Organization’s Overview
The Lufthansa Group is one of the largest global aviation companies, and it is one of the leading aviation companies in the European market. The company has 105,290 employees globally, and in 2021 it generated revenue amounting to 16,811 million euros (Lufthansa Group, n.d.). The Lufthansa Group is segmented into various units, for instance, Network Airlines, Eurowings, and Aviation Services. The aviation industry is a very dynamic sector, and it is known for its massive workforce and its contribution to the global economy. The sector is exposed to various risks and challenges, from natural disasters like the global pandemic to economic and human-induced challenges. As one of the key global players in the aviation sector, Lufthansa airline is not immune to these challenges in its operations. Various operational management frameworks can be utilized to analyze business operation challenges. For the case of Lufthansa Airlines, the 4vs operation management framework, operation management performance objective, and the seven waste of lean management are vital in understanding the company’s operation management challenges.
Operations Management Challenges
Four Vs. Operation Management Framework
The 4vs operation management framework is appropriate in analyzing the operations of the Lufthansa airline. In terms of volume, the company still experiences challenges with crew shortages due to illness and strikes. The crew shortages have led to the cancellation of various flights by the company. From January to February 2021, the company canceled about 33,000 flights due to the global pandemic, which was about 10 percent (Scott, 2020). In early 2022, the company was faced with higher illness in the cockpit crew than usual, thus halting its operations.
The company has also diversified its operations into various segments to increase profitability. The Lufthansa Group is segmented into various units, for instance, Network Airlines, Eurowings, and Aviation services. The network airline is further segmented into the German, Swiss, Austrian, and Brussels airlines. The Lufthansa German airlines are subdivided into Lufthansa city line air Dolomiti and Eurowings Discover. In 2021, the group launched another segment known as the new holiday airline, which mainly focuses on tourism (Redpath, O’Connell & Warnock-Smith, 2017). The Eurowings segment is specifically designed to focus on short-haul traffic in the European market.
The company increases the operational cost by diversifying since each segment is exposed to different crises. In 2020, the company experienced an operating loss of 5.5 billion euros, while in 2021, the company reported an operating loss of 2.3 billion euros, with its shares trading lowest at 1.4% in the Frankfurt trade (Cachinho, 2021). Figure 1 shows a decline in the Lufthansa Group’s share. There has been a variation in the demand of company services over time. This variation has resulted from external factors such as COVID-19 challenges and political instabilities.
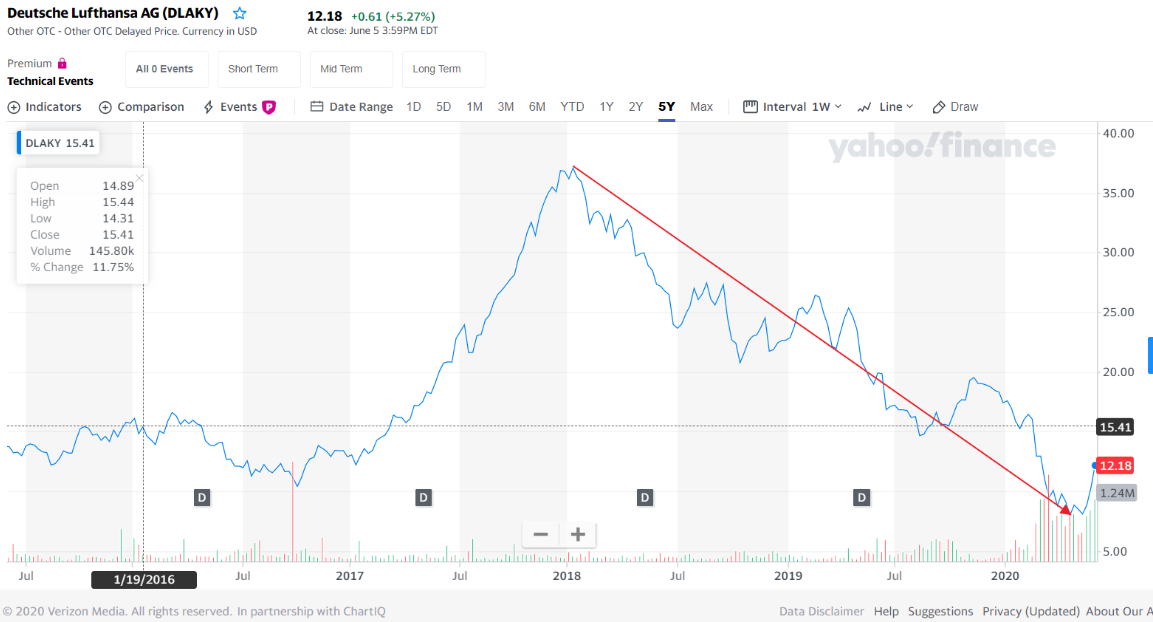
The demand for the airline felt in 2020 at the onset of the coronavirus pandemic. This resulted in a drop in the Lufthansa group revenue, which fell by 52 percent from 17,4 billion euros to 8.3 billion euros (Lufthansa Group, 2020). This drop resulted from the decrease in the operation of the airlines. In the first half of 2020, Lufthansa airline experienced a reduced number of passengers by two-thirds compared to the first six months of 2019 in 2020; between January to June, the company carried 23.5 million people, which was 61 percent lower than in 2019 (Lufthansa Group, 2020). Figure 2 shows the operational figures of Lufthansa Airlines from 2017 to 2021.
