Introduction
The history of construction in the United Arab Emirates (UAE) reveals that contractors and design teams put a significant emphasis on the establishment of buildings at the lowest initial capital costs. However, designers, contractors, and policymakers have gradually realised that it is highly unfavourable to determine the project choices based on alternative options such as initial costs alone. Various reports have also shown that the implementation of many projects in the UAE is determined using the initial and current facilities. For this reason, the implementation process takes into account more than 75-percent of the total life cycle costs of the project (Boussabaine & Kirkham 2004). Various studies have also shown that the exclusive consideration of the initial costs fails to make significant economic sense. Following this reasoning, incurring considerably low initial costs can be regarded as a cheap undertaking. However, the effects of such decisions are always felt as the project progresses. Among the most known practices that were appraised as a part of the decision-making process include the Life Cycle Costing (LCC) and Whole Life Cycle Costing (WLCC). Changes in decision-making processes that consider the total life cycle costs of construction projects without saving exclusive initial costs led to the re-emergence of the WLCC approaches in the building industry (Ashworth & Hogg 2007; Boussabaine & Kirkham 2004). The adoption of the life cycle costing has various advantages that encompass the exact measurement of the overall expenditure of the project. Moreover, it is observed that various organisations and governments positively understand the benefits of the LCC. Ashworth and Hogg (2007) reveal that many organisations and governments around the world have adopted similar procurement practices. For instance, the government of the United Kingdom has ensured that the construction organisations in the country make procurement selections that follow the LCC procedure (Office of Government Commerce 2003).
Despite the benefits that the construction organisations receive from adopting the Life Cycle Costing, its level of implementation is still low. A survey conducted by Cole and Sterner (2000) revealed that the limited application of the LCC appeared to be universal. In the UK, it was reported that the low rate of adoption of the LCC was observed by many organisations (Hunter, Hari, & Kelly 2005). However, the quest for sustainable development undoubtedly enhanced its usage (Olubodun et al. 2010). Arja, Sauce, and Souyril (2009) identified various difficulties encountered in the implementation of the LCC and evaluation of the WLC of a building in France. However, Guo, Li, and Skitmore (2010) assert that the Whole Life Cycle Costing has remained a desired element in the construction industry for many years. Nonetheless, its implementation has not been effective.
According to Kishk et al. (2003), many challenges were encountered in the application of the WLC while evaluating the costs of initiating projects in the construction industry. According to Park (2009), the South Korean Construction Industry operates with low application of the WLC. However, a recent change in the construction sector towards the emergence of the contemporary procurement methodologies together with sustainable development has regenerated interest in both the appraising and application of the WLC in the projects. In addition, tenants and owners of several buildings are becoming progressively sensitised to the development of a healthy environment. This situation amplifies the building of efficient and sustainable constructions (Cole & Sterner 2000). It is expected that this undertaking will lead to an extensive application of the LCC and WLC evaluation programs in both developed and developing countries.
Life Cycle Costing Analysis
A Brief History
The history of the Life Cycle Costing evaluation methods started before the 1970s. The concept was initially known as terotechnology. It focused on spending on the initial capital while expecting greater costs to be saved in future operational years with cheaper alternatives. The concept was appealing in its approach. However, it dallied to get wider acceptance in the construction industry. Various reasons were associated with its failure. Two of the major reasons included the ignorance of the LCC’s significance and lack of interest in saving the subsequent building costs amongst the construction organisations (Kotaij, Schuurmans, & Edwards 2003).
In the late 1970s, the concept of the LCC was accepted. As a result, it emerged as a solution to the problems of considering the initial costs while ignoring the operational costs of the project’s lifecycle. It incorporates previous terotechnology and cost-in-use concepts that emerged in the late 1990s when researchers and practitioners realised that the coverage capacity of the LCC was insufficient. It only considered the economic life of the project while ignoring other perspectives. The researchers led to the development of the Whole Life Cycle Costing (WLCC) concept that was introduced in the late1990s. Since then, the importance of the LCC analysis has been rising gradually. This situation has further resulted in the inclusion of both peripheral and indirect asset costs (Langdon 2007).
