Coca-Cola’s global supply chain and its vulnerabilities
In order to identify the weaknesses of Coca-Cola’s supply chain one should first briefly discuss its structure. This company incorporates more 500 hundreds brands, and its plants are located in different countries and continents. Additionally, many divisions of this corporation were previously separate organizations which only later merged with Coca-Cola. Therefore, these divisions can differ in terms culture, organizational structure, and, most importantly, quality management techniques. The main problem of this corporation is that it may not be able to take full control over the manufacturing process, storage, and transportation of their products. The problems which occurred at a Belgian bottling plant exemplify this situation. The contamination of carbon dioxide, which is used in their products, shows that this organization may lack important control mechanisms. It is possible to distinguish several points in their supply chain which are vulnerable to quality problems, namely: 1) bottling plants which plants which have to use the most up-to-date technologies in order to meet the standards of the company; 2) suppliers which must provide raw materials of the highest quality; 3) transportation companies that have to ensure that their products are not damaged; 4) warehouses and retailers which are responsible for the storage of beverages. Such a company as Coca-Cola cannot tolerate any quality issues because they normally result in multi-million losses. For instance, the decision to ban Coca-Cola products in a certain country or region can be catastrophic for this organization. This is why they should adopt methods which can eliminate quality defects. In the following sections we will discuss several quality management techniques and strategies which can help this company improve supplier quality management.
Juran’s quality trilogy and its application to the company’s problems
One of the methods which are often used by manufacturing companies is Juran’s trilogy. This method decomposes quality management into three activities, namely planning, control, and continuous improvement of quality. This technique is suitable for companies which manufacture technological products. The thing is that Joseph Juran believes that quality should be defined primarily from customers’ perspective (Ghobadian & Speller, 1994, p. 57). In his view, the quality can be defined as ability of the product to fit its purpose or use (Ghobadian & Speller, 1994, p. 57).
Certainly, this interpretation can useful, especially if we are speaking car manufacturing companies, service organizations, the producers of home appliances, and so forth. Nonetheless, it does not fully reflect the industry in which Coca-Cola operates. The beverages produced by this company have to comply with specific production standards and specifications; otherwise their products will simply be prohibited by those governmental agencies which are responsible for food control. By focusing only on customers’ needs, Coca-Cola can overlook some very important risks. Thus, Juran’s model cannot be fully adopted by the management of this corporation.
However, some of the steps outlined by Joseph Juran can be of great use to this company. For example, he urges management to form inter-departmental groups which analyze quality defects, indentify their problems, and propose certain solutions (Ghobadian & Speller, 1994, p. 58). Certainly, the underlying causes of quality defects may differ in various divisions of Coca-Cola; however, this approach will enable the company to better understand their causes. Additionally, Juran argues in favor of experiments which can show whether the company’s production process is susceptible to flaws (Ghobadian & Speller, 1994, p. 58). This method can be implemented at that Belgian bottling plant where Coca-Colas products were contaminated. Among other things advocated by Juran, one can mention the establishment of clear quality criteria which help to determine whether a product conforms to the requirements of the company. Juran pays special attention to the design of manufacturing process. According to him, the quality managers should empirically demonstrate this design eliminates quality defects.
Therefore, one can say that the model developed by Joseph Juran is not fully applicable to quality management of Coca-Cola supply chain. Nonetheless, some of his ideas can be very helpful, particularly when the company will analyze the problems and develop methods of eliminating them. Thus, it will be possible to use only some elements of his trilogy. Overall, the management of Coca-Cola should not overlook this model.
Crosby’s Zero Defects concept
Phillip Crosby’s zero defects methodology is one of the most widespread techniques implemented by modern companies. He lays stress on the prevention of quality problems rather than the inspection which normally takes place after the event (Ghobadian & Speller, 1994, p. 59). In his view, quality can be defined as the cost of non-conformance (Ghobadian & Speller, 1994, p. 59). This interpretation to quality can be relevant to such company as Coca-Cola. Again one should remember that the failure to ensure quality of their products can lead to heavy losses for this organization. They cannot be measured only by the quantity of goods which are damaged. In this case, one has to speak about their reputation which is much more costly, since it is one of the company’s major assets.
