Introduction
An effective supply chain is a guarantee for corporations to successfully plan production and operations, as well as to address customers’ needs. The supply chain management includes controlling relationships with suppliers, producers, and customers and ensuring that a supply chain works as an effective network without any delays in exchanging resources and processing (Mangan & Lalwani, 2016).
Ford Motor Company is one of the leading automotive manufacturers in the United States and globally, and currently, it produces vehicles under such brands as Ford and Lincoln. While being a multinational corporation and having facilities in different countries, Ford has a complex supply chain that needs to be analyzed in detail (Ford Motor Company, 2017a). The purpose of this paper is to describe Ford Motor Company’s supply chain, analyze the supply chain costs, modes of transportation, and types of warehousing, and provide recommendations for improving the currently used chain.
Ford Motor Company’s Supply Chain
To discuss Ford’s complex manufacturing and distribution chain, it is important to focus on describing suppliers, facilities, customers, and other supply chain partners. The analysis of these components of a supply chain is important to conclude about its effectiveness (Mangan & Lalwani, 2016). Furthermore, it is also necessary to provide a schematic representation of Ford’s supply chain.
Suppliers
Ford’s supply chain can be characterized as a multitier supplier network where thousands of suppliers provide raw materials and parts of vehicles, as well as services and resources. As a result, lead times are usually long, and to address the effective work of multiple product lines, it is necessary to guarantee the successful supply chain management (Dyrud, 2016). There are 10 tiers of suppliers that provide vehicle components and raw materials.
Currently, Ford Motor Company cooperates with about 1,500 Tier 1 suppliers that produce the most important vehicle parts. These suppliers are located in more than 60 countries, where over 4,000 sites are involved in the production processes (Ford Motor Company, 2017a; Ford Motor Company, 2017b). As a result, all these aspects make the supply chain of this automotive manufacturer extremely complex and dependent on lead times, as well as the quality of information exchange and transportation. Any disruption in this chain can lead to negative consequences for the whole production process.
To cooperate with strategic suppliers, Ford uses the Aligned Business Framework (ABF). This framework is important to address sustainability issues and build strong relationships with Tier 1 suppliers as partners (Ford Motor Company, 2017b). In the context of the ABF, employees of different suppliers participate in training sessions to understand Ford’s code of conduct and guarantee productive cooperation.
The list of ABF suppliers includes Adient, Autoliv, Bosch, Continental, Diamond Electric, Sharp, and Umicore among other 107 companies, where more than 70% are production suppliers and more than 25% are Ford’s non-production suppliers (Ford Motor Company, 2017b). This system of collaborating with suppliers allows Ford to predict and control any disruption in operations and production processes.
Facilities
Ford Motor Company has 62 manufacturing sites, including consolidated joint ventures, and hundreds of distribution centers, warehouses, assembly facilities, and offices that are located in different regions of the world. Thus, 62 manufacturing sites are situated in North America (29 sites), Europe (16 sites), South America (8 sites), Asia Pacific (7 sites), and the Middle East and Africa (2 sites) (Ford Motor Company, 2017a; Ford Motor Company, 2017b).
Among them, Ford owns all those plants, assembly facilities, engine plants, and metal stamping plants that are located in the United States, and those manufacturing plants, engineering centers, and assembly centers that are situated outside the United States. It is important to note that about 50% of the company’s distribution and sales centers are leased when more than 95% of engineering centers are owned by Ford (Ford Motor Company, 2017a; Ford Motor Company, 2017b). Thus, currently, there are nine engineering and research and development centers owned by the company. All these facilities are equipped with monitoring and supply chain management systems to control operations.
Customers
The satisfaction of customers’ needs is a priority for Ford Motor Company, and it is reflected in its mission and vision statements. Annually, thousands of private and corporate customers become interested in Ford’s vehicles. The focus is also on dealers. To guarantee the on-time presentation of vehicles and their on-time delivery to sales centers, managers work to organize the cooperation with dealers as important participants of the company’s supply chain. Annual costs associated with establishing relationships with dealers and customers are about $10,000,000 (Ford Motor Company, 2017a; Ford Motor Company, 2017b). Therefore, the focus on customers is reflected in the company’s strategic plan on the development of an effective supply chain.
