Literature review
Six sigma
In the beginning, six sigma meant having no more than 3.4 defects per million opportunities in any process, product, or service. However, it is much broader, referring to a program designed to reduce the occurrence of defects to achieve lower costs and improve customer satisfaction in manufacturing corporations. It uses certain tools and techniques to selected projects to achieve strategic business results. In the business world, six-sigma programs have become a key way to improve quality, save time, and cut costs. Six Sigma programs can be used to improve designs in production, service, inventory management (Riebling et al 2005, pp. 23)
There are management and technical components of six-sigma programs. The management components involve providing strong leadership, defining performance metrics, selecting projects likely to achieve a business result, and selecting and training appropriate people. The technical component involves improving process performance, reducing variation, utilizing statistical methods, and designing a structured improvement strategy, which involves definition, measurement, analysis, improvement, and control (Pande et al 2001, pp. 23).
For six-sigma to succeed in any organization, buy-in at the top is essential. Top management must formulate and communicate the company‘s overall objectives and lead the program for a successful deployment. Some of the main principles of Six Sigma come from Total Quality Management, such as the entire organization must support the quality effort and there should be a strong education effort. However, within TQM it is difficult to associate financial benefits to the quality efforts realized and there is no common metric to measure the level of quality finally obtained (Black et al, p. 262).
Once management has decided to invest in a Six Sigma project, the key factor for success is people (Fleming et al, 2005 p. 110). The first requirement is a project leader who is familiar with the Lean and Six Sigma concepts and who is accountable for obtaining improvement; the second is the involvement of laboratory staff in the project through communication, the introduction of core laboratory theories, and organized training sessions (Estioko, 2006 p. 5). Many articles have reported encouraging results for Six Sigma deployment in clinical laboratories (Daley, 2006 p. 5 and Riebling, 2005 p. 23).
Six sigma and quality
Quality management includes integration, consistency, efficiency, and a continuous drive for improvement. Within the organization, resistance to change needs replacement by a culture driven by quality considerations and that is again a difficult exercise. However, responding to these challenges has the potential to yield high rewards through increased reliability of products, safety and efficiency, and consistency (Riebling et al 2005, pp. 23).
Historically, the development of quality concepts has emanated from industrial settings in developed countries with the Japanese and the Western countries leading the way. A very large number of systems to build quality into every aspect of operations have evolved largely dependant on the particular situation a company may find itself in and the statutory requirements faced (Pande et al 2001, pp. 23).
Steps
When implementing six sigma some steps are followed to define a solution.
- Step 1: Define the problem and establish an improvement goal- Give problem definition careful consideration.
- Step 2: Develop performances measured and collect data-The solution must be based on facts, possible tools include a check sheet, scatter diagram histogram, run chart, and control chart.
- Step 3: Analyze the problem-Possible tools include Pareto chart, cause-and-effect diagram
- Step 4: Generate potential solutions- Methods include brainstorming, interviewing, and surveying
- Step 5: Choose a solution-Identify the criteria for choosing a solution (Refer to the goal established in step 1) apply criteria to potential solutions and select the best one.
- Step 6: Implement the solution-Keep everyone informed
- Step 7: Monitor the solution to see if it accomplishes the goal- If not modify the solution, or return to step 1. possible tools include a control chart and run chart.
By applying the Six Sigma process, companies can formulate, integrate and execute new business strategies as well as open for new ones. Since it is obvious that customer requirements and demands for the products are ever-increasing and constantly changing, these things can be dealt with efficiently through the Six Sigma process. Every company envisions that their company could cover vast horizons and eventually be known globally, the globalization efforts of the company can be accelerated. Innovation will also be facilitated. Mergers and acquisitions will also be facilitated. Since the trend now is that businesses must have a corresponding e-business, effective implementation of e-business will be ensured including strategies and infrastructure. Six Sigma can also drive revenue growth and systemic and sustainable culture change. The corporate learning cycle will be enhanced and condensed thereby saving time (Smith et al., 2002, p. 45).