Phillip Crosby believes that the key main goal of the organization should be zero defects. Admittedly, this goal may appear to be unrealistic and almost impossible to achieve. However, there are several reasons for setting such high standards. The thing is that by tolerating the very possibility of quality defects, the company can overlook the defects in production or storage of goods. Again, this aspect of Crosby’s model is of great importance to Coca-Cola because this corporation has to minimize the possibility of such errors. There are several elements of Crosby’s model which can be relevant to Coca-Cola’s supply chain.
He suggests 14 cyclic steps which the management should undertake. Among them one can distinguish: 1) the formation of quality improvement teams; 2) identification of possible non-conformance problems; 3) employee education; 4) the design of manufacturing process, and so forth (Ghobadian & Speller, 1994, p. 59). There are several important benefits of Phillip Crosby’s model. He urges the companies to focus not only on existing problems but on hypothetical ones (Ghobadian & Speller, 1994, p. 59). This strategy will be particularly suitable for Coca-Cola. This company interacts with hundreds of suppliers, and they need to predict hypothetical problems which may occur with suppliers, warehouse companies, or transporters.
It should be noted that according to this quality management is a continuous effort requires full commitment of the management. The company should use these tools even when no defects are detected. Therefore, Coca-Cola should regularly monitor the performance of their suppliers. They should not only react to the problems which have already occurred. Although, it seems that Phillip Crosby sets unachievable goals for manufacturing companies; nevertheless, his ideas can surely benefits many organizations, including Coca-Cola.
Ishikawa’s fishbone diagram
The management of Coca-Cola can use another valuable tool for the identification of factors which contribute to the defects, and it is Ishikawa’s cause-and-effect diagram. This practitioner of quality management focuses on such parameters as employee’s skills, the design of the production process, technologies, used by the company, materials, and culture of the company. Ishikawa attaches great importance to quality circles, employee training, and collection of historical data as methods of analyzing and solving quality problems (Ghobadian & Speller, 1994, p. 65). Ishikawa offers a very valuable method of identifying the factors that contribute to quality defects. His fishbone diagram can be applied to Coca-Cola’s global supply chain. It can be done in the following way:
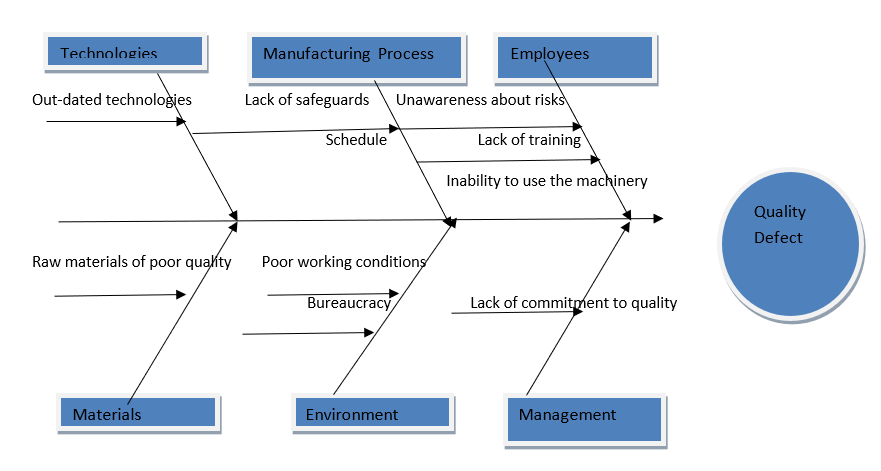
With the help of this diagram we have illustrated various factors that can lead to non-conformance with quality standards. This tool is particularly useful when the management has to identify underlying causes of defects. Yet, this tool is intended mostly for after-event inspections. It cannot help the management predict hypothetical problems and prevent them. Moreover, Ishikawa’s diagram focuses on a set of specific criteria such as technologies, materials, environment, or personnel. However, it may overlook some other factors which may also lead to quality problems.