LCC Evaluation
The primary purpose of the LCC evaluation method is to establish a culture of reputable and sustainable development amongst clients and industry players. The culture aims at executing the most appropriate planning for optimum resource efficiency. Research conducted by Cole and Sterner (2000) showed that contractors created buildings at the lowest costs. They ignored the outlays of wastes such as change of use, future energy, recycling, and building maintenance costs. Figure 1 below shows the data required for carrying out an LCC analysis as presented by Schade (2009).
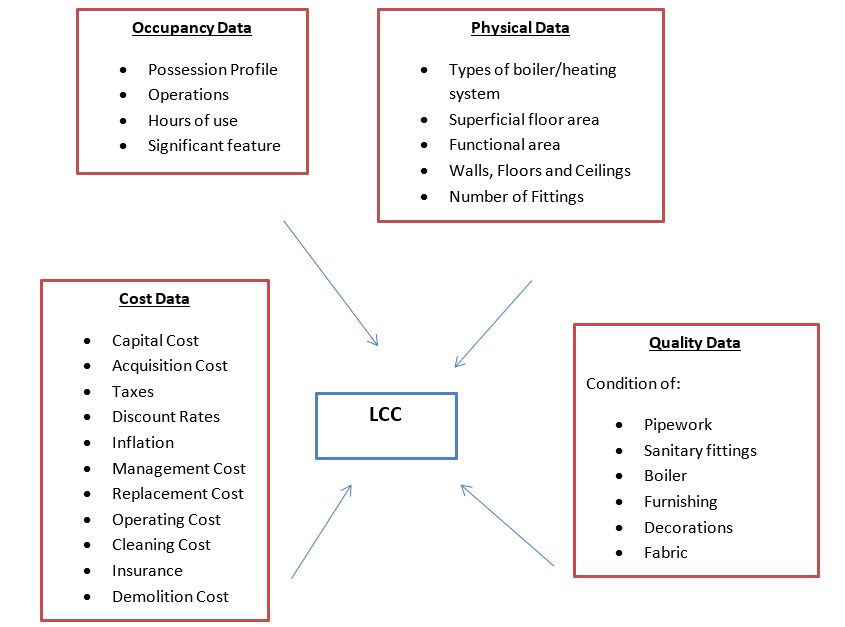
The inputs presented in the above figure show the LCC outcome at varying levels of the project’s lifecycle. Based on the diagram, the initial design phase is predominated by the physical and occupancy data. The LCC evaluation program involved the use of the building aspects such as the functional area and number of fittings among others. The performance and quality inputs are affected by the decisions formulated by the policymakers. The decisions can include the ways through which the inputs are maintained properly and the extent of the demanded hygiene and sanitation (Kishk et al. 2003). The superior information obtained is deemed increasingly independent. As a result, it is perceived to improve the reliability and accountability of the LCC evaluation system (Flanagan & Jewell 2005). The analysis evidence that the detailed design level entails the approximation of the project’s lifecycle about cost data and overall progress (Bakis et al. 2003). However, according to Norris (2001), timing in every project is also important in the LCC evaluation process. Presenting the value of advantages and costs is deemed significant to the success of the overall project. In addition, the specific time horizon is taken into account.
Cost information is considered to be the most significant input to the LCC research. In most cases, the price banks are used to determine the required cost data with a view of improving the evaluation of the building expenses. Kishk et al. (2003) reveal that such data is essential in the alleviation of possible risks that can face the project. The gathering of the information used in the LCC evaluation process is given more weight as compared to the assessment itself. The data collection can be misleading; hence, the decision-makers focus on the reliability and accuracy of obtaining the necessary information. Consequently, the chief objective of the LCC is fulfilled to evaluate the cost-effectiveness of alternative business decisions or investments that mean economic development (Kishk et al. 2003).
Life Cycle Assessment
The successful completion of any project demands continuous assessment from its inception to the production phase. According to Langdon (2007), Life Cycle Assessment (LCA) is a measuring technique that focuses on the development of the project. It provides a framework for monitoring the development of raw materials to finished goods. Further, it guides the usage, reprocessing, and reuse of the products. Besides, it provides appropriate procedures for determining the end of the project’s life. In most of the project cases, the alternative options can have distinct features. This situation can bring about problems especially where single-criterion approaches are applied. The inventories of the life cycle assessment offer the enumerated environmental information (See Figure 2).
