A systems map of the operation
The following outline is the transformation process within Tesco PLC; a UK based global chain of supermarkets. The operation system traces the various systems and subsystems within the firm as products are prepared for sale to clients (see Figure: 1). Operation management entail the planning, organizing, and controlling the performance that influence a person’s conduct through coordination (Stevenson, 2007, p. 9).
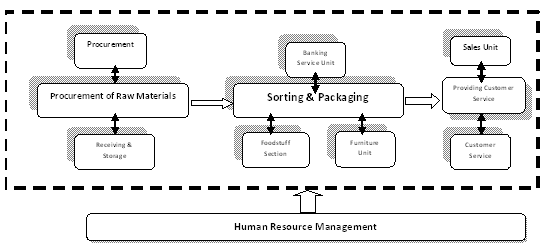
The first phase in the transformation process operations at Tesco encompasses the sourcing of the goods and services retailed at the supermarkets. The subsystem is divided into other subsystems or processing units including the procurement section which sources for the goods and the warehouse unit which verifies the goods delivered and subsequently stores them awaiting packaging. These goods are then delivered to the relevant shops for packaging. The next subsystem is within the packaging section whereby the operations manager oversees the sorting or identifying specific products to be forwarded to the right shelves within the stores.
The most important aspiration in operation management is to meet the needs and demands of their clients’ thus viable operations systems must be geared towards achieving that objective with correct price and timing. Stevenson (2007) asserts that an operation system basic purpose is giving consumers ‘right thing at a right price at the right time’ (11). Thus the final subsystem at the transformation stage at Tesco superstores involves the sales team that ensures customers are guided in the selection process while answering any questions concerning the products or services on offer.
The elementary responsibilities involved in offering services and manufacturing goods entails managing the course of labour from inputs to outputs. Thus in our diagram the human resources are the overriding factor that ensured the smooth operations within the transformation system and subsystems. Similarly, the operations management must control expenses in disbursements to suppliers and productions expenses within the firm. In all this, the firm has to ensure their clients need and desires are met on a timely basis (Slack et al. 2010).
Tesco PLC supermarket is a retail chain of department stores domesticated in the UK but also globally represented. Since it is not a customary manufacturing plant, the analysis traces the input process from the sourcing for goods from suppliers to the transformation (or the display) and sales, to customers as the final output. The process also entails getting client feedbacks to discern how to boost the system.
The inputs envisioned in the management system are the various grocery products and services offered by the department store that form part of the subsystems and sub-subsystems including foodstuff, crockery utensils, furniture, clothing garments, beauty products etc. Services offered encompass telecommunication and banking. In 2007, Tesco’s commissioned ‘Continuous Replenishment’ software that screens and manages its warehouse catalogue (Computing.co.uk, 2007)
The inputs also include other subsystems like the buildings used to retail the products and services, energy, human resources hired to operate the stores, capital to purchase items, and product and market information critical in operating the business (see Figure: 2). Tesco still operates under the motto “pile it high, sell it cheap” coined by its creator Sir Jack Cohen to capitalise on diverse well stocked products retailed at subsided prices. However the firm has recently also earmarked the middle class segment by having more upscale products and services.
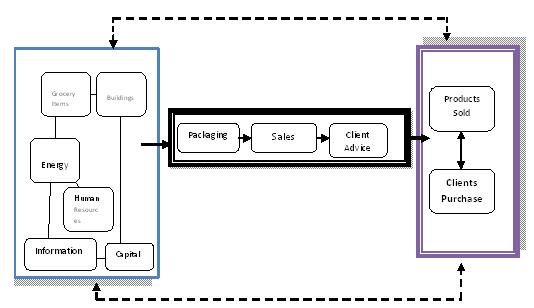
The transformation process within the chain of stores encompasses two main subsystems the packaging process, sales of the products and services, and offering product advice to the clients. At Tesco, the firm has set many units or subsystems that strategically deal various issues within the stores.
The output from the input and transformation within the chain is the purchase of the goods by the customers hence ensuring the input material from the production process is delivered to the end-user, the consumer. The feedback from the customers is then recycled back to the production team to improve on the system or maintain the standards as demanded by the customers. The management or control of the system is closely regulated by the various operations managers within the system network (Barnat, 2005).