Six Sigma brought major impacts on the culture, operation, and profitability of some of the largest companies including Asea Brown Bavari (ABB), AlliedSignal, GE, Lockheed-Martin, Motorola, Polaroid, and Texas Instruments (1999). Three characteristics differentiate Six Sigma from the past quality improvement programs that were used by companies. (1) Six Sigma is customer-focused. In every Six Sigma company, the customers serve as the driving force for innovation and improvement. Whatever customer demands on that particular period, the company has to provide the customer with utmost satisfaction. (2). Major returns on investment are very much possible with Six Sigma. Evidence was given by GE from their Six Sigma program wherein return on investment almost tripled the investment cost in just two years. In 1996, GE invested $200 million, and its returns $150 million. In 1997, the investment cost was $400 million and its returns $600 million. In 1998, the investment cost was $400 million and it brought the company more than $1 billion. Based on the report of GE’s CEO Jack Welch, Six Sigma saved the company more than $2 billion. (3) The third difference is that Six Sigma changes how management operates. It introduced new ways of thinking, planning and executing thus making the business work smarter (Pande et al., 2001, p.25).
Harry Schroeder (2000) once said, “Six Sigma is about making money.” This is indeed true with the firms who adopted the Six Sigma wherein their revenue really boost. GE for example reported in 1999 that Six Sigma increased their revenue by $2 billion. Allied Signal was near bankrupt when their CEO Larry Bossidy decided to adopt the Six Sigma and saved the company from bankruptcy. Similar results were reported by Polaroid, Asea Brown Bovari (ABB), and Ford Motor Com which are also early adopters of the process. Based on careful observation by Waxer on the annual revenue from 1986 to 2000, savings attributed from Six Sigma ranged from 1.2% to 4.5 % of annual revenue for a number of Fortune 500. Based on the report by Bolten (2003), the Idaho National Engineering and Environmental Laboratory achieved over $40 million in 18 months of employing the Six Sigma. The impressive results clearly show the differences between total quality management which was introduced by W. Edwards Deming in 1980 and Six Sigma. According to Repenning and Sterman (2001), TQM has frequently failed its expectations (Box, 2006, p. 20).
The Six Sigma initiative lies firmly on statistics although it originated mainly from engineers and managers. Six Sigma companies use statistical and related methods extensively. Somehow results showed that projects focused on statistics yield significant financial results. Products and services are categorized based on the six standard deviations between the mean and the specification limit. In this process then, all items will fall in any of the six specifications. Statisticians noticed that having six standard deviation as specification limits, 3.4 defects per million will not result. The number would be arrived by assuming that the process drifts over the long term by 1.5 standard deviations (Hahn et al., 1999p. 208). If Six Sigma and Three-Sigma would be compared by plotting on a graph, both processes appear to cover all specifications of the product. Figure 1 shows a graph comparing the Six Sigma and the Three-Sigma (Riebling et al 2005, pp. 23)
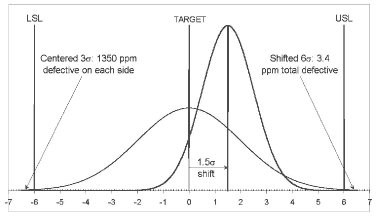
In the graph, LSL is the lower specification limit and on the right end is the USL or the upper specification limit. The middle line represents the target, where T equal (USL+LSL)/2 (Ramberg, 2000, p. 45). In Six Sigma measurement is by defects per million operations (DPMO). Calculation of DPMO is by multiplying an error rate by million. The product would be divided by the number of ways an error can occur. A normal probability table is used to convert DPMO values to sigma. Reduction of DPMO and increasing sigma is the main target of the Six Sigma projects (Box, 2006, p. 25).
Many professional roles in Six Sigma are designated with martial arts convention. The key roles are vital for the implementation of the Six Sigma. To maximize performance, they empower their employees and everyone who works for the company to have the freedom and resource which they might need in exploring new ideas. Champions are picked by the Executive Leadership from the upper management and are tasked to implement Six Sigma across the organization in an integrated manner. They act as mentor to Black Belts. Their most fundamental role is to serve as buffers. They would mediate between the top management and the Black Belts so that head-to-head confrontation will be avoided. Characteristically, champions are proficient in business and operations management, project selection, pace mediation and results implementation (Carnell, 2008). In GE, this rank is referred to as Quality Leader (Institute of Industrial Engineers Ireland, 2008). The Master Black Belts act as coaches in the Six Sigma. They spend their time training, mentoring and consulting the Black Belts and the Green Belts. The Black Belts are the project leaders. They are committed to the use of Six Sigma methods in their projects to make sure that full customer satisfaction will be achieved. They are skilled in statistical methods and interpersonal communication. They undergo intensive training and real-world experience on problem solving strategy and methodology (Carnell et al., 2008) hence they are individuals who are self-assured and knowledgeable. They are also disciplined, purposeful, decisive and highly focused. They are the core structure in the operation system. The Green Belts are employees who are responsible for fewer projects. They require less training than the Black Belts (Chadwick, 2008). The Yellow Belts are employees who undergone the Six Sigma technique training as part of the corporate-wide introduction of the method. Unlike the Green Belts they were not able to complete any project. They may not take part of any quality improvement activities as it is not part of their designation (Institute of Industrial Engineers Ireland, 2008).