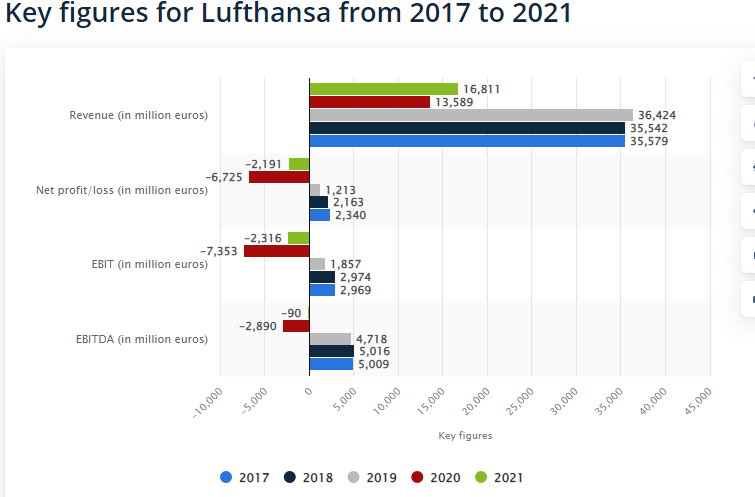
Seven Waste of Lean Management Framework
The seven waste of lean management or lean manufacturing is a vital tool used in analyzing the company’s operations. This framework focuses on the elimination of wastes within the company’s operations. Lufthansa may experience time wastages as a result of delayed landing due to weather and traffic in the airport, waiting for passengers to take their seats, waiting for clearance to take off, and the clients’ boarding time as they wait for the door to be opened are other forms of wastages experienced by the company. Waiting also can affect the environment due to emissions from the airline, and possible damage to the products is also a possible risk due to waiting.
Transporting is also a key aspect of the lean management framework that can be used to analyze air transport. Transportation waste can be considered as any form of excessive transportation which does not add value to the product. For the aviation sector, it is vital to minimize this form of waste. One of the methods used by airlines, including Lufthansa, to minimize waste in transportation is through the joining of flights. This has been achieved by conducting long-haul flights only in big airports. This has assisted the company in cutting costs, and bringing airports closer to one another.
Still, it is a challenge that has increased the waiting time as it has to wait for the arrival of clients from different parts with different departure times. Another possible challenge to Lufthansa Airlines is over-processing. The law requires airlines to employ highly qualified personnel in the sector (Martin & Garner). Airlines such as Lufthansa must process their employees based on set guidelines to ensure they meet the standards. From the airline’s point of view, the over-processing, which demands a lot of licensing from pilots and flight attendants, has been a pain point that has resulted in a shortage of crew in the sector. For instance, Lufthansa had to cancel some flights due to a lack of pilots due to COVID, which greatly affected the airline’s operations.
Operation Performance Objective Framework
This framework is associated with speed, quality, dependability, flexibility, and cost of the operations. Regarding the operations of Lufthansa, this operational performance objective must be considered and can be used to analyze the company’s performance. In terms of punctuality, Lufthansa Airlines experienced difficulty coping in 2021. In September, the operation of the company airline experienced a slight improvement in terms of punctuality. Almost every fifth flight of the Lufthansa airline arrived late at the destination.
The improvement was seen in the airline in September compared to August, but this was still below the normal airline annual average and far below the European airlines in terms of punctuality. Despite the delay in the exemplary performance in schedule reliability, the company achieved a strong reliability score of 99.7 percent, perfectly in line with its annual schedule reliability average (Schmidt, 2020). The company has also shown how flexible it is in terms of operations. During the pandemic, the company changed its operations to accommodate its clients. It allowed the clients to plan well for their trips by allowing them clients to rebook their tickets in all the flight segments.
Supply Chain Analysis
A supply chain is an avital component of the aviation sector since it helps save costs for operating the business. The airline’s success in the industry relies on how well the company adopts the supply chain. Lufthansa airline’s supply chain works through the purchasing department through its internal requesting department to ensure that the company purchases products at affordable prices with the latest technology. The department requests the supplier to send their proposal where the department evaluates the clients based on their innovation capacity, the supplier cost structure, the supplier compliance to regulations, and a comparison of the cost of the competitors for Lufthansa to enjoy an optimal cost-benefit ratio.