Supply Chain Partners
While analyzing Ford’s supply chain, it is important to note that there are more than 10,000 indirect suppliers that cooperate with Ford Motor Company while providing facilities, different types of equipment, various materials, and required services (Ford Motor Company, 2017a). These suppliers can be discussed about Ford Motor Company as supply chain partners. To organize the effective cooperation with these indirect suppliers, supply chain managers develop detailed plans and contracts, in which they describe terms, conditions, deadlines, and risks (Mangan & Lalwani, 2016; Simchi-Levi, Schmidt, & Wei, 2014). These procedures are important to predict any risky situations and delays in operations.
A Schematic Representation of Ford’s Supply Chain
To understand the supply chain flows with the focus on Ford Motor Company’s network, it is necessary to provide a schematic representation of the organization’s supply chain. Key flows that need to be reflected in this scheme are the flow of goods and services, the flow of capital, and the flow of information (Mangan & Lalwani, 2016). Figure 1 represents the directions for all these flows with the focus on Ford’s complex supply chain.
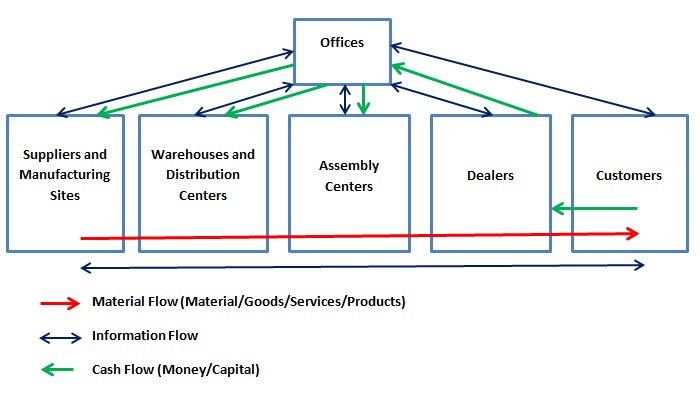
In the 2000s, Ford’s assembly plants controlled logistics operations separately, with the focus on the decentralization strategy. This approach was revised concerning the activities of manufacturing sites and assembly centers located in the United States to reduce supply chain costs associated with using materials and transportation (Ford Motor Company, 2017a; Ford Motor Company, 2017b).
Currently, the organization’s offices control the flow of information with the help of monitoring systems that were implemented at Ford’s sites in the context of the supply chain optimization project. As a result, the flow of information regarding schedules, orders, logistics, and supply chain shipments became not restricted in the network with the focus on the sites located in the United States (Ford Motor Company, 2017a; Simchi-Levi et al., 2015).
The reason for changes is the necessity to provide suppliers, manufacturing sites, and assembly centers with opportunities to modify their operations by set schedules and customers’ expectations. The use of this network for controlling operations and logistics in the company can be discussed as effective as the use of the organization’s network to control the financial management of all U.S. sites.
Ford’s Supply Chain as a Network
To guarantee the effective work of Ford Motor Company’s supply chain as a network, managers pay much attention to organizing the collaboration with suppliers and improving different monitoring systems. Because Ford’s supply chain is wide and complex, it is necessary to analyze the approaches used by managers to control several processes, logistics, and specific aspects of the supply chain performance (Ford Motor Company, 2017a; Mangan & Lalwani, 2016). All these points need to be discussed in detail.
