Introduction
Control is the process whereby managers regulate how efficiently and effectively an organization is performing the activities necessary to achieve the organizational goals (Waddel, Devine, Jones & George, 2008). According to Hubbard, Rick, and Beamish (2007), “the basic concept of control process involves carefully collecting information about a system, process, person or a group of people in order to make necessary decisions about each”.
- Quality control
- Quality assurance
- Quality improvement.
Control process
Quality management system basically employs a kind of management in which managers not only control but also set up a means of feedback with which the managers devise strategies to help them accomplish the organization’s objectives. Based upon this theory, the managers engage junior staff by involving and motivating them. This not only increases their quest for excellence but also boots their morale. The theory of knowledge comes into play here because the managers interact with their staff and clients in which process they obtain knowledge on what and how to improve (Mauch, 2009). This is the theory linked to the control process as further discussed below. Managers set up control systems that consist of four steps:
Establishing standards to measure performance
Within an organization’s overall strategic plan, managers define goals for specific organizational departments. Some operational terms are known as the standards of performance to compare with the actual operational or organizational activity. Managers must carefully do these analyses.
Measuring actual performance
Most organizations prepare a formal report on performance which is reviewed by the managers regularly. These measurements should be related to the standard set of the control process.
Comparing performance with the standard
In this step, the actual performance is compared with the standard performance. When managers read their computer reports or walk through their plants, they identify whether actual performance meets, exceeds, or falls short of the set standards.
In taking corrective actions, Managers must determine what changes are necessary and apply them appropriately and in a timely manner (Mauch, 2009).
Control system and IT
According to Waddell, Devine, Jones, and George (2007) “effective control systems alert managers when something is going wrong and give them time to respond to opportunities and threats. Control and information systems are developed to measure performance at each stage in the process of transforming inputs into finished goods or services. At the input stage, the managers use feedforward control to anticipate problems before they arise hence the problems do not occur later during the conversion process (Cabrales, Luño & Cabrera, 2009). At the conversion stage, co-current control gives managers immediate feedback on how efficiently the inputs are being transformed into outputs so that they can correct problems when they arise. At the output stage, managers use feedback control to provide information about customers’ reactions to goods and services so that corrective action can be taken if necessary (Waddel, Devine, Jones & George, 2008, p 441). The types of control are shown below.
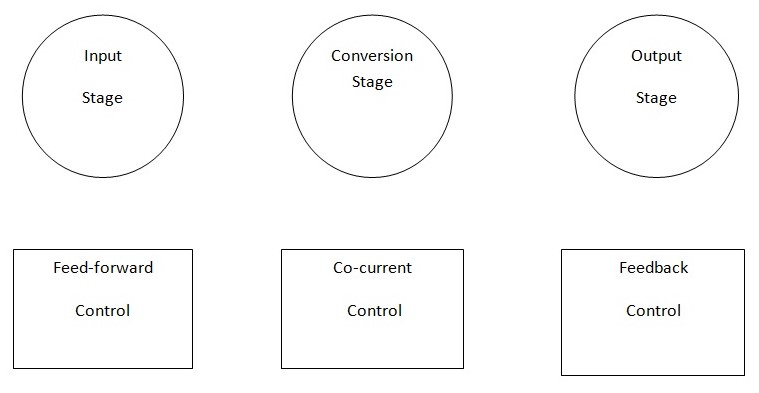
The major theorists
A conceptual framework for the design of organizational Control Mechanisms. Organizational control has many meanings and has been interpreted widely. Tannenbaum, whose view has dominated organizational theory, interprets control as the sum of interpersonal influence relations in an organization. Similarly, Etzioni treats control in organizations as equivalent to power. “Other than the power influence approach to control, organization theorists have also treated control as a problem in information flows” (Ouchi, 1979).
Rather than the organizational sociologists mentioned above, Dr. W. Edwards Deming was a major theorist in this field. Deming’s business philosophy is summarized in his “14 points”:
- In an organizational process, do not live with accepted levels of delays, mistakes, defective materials, and workmanship.
