Executive summary
In the case study, the challenges in the quality strategy of Coca-Cola Company resulted in a lot of health problems such as nausea, headache, vomiting, stomach pain and shivering in children. Improved quality strategy for the company relates to product design, manufacturing process that involves tasks such as product analysis, packaging, and service delivery to the clients. For quality improvement, strict adherence to GMP, IMCR, and PIOC health standards as well as the reduction of calories in the coke products should be done on all Coca-Cola products. The new coca-cola quality strategy should be focused on the use of appropriate raw materials such as coal and use of efficient and very controlled heating and cooling systems. It is also important to reassess and readjust the existing company standards, quality specifications and division auditing practices.
Introduction
Over the years, the Coca-Cola Company, the globally recognised major manufacturer of alcohol free beverages, syrups and beverages has continued to have very outstanding and impeccable product quality standards. As a soft drink company that has a global presence and a monopoly in many countries’s soft drink industry, the existence of competitors such as Pepsi has compelled the company to initiate more strategic and extremely customised product quality standards. Some of the Coca-Coca products include Odwalla, Sokenbicha, Nestea, Glaceau VitaminWater and the Dasani. The evaluation of poor quality standards and many health related threats demands that a new quality strategy be put in place.
Challenges in the case
The case study reveals the existence of a lot of ambiguities in the Coca-Cola products quality enhancement strategy. The two recalls revealed major quality concerns that clearly indicated that proper planning and allocation of resources aimed at improving the company’s quality control procedures were needed. The problems that emerged with regard to the company’s products included unusual taste and odor of the coke products (Samuelson & William, 2004). The packing of the products had limitations that hindered cost effective marketing of the coke products.
The poor quality of coke products heavily contributed to the increased complains and health concerns such as nausea, headache, vomiting, stomach pains, shivering, and other minor complications. Poisoning emerged to be a major health concern. It had been caused by the consumption of the Coca-Cola soft drink products. The poisoning was reported to have occurred in different countries that include Belgium, France, Spain and Luxembourg. This fact dictates that a lot of quality concerns that relate to the company products packaging and quality needed to be assessed. Failure to quickly recall the Coca-Cola drinks in a timely manner before more people could consume the products was a major failure of the company. If the recall had been done in time, then it would have reduced the damages caused and thus safeguarded the integrity of the company’s top level managers and the entire business processes.
The recall of the Coca-Cola products triggered other worries that had not been foreseen by the Coca-Cola Company’s quality department. This concept was a sure indicator that the Coca-Cola products such as Sprite, Fanta, Coke and Diet Coke needed to be accorded proper attention in order to ascertain possible quality problems that could have otherwise led to a major decline in its competitive advantage in the market. The success of the company and enhancement of its competitive strategy is highly dependent on its supply of high quality product design, packaging and service delivery to the clients. Consistency and reliability of the Coca-Cola Company’s products remains fundamental to the success of the Coca-Cola Company and its enhancement of its competitive advantage.
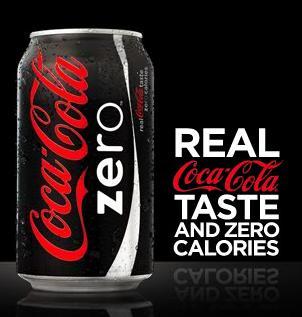
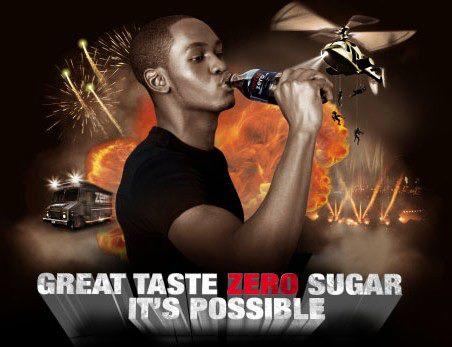
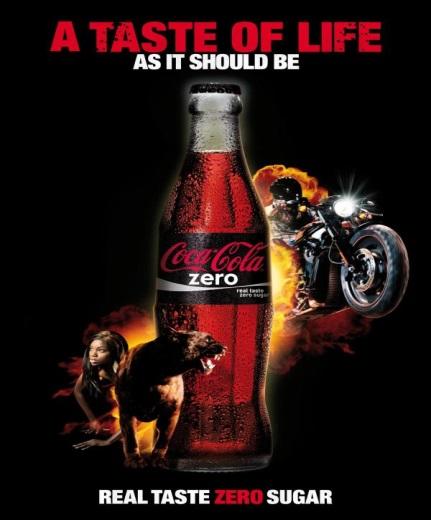
The Coca-Cola Operating Requirements (KORE) used across the globe should be analyzed so as to identify any possible problems that could be the source of any health problems. The Coca-Cola Management System (TCCMS) was replaced in the year 2010. KORE should always be assessed and aligned to any existing health concerns. Integrated quality management strategies of the company should be enforced at all times and should not be limited to situations when dire quality concerns emerge. The relevance of the company’s quality standards should be assessed, implemented, documented and regularly assessed to ensure that such quality enhancement practices are in line with the KORE quality standards. Besides ensuring that the rating of the company’s products on the global product quality index improves, the company should also assess the actual quality standards of the company products.