Definition: Operation Management
An organisation’s operation can be described as a system or process that integrates the diverse units or components inherent in the organisation to produce the final product. The system thus mobilises all the resources including capital, human resources and raw materials to goods and services for consumption by the customer. The operation system and subsystems thus converts inputs to the production process including raw materials and human resources into viable outputs. The operations systems within an organisation are interlinked with each unit or division charged with a different complimentary function within network thus offering valuable support to others.
Organisations that perfect their operating systems to higher efficiency in terms of lower production expenses, timely delivery and quality outputs eventually manage to have a market advantage over their competitors in the market. Astute operational management espousing the conventional organizational functions of planning, organizing, directing, and controlling is therefore critical to the smooth running of the organisation.
According de Lima et al. (2007: 2) the remodelling of an organisation’s operation system to strategically meet the current challenges posed by globalisation of markets is essential. The authors assert this can only be possible if distinct ‘performance measurement subsystem’ is applied to appraise the efficacy of the existing programs within the organisation. A process approach that identifies the procedural gaps is envisioned.
A system is commonly defined as a group of interacting units or elements that have a common purpose. Within an operation system, there are further subsystems that are form the components of the larger unit. These strategic management units (SBUs) encompass schemes, merchandise, tasks, and accountability centres like manufacturing unit, accounts, customer service all within the transformation system.
Operation managers thus recognise the need to enhance their operation systems by strengthening and enhancing the systems to optimally operate within all the subsystems. Nevertheless Suárez-Barraza et al (2010: 64) assert that a more holistic view of the organisation is more viable as opposed to the systems approach since the latter tends to ignore the human aspect as it emphasises on the systems and subsystems that generally guided by the classical and quality management theories.
The systems approach management is derived from system theory which states that to comprehend fully the workings of an operation, the organization should be analysed as a system. Consequently, a subsystem is a component of the whole system that entails various ‘cogs’ that interdependently produce the output desired. Systems are either considered open or closed systems whereby the former refers to those that work together with other organizations while the closed are those that do not integrate with others. In an open system the elements work together with the business environment that includes the clients, contractors, government and even rivals (Heil & Droege, 2007).
Annotated Input-Transformation-Output Diagram
This diagram depicts the input, transformation and output plus the feedback that is typical of open systems.
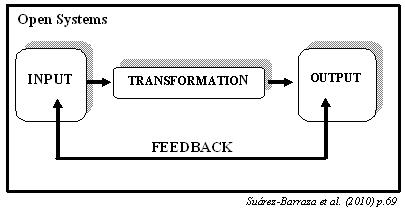
Roper & Millar (2008) have outlined operation systems as product of business systems analysis (BSA) which is a logical grounding that entails evaluating organisations as systems or the process of methodically and independently collecting information about business systems. Drucker formulated the proposition of organizations having explicit objectives or management by objectives (MBO) comprehensible to all employees within the firm. He was influential in advocating the primacy of the “knowledge worker” or non-hierarchical management style whereby teamwork is of very essential with the finest employees allotted duties accordingly rather than through position or executive authority (Drucker, 1954).
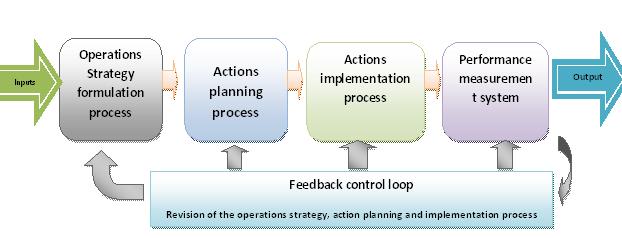
The Process Map Description
The model designed follows a process approach which de Lima et al. (2007: 2) offers the chance to present a step by step analysis of the system process undertaken. Thus in the first phase, inputs are injected into the production process and the management initiates an operations strategy formulation in which the organisation will follow in the subsequent events. The formulated strategy is dependent not only on the input of the organisations strategic team, but also takes views from the feedback from the output or customers. This phase being the most crucial is an ongoing process but is envisioned to take a maximum of two days since the organisation follows the set guidelines.