As stated, Champions must be proficient in four areas. First, they should know the business and operations interface. They must know the process but should never intrude in the process. They just have to make sure that operational level projects will always be kept aligned with the business objectives. They are allowed to review projects to assure that the project is progressing at the required pace and according to plan. By so doing, they can identify areas which need improvement. Second, Champions must be proficient in Six Sigma project selection. Instead of viewing it as a career limiting opportunity, they must view it as an opportunity to improve the process. Project selection will become less of a treat if alignment is practiced in an organization. Third, Champions must be proficient in pace mediation. The deployment plan is usually generated by the Six Sigma provider or the internal sponsor. Choosing an internal sponsor has an associated. Most instances plans are difficulty to modify due resistance from within. When the plan is constructed, it should be complete. For any plan to be successful it should be able to satisfy the customer needs and this is achieved through it goals and attainable targets thus creating competitive advantage. Metric must also be present. There are adjustments to the program every time there is change to match the required metric. The fourth is that Champions must be proficient in results implementation. The project is analyzed in terms of benefits after it is completed. The Champion is accountable for this number. For example, if the project was expected to bring $50,000 in 12 months but at the end of the project, there was only $25,000 because may the Champions to six months to get involved, The lack of involvement of the Champion would be reflected in the metric. The metric would also reflect inaccuracy. For example, if the plan was executed accordingly but the financial projection was inaccurate, it must be indicated in the metric (Carnell et al., 2008).
Six Sigma is not only about fostering quality program, it also changes culture within an organization. Culture change within a company requires strong leadership and focus on project implementation. The management should deploy sigma projects to all levels of management. Competencies in statistical data analysis should be developed by individual leaders. They must also be able to cascade their competencies to other leaders. For sigma projects to succeed leaders should use existing communication channels to ensure employees are involved in these projects. This will help reduce instances of resistance from employees. For the company’s top leaders to be successful in implementing Six Sigma in all levels in the organization, they must understand seven steps of deploying Six Sigma. (1) For Six Sigma initiatives to spread there should be support from committed team leaders. (2) Strategy planning and deployment must be integrated with strategic Six Sigma thinking and best practices. (3) Wherever the company operates, it needs to establish a close connection with the customers and the whole marketplace. (4) It must ensured that leaders do not view the company as mere isolated functions rather a family of closely related business processes which is supporting the business’ value. (5) Quantifiable measures must be developed. Other than that, leaders must demand from their employees their expectations and the aspired tangible results. (6) To compliment the employees’ performance, incentive and rewards system must be developed by the company. This would also entice the employees to perform better. (7) Lastly, top leaders must commit to all of the six strategies (Smith et al., 2002, p. 49).
Ability Analysis
Capability analysis is the determination of whether the variability inherent in the output of a process falls within the acceptable range of variability allowed by the design specification for the process output. If it within the specifications, the process is said to be capable. if it is not, the manager must decide how to correct the situation.
The process of assessing the capability could be in control and still generate unacceptable output. Thus, one cannot automatically assume that a process that is in control will provide desired output instead he must specifically check whether process is capable of meeting specifications and not simply set up a control chart to monitor it. A process should be both in control and within specification before production begins-essence (Riebling et al 2005, pp. 23).
Advantages and Disadvantages of Six-Sigma
There are many advantages of six-sigma, among them is listed below (Bertels, 2003 p.45-49):
- Six sigma involving all operations and management units in the organization and led from the top;
- The customer as king with every strategy ,process and action directly related to satisfying customer’s needs;
- A greater emphasis on rational information collection and analysis using modern technology where appropriate;
- An emphasis on a different approach to looking at the cost of poor quality by examining all processes in the organization which add to costs;
- A greater involvement of people, recognizing that they are a great untapped resource in most companies.
- Teamwork as crucially important, involving multi-discipline and multi-level working to solve problems and to meet customers’ needs ;and
- The requirements for creative thinking and the ability to think beyond the immediate job or work environment.
For dynamic companies quality is becoming a complete misnomer as it moves organizations into the arena of business excellence. To achieve this transition, the challenge for the future is to harness latest developments and thinking in this field (Estioko, 2005 p.E5).
- Six sigma should represent two things in today’s business, customer satisfaction and continual improvement. Customers demand satisfaction and expect more. It is no longer sufficient to merely satisfy customers; they need to be delighted, both internally and externally.
