturing strategy, business strategy, and organizational strategy. Production and Operations Management, 7(3), 243-264
Harrison, J. and Boyle, E. (2006), “Falling into capability learning traps: the role of the firm’s predominant managerial mental models”, Management Decision, Vol. 44, No. 1, pp. 31-43.
Hayes, R.H. and Wheelwright, S.C. (1979), Linking manufacturing process and product lifecycles”, Harvard Business Review, January-February, pp. 133-40.
Hayes, R. and Wheelwright, S.C., (1984). Restoring Our Competitive Edge, The Free Press, New York, NY.
Hill, T.J. (1985), Manufacturing Strategy, Macmillan, Basingstoke.
Hill, T., (1993). Manufacturing Strategy – The Strategic Management of the Manufacturing Function, 2nd ed., Macmillan Press, London.
Hill, T. (1994), Manufacturing Strategy: Text and Cases, 2nd ed., Richard D. Irwin, Homewood, IL.
Hopp, W. J. and M. L. Spearman., (2004). “To pull or not to pull: What is the question?” Manufacturing Service Operations Management 6(2): 133-148.
Innis, D.E., LaLonde, B.J., (1994). Customer service: the key to customer satisfaction, customer loyalty, and market share. Journal of Business Logistics 15 _1., 1–28.
Kim MK, Park MC, Jeong DH (2004). “The Effects of Customer Satisfaction and Swithching Barrier on Customer Loyalty in Korean Mobile Telecommunication Services”, Telecomm. Policy, 28(2): 145-159.
Karlsson, C., Ahlström, P. (1996). The difficult path to lean product development. Journal of Product Innovation Management 13. 283-295.
Karlsson, K., Tesfamariam, D., (2004). “Manufacturing strategy linked to manufacturing system flow principle” Submitted to the 7th CIRP International Seminar on Manufacturing Systems (ISMS-2004), Digital Enterprises, production network 2004.
Koufteros, X.A., (1995). Time-Based Competition: Developing a Nomological Network of Constructs and Instrument Development. The University of Toledo, Toledo, OH.Leong, G.K., Snyder, D. & Ward, P.T. (1990). Research in the process and content of manufacturing strategy.
Liker, J.K.(2004). The Toyota Way: 14 Management Principles from the World’s Greatest Manufacturer, McGraw-Hill, New York.
Martins, R.A. (2000). “Use of performance measurement systems: some thoughts towards a comprehensive approach” In: Neely, A. (Ed.) Performance Measurement – Past, Present and Future, Centre for Business Performance. Cranfield, 363-370..
Miller, D. & Friesen, P.H. (1983). Strategy making and environment: The third link. Strategic Management Journal, 4, 221-235.
Miller, J.G., Roth, A.V., (1994). A taxonomy of manufacturing strategies. Management Science 40, 285–304.
Najmi, M.; Rigas, J. and Fan, I-S. (2005), “A framework to review performance measurement systems”, Business Process Management Journal, Vol. 11, No. 2, pp. 109-122.
Narasimhan, R., M. Swink and S. W. Kim., (2006). “Disentangling leanness and agility: An empirical investigation.” Journal of Operations Management 24(5): 440-457.
Neely, A.D., Mills, J.F., Platts, K.W., Gregory, M.J and Richards, A.H. (1994). Realizing strategy through measurement. International Journal of Operations and Production Management, 14, 140–152.
Noble, M. A. (1995), Manufacturing Strategy: Testing the Cumulative Model in a Multiple Country Context. Decision Sciences, 26: 693–721
Nomden, G. & Zee, D. (2008). Virtual cellular manufacturing: Configuring routing flexibility. International Journal of Production Economics, 112(1), 439–451
Ohno, T., (2008). “Workplace Management”, Productivity Press, Portland, OR.
Paranjape, B.; Rossiter, M. and Pantano, V. (2006), “Insights from the Balanced Scorecard Performance measurement systems: successes, failures and future – a review”, Measuring Business Excellence, Vol. 10, No. 3, pp. 4-14.
