Toyota Motors Corporation, which was founded in 1937, remains to be one of the world leaders in the automotive industry (Borkowski 2013). The key strength of Toyota that makes it profitable and competitive in the industry and market is its focus on technology and innovation in all spheres of the company’s development, including processing and sharing information (Information systems 2012). The purpose of this brief is to critically evaluate the information management business model of Toyota with reference to its benefits and weaknesses for influencing the company’s competitive advantage.
Background
Toyota supports its profitability with the focus on implementing innovative technologies for information systems and approaches to lean information management. In the 1980s-1990s, Toyota developed the office automation and improved business application strategies with the help of applying CAD/CAM systems (Coetzee, Van der Merwe & Van Dyk 2016). In the 2000s, the company’s information systems based on the idea of lean management were advanced to address Toyota’s reformation of the management structure in the company. IC network systems were changed with TCP/IP-based systems (Information systems 2012). These approaches allowed Toyota to develop an effective competitive strategy. It is based on the efficient data exchange in the company, the application of the Rational Unified Process to realise the architecture-centric method in managing data, the use of communication channels with suppliers, and the application of a simplified information sharing procedure (Information systems 2012; Toma & Naruo 2017). The current situation regarding the information management model used in Toyota is associated with these aspects of the lean system.
Findings and Evaluation of Toyota’s Information Management Business Model
The analysis of the corporate information indicates that Toyota has successfully applied the principles of lean information management as a basis for its business model. The concept of “lean” was introduced in the 1980s to describe Toyota’s approach to organising the production system and a manufacturing process (Clark 2016). Its main principles, such as the elimination of waste and optimisation of processes, were successfully applied to the company’s information networks (Coetzee, Van der Merwe & Van Dyk 2016). As a result, data outputs and reports are generated only if they are important for decision-making, information is shared only with target employees, real-time processing of data is used, and data waste is eliminated at the stages of input and output (Clark 2016; Hessman 2014). Figure 1 presents the details regarding the application of the lean information management system in Toyota.
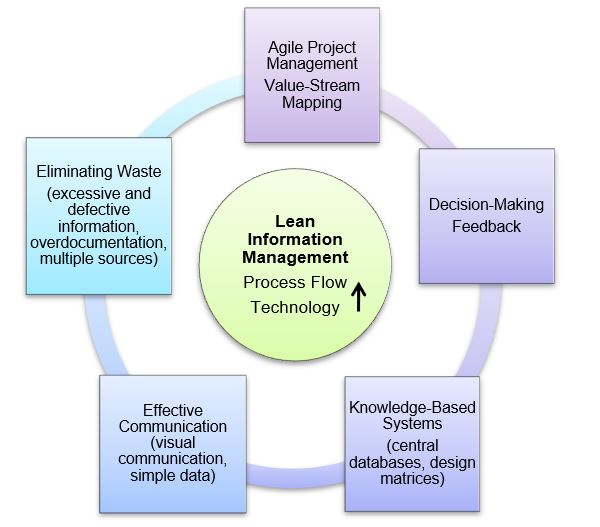
The lean information management allows for applying effective information sharing and communication strategies in Toyota to unite the company’s departments in one network.Several servers manage the work of the company’s IT network, allowing for the exchange of information between all departments and all Toyota’s units globally (Information systems 2012).A single internal information management system is used (Figure 2).
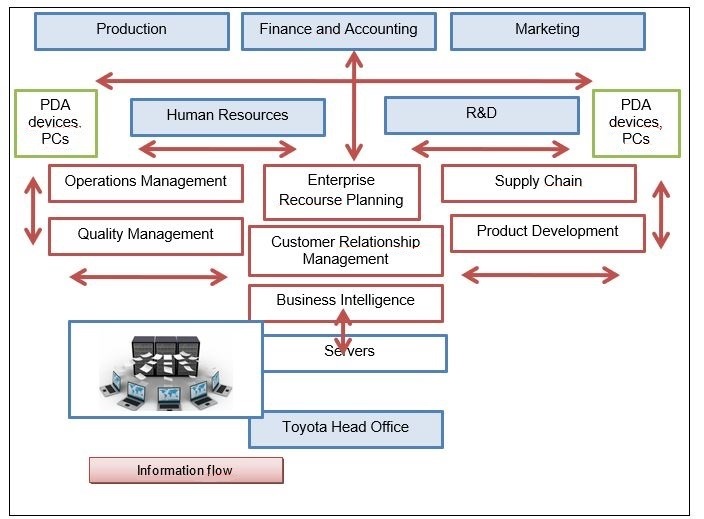
Being operated according to the lean management principle, Toyota’s IT system includes more than 1200 servers, more than 3000 applied CAD/CAM/ PDM systems, supplier and management databases, and internal knowledge bases (Information systems 2012). The information business model input and output include different types of data objects that are categorised as documents, reports, notes, accounts, and protocols (Figure 3). Volumes of information sets from all facilities and departments in Toyota are large, and the lean approach is followed to make the used process, technical, and human toolbox efficient (Amasaka 2013; Matsuo 2015). Data processing, tracking, and monitoring are realised in real time allowing for the immediate communication between departments (the web-based exchange of data). To process and monitor information with the focus on the lean management principles, Toyota applies the visual information management, standardisation of data, and training of users (Figure 3).