Supply Chain Costs
While focusing on supply chain costs, it is possible to note that the automotive industry is among the leaders in this area. Even though effectively organized supply chains are oriented to reducing costs that are associated with the transportation of components, their storage, and controlling operations, supply chain costs usually represent the large percentage of sales. In the case of Ford Motor Company, the costs related to the supply chain represent more than 75% of sales (Ford Motor Company, 2017a; Ford Motor Company, 2017b). As a result, managers are focused on finding new ways to reduce costs that are associated with transporting and storing vehicle components
It is also important to pay attention to the fact that the number of suppliers and Ford manufacturing sites also contribute to increasing supply chain costs. Therefore, managers are oriented to decreasing expenses while applying the method of vertical integration (Simchi-Levi et al., 2015). Furthermore, managers in this organization also choose to decrease the number of suppliers with the focus on those who can substitute other smaller suppliers (Ford Motor Company, 2017a; Ford Motor Company, 2017b; Simchi-Levi et al., 2014). The reason is that it is important to guarantee that all required components and materials will be delivered in time because the procedures of re-sourcing are expensive.
Transportation
The fact that Ford Motor Company operates in more than 60 countries influences the selection of prioritized modes of transportation that can be used for the supply network. The main focus is on using water transport, motor vehicles, and trains. Airplanes are also used for transporting certain components and parts of vehicles (Ford Motor Company, 2017a). Water transport is associated with delivering materials and components by barge and ships to and from European countries, North America, South America, the Middle East, Asia, and Africa. Ford’s supply chain outside the United States is organized in a way to reduce the number of water routes (Dyrud, 2016; Ford Motor Company, 2017b).
In the company, the most actively used transport includes such motor vehicles as trucks, and they are utilized as primary carriers for Ford’s components (Ford Motor Company, 2017a). As a result, the important parts of the supply chain management are logistics and freight management that is oriented to planning efficient routes and decreasing transportation costs. In this case, the focus is on maximizing services and outcomes associated with the use of carriers.
Warehousing
Ford Motor Company is focused on using warehouses that are the property of third-party providers because of the necessity to utilize large spaces associated with warehousing facilities in more than 60 countries (Ford Motor Company, 2017a). Therefore, warehouses, which are used by the company for storing its products, are usually leased under certain service contracts (Ford Motor Company, 2017a; Ford Motor Company, 2017b). Still, it is also important to note that Ford’s plants and assembly centers that are owned by the company have additional warehousing space to store the limited number of products and components.
Measuring the Supply Chain Performance
To conclude regarding the supply chain performance, it is important to measure certain outcomes with the help of appropriate metrics. In the area of supply chain management, these metrics are numerous (Mangan & Lalwani, 2016). As a result, the organization can focus on using only those metrics that are viewed as effective to indicate changes in performance associated with the supply chain activities.
Cost
This metric is used to determine annual costs associated with purchasing materials, components, and services; purchasing inventories; using facilities; as well as transporting vehicle components and goods. When these costs are analyzed along with annual sales, it is possible to determine the percentage that is associated with the supply chain costs (Mangan & Lalwani, 2016). Thus, referring to the data from Ford’s annual report, it is possible to note that overall annual costs that cover operations and the company’s supply chain are more than $110,000,000 (Ford Motor Company, 2017a). The company’s purpose at this stage is to decrease these costs to reduce the percentage of supply chain costs about the company’s annual sales.
Service levels
Service level metrics are important to be used while establishing criteria for the quality of services provided by suppliers. A certain quality target represented in quantitative terms should be set to control the quality of the provided services (Mangan & Lalwani, 2016). It is also important to pay attention to the fact that the quality of services proposed by Ford’s suppliers is controlled concerning the ABF principles (Ford Motor Company, 2017b).
Furthermore, Ford refers to the following quality standards to monitor the supply chain performance: the annual rate of delays is 15%, the rate of resolved incidents is 95%, and the rate of successful operations is 93% (Ford Motor Company, 2017a; Ford Motor Company, 2017b). These metrics allow for controlling the performance of the supply chain in terms of its efficiency.