The measurement of unique product and coca-cola quality through the focus on the company products, materials, ingredients, and regulatory manufacturing requirements, the bottling and distribution of the products should keenly be done. In the long run, consistent product quality is crucial and vital to the success of the company and restoration of clients trust. Coke’s quality strategies revolve around the enhancement of brand differentiation, attractive brand name and provision of alternative choices in the company’s products offered by the company. As the largest global juice and soft drink company, maintenance of high standards of quality in the ever evolving soft drink business environment, Coke quality standards need to be amended. The company should undertake a critical analysis and in-depth focus on fully meeting the needs and expectations of consumers besides producing products that are in line with the ever increasing regulatory requirements.
Recommendations for a Better Coke quality strategy
To ensure that the above quality challenges do not occur again, a number of improvements on the company quality strategy need to be undertaken. With regard to the need to ensure that a high level of quality of products would be assured, it is crucial that the Coca-Cola Company quality management become keener in its quality enhancement strategies. Strict adherence to GMP is an important quality strategy that would improve Coca-Cola products and make sure that product health problems are forever solved. Diversification of the coke product portfolio is crucial. However, such diversification must be undertaken with keen interest paid to the impact of such diversification strategies to the overall outcome of the coke products. Simpler portfolio, consistent quality, argumentation of loyal consumers and fully trusted quality standards should be implemented with the view of fostering quality standards.
Risk assessors should not only engage the use of insurance companies, shareholder participation, capital markets and the global banking sector but rather employ security, health, wellness and fitness analysts that would identify both real and perceived issues that could degrade coke’s quality standards. Implementation and devotion to strict food policies should be undertaken by the top level managers of the Coke Company. This concept should be aligned to the identified quality priorities and food and safety governance mechanisms already put in place by the Coke Company with the view of improving consistency in its products’ safety. The standards of laboratory process should be keenly assessed and proper improvement mechanisms implemented. Governance and oversight of the coke laboratory processes should be objectively done and focused on eliminating any possible quality problems. This process would help to detect the slightest presence of food poisoning at Antwerp, Dunkirk and other British Coca-Cola plants.
Safety of products should be improved by ensuring that IMCR standards and PIOC health and wellness standards are thoroughly checked before any product is declared good for consumer consumption. The rate at which system checkup and auditing of the manufacturing processes is done should also be increased. The auditing should be focused on ensuring that customers’ demands are addressed and that all capability and calibration standards are fully adhered to. The company standards, quality specifications and division audits should be reassessed and readjusted so as to enhance a greater and more powerful level of efficiency and improved product standards (Gomez, David & Robert, 2008).The reduction of calories in Coke’s products should not be limited to the Coke Zero brand but rather to all Coca-Cola products and affiliate companies’ goods and services. Efforts to reduce obesity levels of the clients by the company should never be seen as a favor to the clients but rather as part of the company’s wide operational strategy aimed at reinforcing the significance and objectivity of the Coke Zero product. The choice of appropriate Coke’s raw material such as coal and controlled heating and cooling systems is necessary.
This would help in the realization of a high level of efficiency and products’ cost effectiveness. Where it is deemed necessary, the company’s quality strategy should be amended to ensure that more auditing sessions are undertaken and that many microbiology experts and chemical analyst are employed with the view of improving devotion to lean operations. This process would ensure reliable and clear product calibration and transparent quality selection capability. This fact should ensure that the company quality strategy is able to effectively identify the most critical quality requirements of environment, safety and quality. Chemical analysts should not only be restricted to the combination of ingredients but should also be used at nearly all levels of business operations. The company should endeavor to hire more chemical analysts to do test and re-tests of the Coca-Cola products. The quality strategy would be of great importance as it would reduce error rate and also eliminate the unnecessary costs incurred whenever a product recall is done by the company. Internal and external product capability should also be improved and streamlined so as to enhance consumer trust and loyalty to the products offered by the Coca-Cola Company. Regular quality checks should be undertaken by quality product analysts. The process would help to reduce the degree to which health concerns are raised and products recalled by the company due to poor quality and failure to meet required health standards (Andrew & Andrew, 2008).
Conclusion
Quality management is evidently an important aspect of Coca-Cola business operations. To enhance the company’s quality standards and reduce error rates, the Coca-Cola Company needs to be more focused on meeting consumer expectations and market demands. It is crucial that the operations of the company be fully be aligned to the most effective and reliable health standards with the view of safeguarding the health and wellness of the company’s clients. The concept is necessary in ensuring that only realistic and truthful product advertisements should be used. The use of an integrated quality management, effective and reliable quality enhancement standards is important to the operations of the company and avoidance of future quality and health issues.
References
Andrew. C., & Andrew, S. (2008).The Foundations of Positive and Normative Economics. Oxford, UK: Oxford University Press.
Gomez, M. R., David, B. B., & Robert L. C. (2008). Management: People, Performance, Change, 3rd edition. New York, USA: McGraw-Hill.
Samuelson, P.A., & William D. N. (2004). “Economics“, The Process of Economic Growth, 27, 634-636.