- Improve consultancy and every process for planning, production, and service. Search continuously for problems to improve quality and productivity and to constantly decrease costs (Who is Dr. W. Edwards Deming, 2010)
Importance of organizational control
The fallacy lies in the goals set by management. Instead of setting numerical quotas, management should work on improving the process. A flow diagram displays a process; the problem is how to improve it. The PDSA cycle will help (Deming, 1994, p. 32). In describing processes such as Deming’s system of profound knowledge, it is necessary to summarize it in a structured way; this develops a very real concern of presenting a complex multidimensional strategy as a simple framework (Gapp, 1999a).
Improving responsiveness to customers
To achieve high performance, an organization’s production system must respond to customer demands. Managers design production systems that produce outputs with attributes desired by customers. One of the central tasks of operations control management is to develop new production systems that enhance the ability of the organization to economically deliver more product qualities for the same price. The ability of an organization to please the demands of clients for lower prices, acceptable quality, and better features depend significantly on the nature of the organization’s production system. Managers need to recognize that there are limits to how responsive an organization can be and still cover its cost (Waddell, Devine, Jones, & George, 2007, p 471).
Operations management and competitive advantage
To attain high performance, managers try to improve their organization’s responsiveness to customers, the quality of its products, and its efficiency. To achieve this, managers can use several operations management techniques to improve the way an organization’s production system operates (Waddell, Devine, Jones, & George, 2007, p 471).
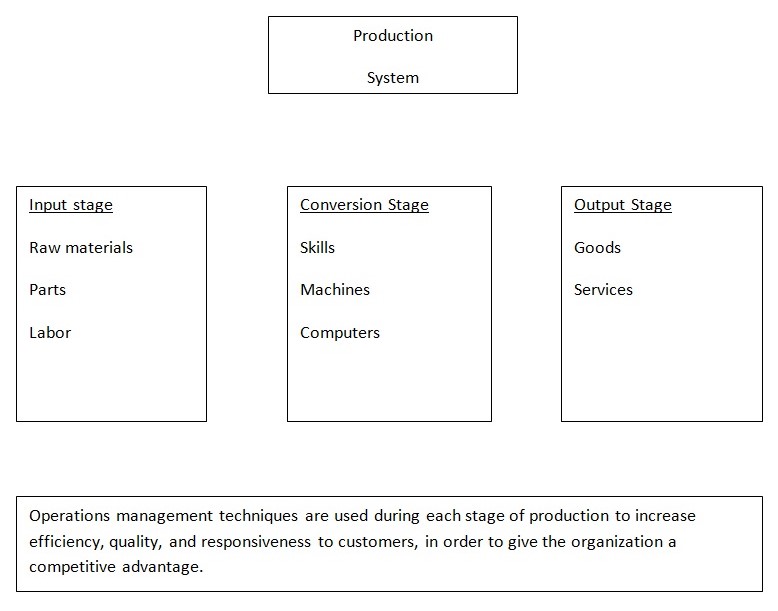
Improving quality
Managers seek to improve the quality of their organization’s output because it enables them to better serve customers, raise prices, and lower production costs (Waddell, Devine, Jones, & George, 2007, p 471). This is vital for the quality of products given to the end-user.
Improving efficiency
Improving efficiency requires one or more of the following: the introduction of a total quality management program, the adoption of flexible manufacturing technologies, the introduction of just-in-time inventory systems, and the establishment of self-managed work teams and/or processes reengineering. Top management is responsible for setting the context within which efficiency improvements can take place; for example by emphasizing the need for continuous improvement (Waddell, Devine, Jones, & George, 2007, p 471).
“The principles of planning, organizing, controlling, and specialization have led to a model of supposed efficiency that all too often stumbles over its multiple mechanisms and blocks effectiveness” (Mink et al., 1986, p. XII). It is within this environment that McGregor’s (1960, p. 44) well-known concept comes into prominence: “If employees are lazy, indifferent, unwilling to take responsibility, intransigent, Uncreative, uncooperative, this is due to the traditional assumptions and methods of organization and control”.