After the company has successfully evaluated the suppliers to determine which meets all the said criteria, the company then places the order. The order is only placed through an order form. The company order forms consist of a timeline of the service. The quantity and the order from the company are designed to give a specific code, for instance, 90, for easier referencing. However, before finalizing any order at the company, the order must go through a clearance process that verifies that there are available funds to facilitate the order and the order is correctly drafted. The process is also key in identifying if the orders have been signed by the correct cost center and G/L account to facilitate the easier processing of the invoice. The suppliers then receive the goods based on the order generated by the company buy order system.
The goods are verified and checked based on their conditions and checked if their order number matches the order and in terms of the structure of the order and position. The invoice is generated automatically and cleared for payment under the condition that the purchasing department confirmation accompanies the order in the accompanying accounting system. The supplier further needs the signature of the recipient of the product or services to sign against the order delivery note, which matches the one in the system structurally and with the same order number. The supplier should hand the customer copy to the receiving company within the group to log in to the accounting system once the goods are received for the client to send the invoice and receive payment.
The company controls most of the supply chain operation, from evaluating the supplier to receiving the goods. The only part in which the company lacks control is the setting of the regulation, which governs the production of products it uses. It is recommended that the company reduce the bureaucracy within its supply chain to ensure that the suppliers are paid on time. The requirement by the company for the suppliers to look for the receiving organization within the group to countersign the delivery note should also be an automated process. It should be achieved by the recipient just logging in after verifying the goods to prove that they received the right product. Figure 3 summarizes Lufthansa Group’s supply chain.
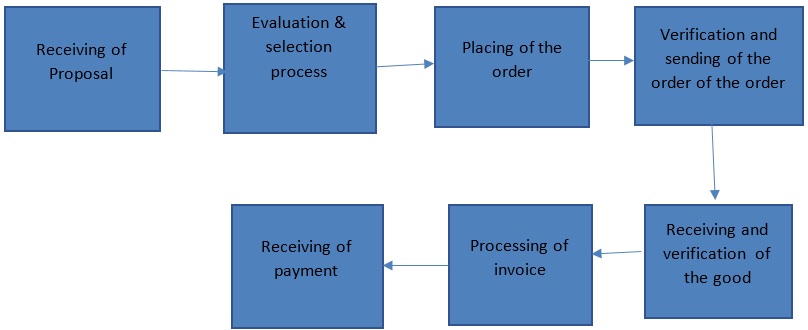
Operational Risk Analysis
Table 1. Risk assessment.
Summary
The Lufthansa Group is one of the largest global aviation companies, and it is one of the leading aviation companies in the European market. Despite the size, the company still experiences challenges with crew shortages due to illness and strikes. The crew shortages have led to the company’s cancellation of various flights, leading to losses. The company has a robust supply chain that facilitates its operations. A supply chain is a vital component of the aviation sector since it helps save operating costs. The airline’s success in the industry relies on how well the company adopts the supply chain. Lufthansa Airlines have digitized its supply chain, which works through the purchasing department through its internal requesting department to ensure that the company purchases products at affordable prices with the latest technology.
Improvement Recommendations
- The airline should train its pilots to avoid future cancellations of the flights due to employees’ sickness and strikes. The company should embark on training pilots on a small scale to test the project’s viability and determine its costs and benefits on the company revenue and provide better working conditions for its employees.
- The company can boost its reliability score further by reducing the unnecessary delays caused by humans. The company can adopt the use of technology in various segments which are dependent on humans but can be computerized to ensure reliability due to high-level accuracy, thus limiting delays, for instance, ticket booking.
- To reduce time wastages due to the over-processing of employees, the airline can act by ensuring that it provides its recruits with relevant information about their roles and duties and relevant documents they are required to have before joining the airline. In this way, the company will be able to minimize risks associated with non-compliance and also save time as they will not be required to retrain new employees to fill the gap that will be left upon determination of the issue.
- The company can also reduce the over-processing of the suppliers by automating the entire supply chain. The current system still requires the supplier to physically present the order paper to the company for it to be filed and signed before uploading it back into the system for the payment to be made.
References
Cachinho, C. F. F. (2021). What influences management to disregard the quality of disclosure? Lufthansa case [Unpublished doctoral dissertation]. Instituto Superior de Contabilidade e Administração do Porto.
Lufthansa – operational figures 2021 | Statista. (2022). Statista.
Lufthansa Group. (n.d.). Company.
Lufthansa Group (2020). Consequences of Corona pandemic have a considerable impact on Lufthansa result.
Martin, S., & Garner, W. (2017). The application of lean thinking: An example of ground handling operations at an international airport. In A. H. Obaide (Ed.), Proceedings of the 3rd international aviation management conference (p. 117-125). Emirates Aviation University.
Redpath, N., O’Connell, J. F., & Warnock-Smith, D. (2017). The strategic impact of airline group diversification: The cases of Emirates and Lufthansa. Journal of Air Transport Management, 64, 121-138.
Schmidt, K. C. (2020). Strategic alliances as a form of coopetition and its impact on the performance of airlines: A case study analysis of Lufthansa, Finnair, and Alitalia.
Scott, B. I. (2020). National aviation law responses to COVID-19. Air and Space Law, 45, 195-272.