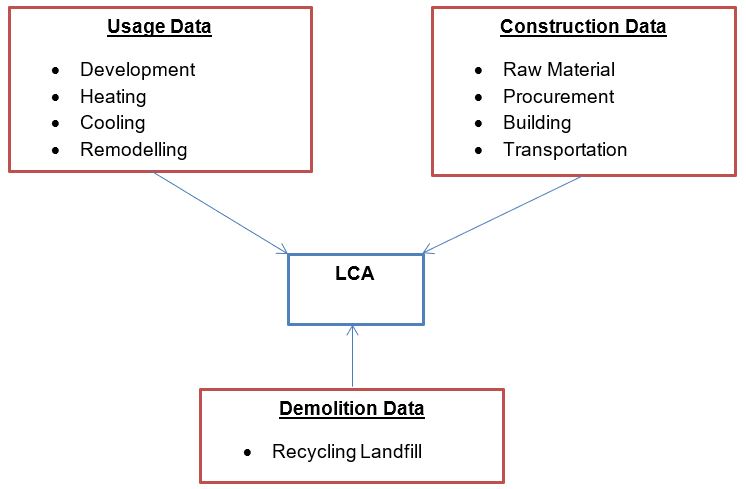
According to Norris (2001), the primary role of the LCA is to evaluate the relative sustainable project performance based on substitutional products that are aimed at arriving at the same results. Sustainability is assessed using holistic measures to promote reliability and accountability. Furthermore, it provides a framework for controlling the resources that are available for the production process to avoid depletion.
Decision Process for Life Cycle Cost (LCC) and Life Cycle Assessment (LCA)
The applications of the LCC and LCA are distinct even though the processes have many similarities. For instance, Norris (2000) reveals that the models are planned characteristically to respond to specific problems. Elsewhere, Ciroth et al. (2008) posit that the LCA works in conjunction with particular economic values. On the other hand, the LCC aligns the LCA’s ideologies to various factors such as cost analysis and product designing and development. Ciroth et al. (2008) reveal that the knowledge about the functioning of the LCC and LCA processes promote the development of eco-friendly constructions. However, the comparison of the Life Cycle Costing and Life Cycle Assessment tools needs to focus on particular characteristics of the client’s decision-making process in the construction industry.
A common phenomenon is that certain factors such as the degree of detailing, model maturity, and information level is being increased as the construction process proceeds from the initial to final phases where the obligatory functionalities are designed to develop technical solutions gradually. Langdon (2007) suggested a stepwise model that identifies conceivable solutions to construction limitations in time. The planned solutions are checked recurrently with a view of authenticating and refining them before the project. In addition, Langdon (2007) reveals that the LCC process is characterised by a crucial aspect that is naturally iterative. Furthermore, it is well-known that the usage and categorisation of the two processes depend on the choices of the involved policymakers.
A study that was conducted by Ochoa, Hendrickson, and Matthews (2002) revealed three different factors that had significant effects on the life cycle of the project. These factors included the building process, usage, and destruction. According to Ochoa, Hendrickson, and Matthews (2002), the usage level constituted over 90-percent of the total life cycle energy. However, many researchers have theorised that there is a need to take into account various characteristics that create the distinction between the LCC and LCA evaluation processes. On average, it is observed that 1% of the project cost is spent on the initial stage while 70% of the life cycle budget is committed (Romm 1994). According to Kishk et al. (2003), various methods are implemented in the evaluation processes to support the policymakers with a view of formulating concrete construction decisions. Nonetheless, the use of the LCC and LCA as assessment approaches to the establishment of buildings is perceived as a multifaceted undertaking. This situation brings about difficulties in arriving at unanimously apposite and good-natured solutions (Elghali et al. 2008). Likewise, the appraisal of the LCC and LCA processes as decision-making tools should provide opportunities for substitute developments, services, plans, and/or structural constituents (Bakis et al. 2003). Another important concept that designers and constructors should consider is the application of the LCC and LCA life cycle inventories. Besides, there is a need to support such systems to improve the handling of events that pose various risks to the project. In this manner, the uncertainties facing the life cycle of the project are greatly reduced thereby increasing the chances of realising the impending construction goals (Bakis et al. 2003).