Inventory turnover
Ford also refers to the inventory turnover ratio. This ratio represents the relation of the cost of goods to inventories (Mangan & Lalwani, 2016; Simchi-Levi et al., 2015). In 2016, the inventory ratio was 14.2, and this number decreased in comparison to the data for 2015 (Ford Motor Company, 2017a). Managers of the company can make conclusions regarding the effectiveness of the supply chain and the use of inventories concerning these metrics.
Ford Motor Company’s metrics
In addition to those metrics that are usually applied to measuring the performance of a company’s supply chain, Ford’s uses such metrics as the average inventory processing period (26 days in 2016), the average receivable collection period (29 days in 2016), and the operating cycle (55 days in 2016) (Ford Motor Company, 2017a). These metrics are important to demonstrate what changes in operations, logistics, the flow of information, contacts with suppliers, and other associated procedures can lead to such negative outcomes as increases in the number of days related to the inventory processing period and the operating cycle.
Recommendations
Even though Ford Motor Company has succeeded in improving its supply chain management while focusing on the decentralization for those plants located outside the United States and selecting the centralization of operations for those plants located in the United States, there are still challenges in the network that should be addressed to decrease supply chain costs. The problem is that many components that are used for manufacturing vehicles are produced only by a single supplier (Ford Motor Company, 2017a; Ford Motor Company, 2017b).
Therefore, any problems and unpredicted risks and barriers associated with the production and transportation of these components lead to affecting the work of the whole supply chain (Simchi-Levi et al., 2014). From this point, this problem requires its immediate solution to provide Ford Motor Company with opportunities to reduce costs.
Also, one should state that Ford has experience in promoting vertical integration as a supply chain management strategy. Thus, it is important to note that, during a long period, the company used its resources to produce radio systems for vehicles (Dyrud, 2016; Ford Motor Company, 2017a). This approach of vertical integration can be applied to the situation with a single supplier to modify the procedure of re-sourcing orders and signing contracts with partners without affecting lead times (Mangan & Lalwani, 2016; Simchi-Levi et al., 2015). While using this strategy, it will be possible to address the threat of delays and resolve this risky situation that is typical of the company’s supply chain management.
Furthermore, more changes are required in the area of logistics and transportation. It is important to centralize the transportation of materials and components not only with the focus on the United States but also on South America (Ford Motor Company, 2017a; Ford Motor Company, 2017b). As a result, using a single monitoring system, it will be possible to improve distribution operations and decrease lead times (Mangan & Lalwani, 2016). Therefore, it is possible to state that additional training for suppliers can be required to help them adapt to new procedures and processes.
Conclusion
The paper has presented the description of Ford Motor Company’s supply chain with the focus on all its components. Furthermore, the analysis of supply chain managers’ activities has also been presented to determine possible weaknesses in the network and address them concerning the provided recommendations. Thus, it is important to note that Ford’s supply chain can be characterized as extremely complex and multitier because of the large number of suppliers, facilities, dealers, and customers involved in this network. To control this network as a system, Ford needs to regularly improve its supply chain management strategy. In this case, it will be possible to reduce supply chain costs and facilitate operations and manufacturing processes.
References
Dyrud, M. A. (2016). The case of Ford Motor Company. Journal of Engineering Technology, 33(1), 10-15.
Ford Motor Company. (2017a). 2016 annual report. Web.
Ford Motor Company. (2017b). Sustainability report 2016/17: Environmental impact of our suppliers. Web.
Mangan, J., & Lalwani, C. (2016). Global logistics and supply chain management (3rd ed.). London, UK: John Wiley & Sons.
Simchi-Levi, D., Schmidt, W., & Wei, Y. (2014). From superstorms to factory fires: Managing unpredictable supply chain disruptions. Harvard Business Review, 92(1-2), 96-101.
Simchi-Levi, D., Schmidt, W., Wei, Y., Zhang, P. Y., Combs, K., Ge, Y.,… Zhang, D. (2015). Identifying risks and mitigating disruptions in the automotive supply chain. Interfaces, 45(5), 375-390.