Quality management was adopted by Japanese firms such as Toyota in the 1970s and 1980s to mount a spectacularly successful attack on western markets. By the 1990s the message had gone around the world and total quality management came to be considered a necessary condition of being in business (Waddell, Devine, Jones, & George, 2007, p 471).
If we take a look at the product line of Rockstar energy drink, it is easy to evaluate what they have in store for their clients, how different they are from their competitors, and how their product revenue is increasing. They maintained the strategic highlighting on reducing product costs for profitable growth. To increase profits, Rockstar has dedicated a lot of research to ensure that its products live up to the strength of its brand. Rockstars as a company maintain standard quality for their drinks throughout all their stores to meet consumer expectations.
Owing to this, It has been possible for them to cope with customer demands for product variety along with offering affordable prices because product variety includes the cost of customizing or configuring products, the cost of excessive variety, the cost of excessive procedures, and the cost of excessive processes and operations (Julian, Dankwa & Justis, 2009).
As the competitive environment changes, any business has to concentrate on flexibility to achieve a competitive advantage. Rockstar’s strategy is quick launching of new products, adjustment of the processing system capacity and process technologies to meet market demands, and proper personnel training (Cabrales, Luño & Cabrera, 2009).
Conclusion
It is significant for any business to improve the performance of operational processes to be successful. To achieve such outcomes operational management has either direct or indirect impacts on the bottom line performance. Operational management can be seen as a source of competitive advantage because it emphasizes the quality of management and the ability to correctly assess, manage and align operational activities. Operational management helps in dealing with small and predictable events such as processing errors, human resources, system failure, and loss.
To determine the operational activities any business has to find a consistent approach to measure and monitor operational performance throughout the organization and determine which measurement tools can best fit the requirements. Operational activities help measure outcomes that will increase profitability and its reputation within its target market. Businesses are focusing increasingly on measuring their project outcomes, and this provides a firm to monitor their operational activities efficiently and effectively, necessary for quality customer service, leading to a growing satisfied customer base, producing smoother and more stable cash flows (Julian, Dankwa & Justis, 2009).
Reference List
Cabrales, A., Luño, P., & Cabrera, R. (2009). Knowledge as a mediator between HRM practices and innovative activity. Human Resource Management ,48( 4), 485- 503.
Davidson, P., Simon, A., Woods, P. & Griffin, R. W. (2009). Management. (4th Edition). Australia: John Wiley & sons Australia, Ltd.
Hubbard, R. (2007). Strategic Management, (3rd Edition). Australia: Pearson Education.
Deming, W.E. (2 Ed.) (1994). The new Economics, for industry, Government, Education. Cambridge, MA: MIT press.
Gapp, R. (1999a). Quality Principles, a successful foundation upon which to build a learning organization. Proceedings of the Fourth International Conference on ISO 9000 and TQM, Hong Kong, Hong Kong Baptist University, 524-30.
Gapp, R.P. (1999b). Leadership, learning styles, and dealing with individual difference, keys to quality management in a learning environment. Proceeding Third International and Sixth National Research Conference on Quality Research, Melbourne.
Gapp, R.P. (2000). What you see is what you get, a model for understanding the difficulties in applying profound knowledge by organizational type. Proceedings Fourth International and Seventh National Research Conference on Quality Research, Sydney.
Julian, D., Dankwa, C. ,& Justis, T. (2009). Understanding strategic responses to interest group pressures. Strategic Management Journal, 29( 9), 963-984.
Mauch, D. (2009). Quality Management:Theory and Application. Web.
McGregor, B. (1960). The Human Side of Enterprise. New York: McGraw-Hill
Mink, G., Shultz, M. and Mink, P. (1986). Developing and Managing Open Organizations, OHRD Associates, and Austin, TX.
Ouchi, G. (1979). A conceptual frame work for the design of organizational control mechanisms, 25, 833-848.
Waddell, D., Devine, J., Jones, R. & George, J. (2007). Contemporary Management. (6th Edition). Australia Pty Ltd., N.S.W.: Ailsa Barckley: McGraw-Hills
Who is Dr. W. Edwards Deming?.(2008). Web.