Implementation of Life Cycle Costing (LCC)
Building manufacturers often aim at increasing profits while lowering costs where applicable. According to ISO (2006), the choices made at each project level have significant effects on its economic aspects. Such decisions pertain to activities such as procurement, setup, maintenance, and disposal (ISO 2006). This situation calls for the assessment of various fiscal aspects to optimise the usage of resources throughout the project’s life cycle. The realisation of this objective requires both the government and contractors to adhere to strict public procurement procedures. The cost time and construction information should also be considered to arrive at a concrete LCC evaluation (Ramzy n.d).
LCC in the UAE Construction Industry
The construction sector in the UAE has recently initiated the framework for economic growth and sustainable development. In general, the level of awareness and usage of the LCC evaluation in the construction industry needs enhancement as this initiative is considered to be in its initial stages. Salama et al. (2010) reveal that the construction industry in the UAE is working to develop itself by adopting various products and processes that are considered both environmentally and economically viable. To achieve this objective, the industry needs to be aware of the advantages of using the LCC technique. Kats (2003) held that using this analysis technique resulted in higher initial capital with lower long-term operational costs. Separate research conducted by Wilen (2008) identified that most quantity surveyors considered the LCC evaluation process when procuring new buildings for PFI projects. However, it is observed that the LCC is not considered for evaluation purposes in certain circumstances that involve exceptional heavy workloads or when operating with limited construction budgets (Ramzy n.d). In such cases, the procurement decisions are based on lower capital costs. The researcher explored various occasional failures of contractors’ quantity and identified due to the ignorance of conducting the LCC cost evaluation processes. This undertaking has poses substantial fiscal risks to the ongoing projects as prices tend to hike. This situation exerts pressure on the initial capital intended for the project.
Difficulties with LCC Implementation in the UAE
The implementation of the life cycle cost evaluation techniques in the UAE has faced various challenges that result from either the industry or its consumers. At the outset, there is a difficulty in considering the three primary data inputs that include the capital, operating, and disposal costs (Ramzy n.d). This situation distorts the usual evaluation process thereby leading to the generation of unreliable construction solutions. Besides, various suppositions about the life span of the properties and the value of the construction components significantly control the length of the contract. Such factors also determine the regularity of substituting each component (Bull 1993). In addition, the prediction of impending aspects such as interest rates, price increases, and discounting procedures directly influence the prevailing values of the assets. This situation poses a high level of insecurity to the construction companies (Bull 1993).
Moreover, the industry players in the UAE’s construction sector tend to handle the capital and running costs distinctively. In this case, the acceptance of the cheapest initial costs while ignoring the future spending trends are inevitable in the country. Due to this ignorance, most of the builders’ hand over the projects to others to either maintain or complete them. Moreover, it is seen that the sector does not have a clear definition of buyers and sellers. In this manner, they fail to know their role in the proper evaluation of both the operational and maintenance costs (Bull 1993). Besides, there is minimal optimisation of costs by the designers and contractors. This challenge arises from the increasingly high cost of applying the LCC evaluation procedures in the design, construction, and maintenance of the assets (McGeorge 1993). Furthermore, there is a challenge in the establishment of the association between the short-term outlays and the life span of the building (Grubb 1998).
Other difficulties faced in the UAE construction industry are linked to the clients. First of all, it is recognised that most clients in the UAE have either little or no understanding of the cost evaluation methods (Bull 1993). This situation serves as an obstacle as the decisions to use the LCC evaluation methods are guided by subjective rather than objective reasoning (Bull 1993). Another trouble arises where the UAE consumers yearn for a variety of aspects that match their needs (Chinyio et al. 1998).