This is the limitation of this analytical tool. The fishbone diagram presented in this paper illustrates only the most common causes of product non-conformance. This diagram must be supplemented by some other tools, for example: 1) scatter diagrams which describe the relations between different causes and factors, 2) process flowcharts that explain each phase of the production, and 3) Pareto analysis (Ghobadian & Speller, 1994, p. 66). Combined use of these methods can ensure accuracy and validity of findings.
The main advantage of Ishikawa’s approach is that it helps to visualize the root causes of poor quality. However, the management of Coca-Cola should use this tool when they have gathered relevant data. For example, they need to examine the structure of their suppliers, their organizational culture, the number of quality defects within a specific period of time. Without this data, Ishikawa’s diagram can hardly be efficient. The bottling plants of Coca-Cola may have several inefficiencies. Among hypothetical causes of defects, one can distinguish lack of employee’s skills, extremely tight schedules, and poor understanding or risks related to management. The fish-bone diagram will help to categorize these inefficiencies. This is the main advantage of this technique.
Shingo’s Poka-Yoke
The elimination of quality defects can be achieved through the adoption of poka-yoke mechanisms advocated by Shigeo Shingo. These tools are aimed at reducing the possibility of individual errors; this is why they are often called foolproof or mistake-proof devices (McIntosh et al, 2000, p. 2381). These tools can warn the workers about the quality defects. Moreover, they can tell whether a person has followed specific steps while working on the product (Saffer 2009, p. 138). These methods can be implemented at Coca-Cola bottling plants. For example, the managers of bottling plants can install devices which test the quality of carbon dioxide that fills the bottles of Coca-Cola. If these sensors detect that carbon dioxide has become contaminated for some reasons, they can automatically stop the assembly line and raise the alarm. The main advantage of this approach is that it allows the workers to address the problem as soon as possible. This is one of the ways of preventing contaminated gas, entering Coca-Cola products.
Additionally, the production of Coca-Cola consists of many processes and steps many of which have not been disclosed by the company. However, poka-yoke devices can be employed at various stages of this process. If a certain operation is not performed by the worker, the warning system will immediately inform him/her about this failure. For example, very often the operators of assembly lines forget to properly cork up the bottle, and this leads to degasation. The adoption of poka-yoke methods can eliminate such mistakes, but this approach will require complete integration of assembly line. Moreover, Shingo’s model can be used effectively, only if quality managers are able to track and quantify every phase of the production process. Otherwise, this approach may not yield the expected results. In this case, the work of a bottling plant should be presented as a series of steps which have certain quantitative aspects. Thus, one can say that Shigeo Shingo’s model can be of great assistance to Coca-Cola and many of its subsidiaries, including their bottling plants.
Conclusion
The methods and models described in this paper can be of great use to Coca-Cola. Juran’s trilogy and Crosby’s model describe the general principles of quality management that a company can adopt in order to improve the functioning of their supply chain. Ishikawa method can help them pinpoint the underlying cause of defects and non-conformance cases. In their turn, poka-yoke mechanisms can enable them to prevent specific type of errors which are often committed by workers. By combining these approaches, the management of Coca-Cola can eliminate their quality problems and reduce the costs which are associated with such problems.
Reference List
Ghobadian, A. & Speller, S. (1994). Gurus of quality: a framework for comparison. Total Quality Management, 5 (3), 53-69.
McIntosh, R., Culley, S., Mileham, R., & Owen, G. (2000) A critical evaluation of
Shingo’s SMED’ (Single Minute Exchange of Die) methodology. International Journal of Production Research, 38, (11), p 2377-2395.
Saffer, D. (2009). Designing for interaction: creating innovative applications and devices. New Jersey: New Riders.