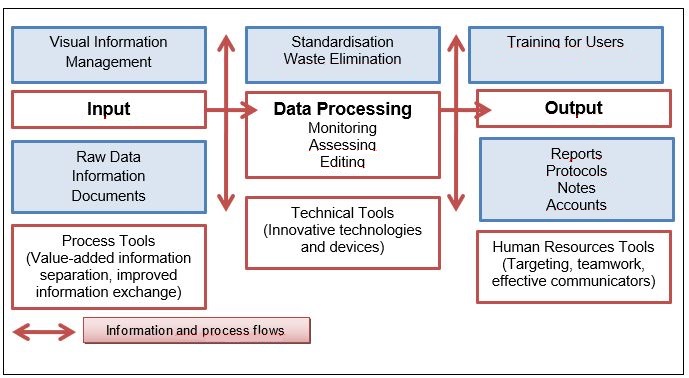
The lean information management system used in Toyota can be discussed as effective, and its elements are followed in many other organisations over the globe (Ota, Hazama & Samson 2013). The developed digital network uniting the company’s facilities and departments allows for communicating data and information efficiently without involving non-target persons or producing duplicates (Clark 2016). Thus, flexibility and traceability of this information management model are high. As a result, feedback and responses to problems in operations are received and shared immediately, and the problem is resolved within the shortest time to guarantee the quality of communication and operations (Information systems 2012).
However, there are some challenges in the system, which are associated with the used technology. Although Toyota focuses on applying the most innovative technologies to support its network, the application of CAD, CAM, and PDM systems can be a challenging task, and much attention should be paid to the systems’ integration (Toma & Naruo 2017). Still, the impact of the developed information management technology on business competitiveness of Toyota is positive as the company builds effective relationships with customers, suppliers, and partners because of the efficient management of data to avoid delays, barriers in information exchange, and errors in operations (Information systems 2012; Kobayashi 2014).
Recommendations and Conclusion
Toyota competes in the industry using advantages of its information technologies, but the applied model can be further improved with reference to the sustainability principle that is correlated with lean management. It is recommended to apply more tools to monitor and evaluate data processing to avoid errors and duplicates. Toyota’s case demonstrates that the use of technology in business and management systems is important to control operations, processes, data exchange, orders, and product cycles. Thus, the model allows for adding to the company’s competitiveness because the lean information management system allows Toyotato improve all processes while controlling output data, measuring results, and providing feedback to make the manufacturing process high-quality and efficient. As a result, the innovative information management system contributes to the company’s competitive advantage.
Reference List
Amasaka, K 2013, ‘The development of a total quality management system for transforming technology into effective management strategy’, International Journal of Management, vol. 30, no. 2, pp. 610-628.
Borkowski, S 2013, ‘Toyotarity.Term, model, range’, Production Engineering Archives, vol. 1, no. 1, pp. 2-5.
Clark, D 2016, ‘Quality improvement in basic histotechnology: the lean approach’, VirchowsArchiv, vol. 468, no. 1, pp. 5-17.
Coetzee, R, Van der Merwe, K & Van Dyk, L 2016, ‘Lean implementation strategies: how are the Toyota way principles addressed?’, South African Journal of Industrial Engineering, vol. 27, no. 3, pp. 79-91.
Hessman, T 2014, ‘Putting it in its place: Toyota’s high-tech production ballet’, Industry Week, vol. 263, no. 4, pp. 34-36.
Information systems 2012. Web.
Kobayashi, M 2014, ‘Relational view: four prerequisites of competitive advantage’, Annals of Business Administrative Science, vol. 13, no. 2, pp. 77-90.
Matsuo, M 2015, ‘Human resource development programs for knowledge transfer and creation: the case of the Toyota Technical Development Corporation’, Journal of Knowledge Management, vol. 19, no. 6, pp. 1186-1203.
Ota, M, Hazama, Y & Samson, D 2013, ‘Japanese innovation processes’, International Journal of Operations & Production Management, vol. 33, no. 3, pp. 275-295.
Toma, S &Naruo, S 2017, ‘Total quality management and business excellence: the best practices at Toyota Motor Corporation’, Amfiteatru Economic, vol. 19, no. 45, pp. 566-580.