Various challenges also arise from the UAE construction experts. There is a tendency to ignore the impending operational, maintenance, and disposal costs upon the access to cheap capital. Poor prediction of such aspects together also affects the determination of the life cycles, discount rates, and possible price upsurges (Ferry & Flanagan 1991). This situation increases the uncertainties posed to the LCC variables. According to Bull (1993), such indecisions should be alleviated to pave way for improved efficiency and accountability. Most information analysts in the UAE handle intangible data since it significantly influences the formulation of decisions using the LCC evaluation procedures (Flanagan et al. 1989). Last but not least, the construction experts operating in the UAE experience a problem in realising the appropriate and precise information that guides the LCC evaluation process (Griffin 1993).
The UAE Construction Industry Efforts towards Solving Difficulties in the Implementation of the Life Cycle Costing (LCC)
According to Ciroth et al. (2008), many of the abovementioned difficulties will pose further challenges soon for the construction industry in the UAE. However, various researchers, experts, and policymakers are working together with the appropriate authorities to address the shortage and uncertainty of the LCC and the complexity of the exercise. The information on the construction of a building project forms the framework for the LCC evaluation. Therefore, it becomes important to address the basis of the technique through the analysis of the existing construction theories and interventions. Moreover, the government is promoting various efforts to develop the interest of the clients in the consideration of the LCC as a cost evaluation model. In this regard, the consumers are regularly invited to attend various events and seminars where the advantages of implementing the LCC are discussed in detail. Such practices provide them with the appropriate information about the importance of the LCC and WLC evaluation techniques.
In an attempt to overcome the barriers faced by the UAE construction industry in implementing the LCC, several papers and models have been developed. In this regard, a WLC framework and input tool for surveyors was developed by Hunter, Hari, and Kelly (2005). The tool provides simple inputs to the surveyors thereby enabling them to work with the LCC model. Moreover, this tool also ensures that the users are confident with the use of pre-programmed formulae that not only provides the surety of accuracy but also easy applicability. The recognition of the importance of information capturing in the WLC together with the difficulties arising in the process requires a WLCC model decision software application known as the Logbook (Kirham 2005). The application operates simultaneously with the WLCC model to provide the designers with a chronological and sequential record of decisions. Besides, it generates a repository of suitable decision data. However, it is recognised that this software is not compatible with the traditional procurement methods in which the construction team uses different means as compared to the designer team. To address the input shortcoming of the Logbook, El-Haram et al. (2008) proposed a flexible framework for gathering the whole life cycle information for the construction of projects that incorporated design and demolition processes. Up to date, the data structure is perceived as efficient. It is deemed valuable to the project team since they are not directly involved in the traditional protocols observed in the construction projects (Engelhardt et al. 2003).
According to Kishk et al. (2003), the difficulties faced by the UAE construction industry in the implementation of the LCC evaluation model can be alleviated using a variety of vastly fragmented methods. There are no integrated approaches to solving the challenges in the UAE construction industry (Kirkham et al. 1999). Moreover, the sheer comity of many models results in the less practical application of those concepts. This situation fails such models to deal with the uncertainties adequately. In addition, the infrequent provision of quality data also prohibits further enhancement. There is a need to put more emphasis on solving the challenges facing the implementation of the LCC model in the UAE. Last but not least, efforts should be made to develop a framework for the collection the correct and reliable information using the appropriate technological interventions to handle uncertainties (Al-Hajj & Horner 1998).
Conclusion
This specific chapter describes the history and description of the LCC evaluation model as well as the concepts associated with it such as the LCA and WLC. Moreover, it also describes the current shift in the global construction industry from the dominant culture of using the traditional cost evaluation models to whole life cycle estimations. The chapter also states the status of the LCC in the UAE construction industry. It highlights the details of the construction industry of the UAE and the barriers that it faces in implementing the LCC as a cost evaluation model.
References
Al-Hajj, A & Horner, M 1998, ‘Modelling the running cost of buildings’, Construction Management and Economics, vol. 16 no. 4, pp. 459-470.
Arja, M, Sauce, G & Souyril, B 2009, ‘External uncertainty factors and LCC: A case study’, Building Research & Information, vol. 37 no. 3, pp. 325-334.
Ashworth, A & Hogg, K, 2007, Willis’s Practice and Procedure for the Quantity Surveyor, Blackwell Publishing, Oxford.