- Today’s competitive business performance requires the setting of clear missions, objectives and measurement to deliver these levels of customer satisfaction. A balanced company-wide approach is needed. The way forward is to achieve business performance through the linkage of critical company issues right through to day-to day activity and reporting.
- Teamwork is replacing the organizational hierarchy but teams need to be able to perform well with good team leadership and quality process to work with to achieve their missions.
- Quality registrations based on compliance to standards like ISO 9000 have played their part but this arena is moving fast. Leading organizations will need to adapt from compliance to performance based quality management systems as benchmarking takes over.
- Complicate this with new environmental initiatives such as ISO 14000 and numerous other standards, then flexible, dynamic management system are need more than ever.
Disadvantages of six sigma
- Six sigma advocates a routine that consists of checking technical activities, measuring the quality of the product and keeping a control over it which may expensive and hard to maintain(Hahn, et al, 1999, p. 208).
- At times control procedure used may have an adverse effect in future production and hence profitability. The basic tools for a quality control consist of Inspection, Control Charts, and Ishikawa chart, Histogram, Stratification, Statistical Sampling, Pareto Chart and Flowcharting. Inspection helps to determine whether the results are in accordance with the requirements (Hahn, et al, 1999, p. 208).
- The whole management should be integrated well otherwise six sigma will fail to be successful. This means that some companies can’t undertake a fruitful research if they find that their hard work has got no implementation from the top management (Hahn, et al, 1999, p. 208).
- In the present era of high technique and modernization, the six sigma has become more and more dynamic. It involves an integrated picture at every point of time requiring quick data processing and analysis for adjusting the fluctuations of demand and abrupt change in circumstances. Thus requires dynamic management if not it will fail (Hahn, et al, 1999, p. 208).
Conclusion
Keeping customers is very important in every company. They must be able to retain their customers so they would be able to remain in the industry and flourish. One of the best way, to get more customers and keeping old customers is to provide them with the products which are of best quality. The main objective of the Six Sigma is to reduce near-perfect products and reduce wastes. In this way, revenues and savings would be high. The Six Sigma is also versatile as it can be applied in almost all industries. It just needs to be adjusted to fit the company’s goals. The effectiveness of Six Sigma has been proven by many companies which adopted the process (Bertels, Thomas, 2003, pp. 48)
References list
Bertels, T. (2003). Rath & Strong’s Six Sigma Leadership Handbook. Hoboken, NJ: John Wiley & Sons. pp 45-49
Black K and Revere L. (2006). Six Sigma strategy arises from the ashes of TQM with a twist. International J Health Care Quality Assurance Inc Leadership Health Services; 19:259–66.
Box, Thomas M. (2006). Six Sigma Quality: Experiential Learning. SAM Advanced Management Journal, 71(1): 20.
Carnell, M. and Shank, S. (2008). The Champion’s Role in Successful Six Sigma Deployments. Web.
Chadwick, Gail C. (2008). History of the Six Sigma Black Belt Naming Convention. Web.
Daley A.T. (2000). Pro: lean Six Sigma strategy revolutionizing health care of tomorrow. Clinical Leadership Manage; 20:E2.
Estioko-Taimuri T. (2005) The makeover of the Lakeshore General Hospital laboratories. Clinical Leadership Manage Rev. 20:E5.
Fleming JH, Coffman C, Harter JK (2005). Manage your human sigma. Harvard Business Review. 83:106–14, 192.
Hahn, G. I., Hill, W. J., Hoerl, R. W. and Zinkgraf, S. A. (1999). The Impact of Six Sigma Improvement-A Glimpse into the Future of Statistics. The American Statistician, 53 (3): 208.
Institute of Industrial Engineers Ireland (2008). Six Sigma. Web.
Larson, Alan (2003). Demystifying Six Sigma: A Company-Wide Approach to Continuous Improvement. New York: AMACOM. Pp.18-26
Ramberg, John S. Ph.D. (2000). Six Sigma: Fad or Fundamental.
Riebling N, Tria L. (2005) Six Sigma strategy project reduces analytical errors in an automated lab. Med Lab Obs ;37:20, 22–3.
Pande, P. and Holpp, L. (2001). What is Six Sigma?.McGraw-Hill, pp. 18-25
Smith, D. and Blakeslee, J. (2002) The New Strategic Six Sigma: The Old Standby Quality Approach, Six Sigma, Can Change Your Organization’s Culture to Drive Strategy Deployment and Business Transformation. T&D, 56 (9): 45.