Platts, K.W. and Gregory, M.J., (1988).Competitive Manufacturing: A Practical Approach to the Development of a Manufacturing Strategy, IFS, London.
Platts, K.W.(1990),’ Manufacturing audit in the process of strategy formulation’, Ph.D. thesis, Manufacturing Engineering group, Engineering Department, University of Cambridge,1990.
Platts, K.W. (1994), Characteristics of methodologies for manufacturing strategy formulation’’, Computer Integrated Manufacturing Systems, Vol. 7 No. 2, pp. 93-9.
Poppendieck, M., (2002). “Principles of lean thinking”, Technical Report, Poppendieck. LLC, USA.
Porter, M. E., (1980). Competitive strategy: techniques for analyzing industries and competitors. New York: Free Press.
Sánchez, A.M. and Pérez, M.P., (2001). “Lean indicators and manufacturing strategies”, International Journal of Operations & Production Management 21, pp. 1433-1451
Shah, R. and P. T. Ward., (2003). “Lean manufacturing: Context, practice bundles, and performance.” Journal of Operations Management 21(2): 129-149.
Shah, R. and P. T. Ward., (2007). “Defining and developing measures of lean production.” Journal of Operations Management 25(4): 785-805.
Shahin Arash & Janatyan Nassibeh, (2010), Group Technology (GT) and Lean Production: A Conceptual Model for Enhancing Productivity, International Business Research, Vol 3 No 4.
Skinner. (1969). Contingencies of Reinforcement. Englewood Cliffs, N.J.: Prentice-Hall.
Slack, N., (1994).“The importance-performance matrix as a determinant of improvement priority”, International Journal of Operations and Production Management, Vol. 14 No. 5, pp. 59-75.
Slack, N., Chambers, S. and Johnston R. (2004) Operations Management (4th Edition), Harlow: Pearson Education.
Sousa, S.; Aspinwall, E. and Rodrigues, A. (2006), “Performance measures in English small and medium enterprises: survey results”, Benchmarking: An International Journal, Vol. 13, No. 1/2, pp. 120-134.
Swamidass, P., Newell, W., (1987). Manufacturing strategy, environmental uncertainty, and performance: A path analytical model. Management Science 33 (3), 509–534.
Venkatraman, N.,(1989). “The Concept of Fit in Strategy Research: Toward Verbal and Statistical Correspondence,” Academy of Management Review (14:3), pp. 423-444.
Vickery, S.K., Droge, C., Markland, R.E., (1993). Production competence and business strategy: do they affect business performance? Decision Sciences 24, 435–455.
Ward, P.T., Bickford, D.J., Leong, G.K., (1996). Configurations of manufacturing strategy, business strategy, environment and structure. Journal of Management 22, 597–626
Ward, P.T., Miller, J.G., Vollmann, T.E.(1988),’Mapping Manufacturing Concerns and Action Plans’, International Journal of Operations and Production Management, Vol.8, No.6. pp.5-18.
Ward P. (2000), Manufacturing Strategy in Context: Environment, Competitive Strategy and Manufacturing Strategy, Journal of Operation Management, Vol. 18 (2) pp 123-138.
Wheelwright, S.C. (1978), Reflecting corporate strategy in manufacturing decisions”, Business Horizons, February, pp. 57-66.
Williams, F.P., D’Souza, D.E., Rosenfeldt, M.E., Kassaee, M.,(1995). Manufacturing strategy, business strategy and firm performance in a mature industry. Journal of Operations Management 13, 19–33.
Womack, J. P. and D. T. Jones., (1996). Lean Thinking. New York, Simon & Schuster.
Womack, James, Jones Daniel and Ross, Daniel; (1990); The machine that changed the world; New York, USA.
Wong, Y.C., Wong, K.Y. and Ali, A., (2009). “Key practice areas of lean manufacturing”, Proceedings of the International Association of Computer Science and Information Technology Spring Conference (IACSIT-SC 2009), Singapore, pp. 267-271