Bakis, N, Kagiouglou, M, Aouad, G, Amartunga, D, Kishk, M & Al-Hajj, A 2003, An Integrated Environment for Life Cycle Costing in Construction House, Taylor and Francis, New York, NY.
Boussabaine, H & Kirkham, R, 2004, Whole Life-cycle Costing Risk and Risk Responses, Blackwell Publishing Ltd, Oxford.
Bull, J 1993, Life cycle costing for construction, E & FN Spon, London.
Ciroth, A, Hunkeler, D, Huppes, G, Lichtenvort, K, Rebitzer, G, Rudenauer, I & Steen, B 2008, Environmental Life Cycle Costing, SETAC Press, Pensacola, FL.
Cole, R & Sterner, E 2000, ‘Reconciling theory and practice of life cycle costing’, Building Research and Information, vol. 28 no. 5, pp. 368-75.
Elghali, L, Clift, R, Begg, K & McLaren, S 2008, ‘Decision support methodology for complex contexts’, Engineering Sustainability, vol. 161 no. 1, pp. 7-22
Engelhardt, M, Savic, D, Skipworth, P, Cashman, A, Saul, A, & Walters, G 2003, ‘Whole life costing; Application to water distribution network source’, Water Science and Technology: Water Supply, vol. 3 no. 2, pp. 87-93.
Flanagan, R & Jewell, C 2005, Whole Life Appraisal for construction, Blackwell Publishing, Oxford.
Flanagan, R, Kendell, A, Nomian, G & Robinson, G 1987, ‘Life cycle costing and risk management’, Construction Management and Economics, vol. 5 no. 4, pp. 53-71.
Guo, H, Li, H & Skitmore, M 2010, ‘Life-Cycle Management of Construction Projects Based on Virtual Prototyping Technology’, Journal of Management in Engineering, vol. 26 no. 1, pp. 41-48.
Hunter, K, Hari, S & Kelly, J 2005, ‘A whole life costing input tool for surveyors in UK local government’, Structural Survey, vol. 23 no. 5, pp. 346-358.
Kirkham, R 2005, ‘Re-engineering the whole life cycle costing process’, Construction Management and Economics, vol. 23 no. 1 pp. 9-14.
Kishk, M, Al-Hajj, A, Pollock, R, Aouad, G, Bakis, N & Sun, M 2003, Whole Life Costing in Construction – A State-of-the-Art Review, RICS Foundation, London.
Kotaij, S, Schuurmans, A & Edwards, S 2003, Life cycle assessment in building and Construction, Society of Environmental Toxicology and Chemistry, Denver.
Langdon, D 2007, Life cycle costing (LCC) as a contribution to sustainable construction: a common methodology, Davis Langdon Management Consulting, London, UK.
Norris, G 2001, ‘Integrating Life Cycle Cost Analysis and LCA’, The International Journal of Life Cycle Assessment, vol. 6 no. 2, pp. 118-120.
Ochoa, L, Hendrickson, C & Matthews, H 2002, ‘Economic Input-output Life-cycle Assessment of U.S. Residential Buildings’, Journal of Infrastructure System, vol. 8 no. 4, pp. 132-138.
Office of Government Commerce 2003, Whole-Life Costing and Cost Management, Procurement Guide Number 07: Achieving Excellence in Construction, Office of Government Commerce, London.
Olubodun, F, Kangwa, J, Oladapo, A & Thompson, J 2010, ‘An appraisal of the level of application of life cycle costing within the construction industry in the UK’, Structural Survey, vol. 28 no. 4, pp. 254-265.
Park, S 2009, ‘Whole Life Performance Assessment: Critical Success Factors’, Journal of Construction Engineering and Management, vol. 135 no. 11, pp. 1146-1161.
Ramzy, E n.d, A study in the use of life cycle costing in 5D BIM applications in the UAE Construction Industry, Routledge, London.
Romm, J 1994, Lean and Clean Management: How to Boost Profits and Productivity by Reducing Pollution, Kodansha International, New York, NY.
Schade, J 2009, Energy simulation and life cycle costs: estimation of a building’s performance in the early design phase, Luleå Tekniska Universitet, Licentiatuppsats Luleå, Sweden.