The second phase in the process is the action planning process. Like in the first phase, this entails following strategies whereby specific action plans are designed by each subsystem or strategic business unit (SBU). The SBUs are independent units that are authorised to organise their own budgets according to a preconceived and agreed format from the first phase. The planning process is done on regular basis unlike the entire organization’s strategy formulation process. This takes a maximum of one day to be completed by the sectional operations teams and managers.
The third phase in the model describes the plans/actions implementation process. In this phase, the designed plans are put into practice as the organisation operations managers oversee the efficient implementation of the specific plans. The process is therefore highly dependent on the line staff that must be properly briefed on the workings of the plans to ensure unhindered implementation Failure to clearly outline the plans can lead to bottlenecks that can hold back on production and eventually meaning the output will be affected both in terms of quality and timely production.
The final phase prior to releasing the output is the performance measurement system that is designed to ensure quality control within the operation system network. Various performance measurement plans are designed by both the strategic teams and in the planning process that give an accurate indication of how the system is performing against set benchmarks. Workers are given goals and targets that must be met within the production process. Similarly the stage also measures the performance of the products produced in the output as gauged by the customers. The feedback from these appraisal systems is then fed back to each specific system or phase to improve or analyse how they can further enhance the system.
The Main Control System
The control systems employed at Tesco supermarkets in both its local (UK) and international operation systems is through the application of modern logistics software that is able to keep track of the inventory for the supply and delivery of the raw materials. Similarly, quality checks are highly developed as most of its products are supplied from overseas locations thus communication and technology is highly developed while keeping a tight lease on the contractors who must follow rigid guidelines set by the firm.
Tesco’s operation and supply network is also dependent on well trained staff whereby the company manages to maintain the same standards administered locally in its international operations. Company staff handles the most important (primary) activities but Tesco also outsources from the major suppliers/contractors through the value chain. A representation of the system applied can be envisioned as outlined in Porter (1985) value chain whereby the operation system is viewed in terms of systems and subsystems navigating from the inputs, transformation and outputs progression (see figure: 4).
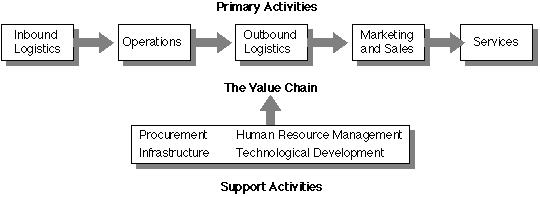
The core activities within the logistical control system evolve around the inbound supplies, the transformation operation, outbound goods and services, marketing and sale of the products and the customer service offered by the firm. Nevertheless, the company must have support services to ensure the system operations are completed. These include procurement, human resource management, technological, and infrastructure development. The system operation can therefore be viewed in terms of a cyclical replicating network that has veritable performance measurement tools administered by the diverse operations managers who evaluate the performance of the support services (see Figure: 5).
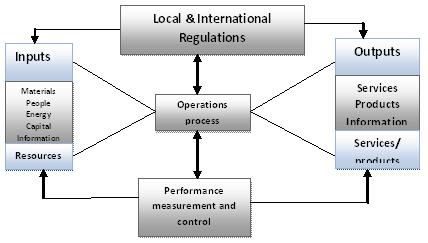
The control mechanism integrates the inputs/resources that include the raw material, human resources, energy, capital and information which are measured against local and international regulations. Likewise, performance measurement and control for the inputs is gauged against the feedback from the outputs or services and products thus discerning the performance gaps not met against the benchmarks (Suárez-Barraza et al. 2010).
Tesco’s operation and supply network offers the firm one of its main competitive advantage over their rivals. Tesco is able to control its entire supply network with contracted firms that supply products to Tesco conforming to their guidelines hence able to vary the price paid to their advantage. The logistic software used by the firm Micro Focus will enhance its capacity to keep track of its global operations (Computing.co.uk, 2007). Tesco is thus able to blend, changes in international populations, conventions, technologies, and finances to its operations business management advantage applying divergent market forces into operational advantage while ruthlessly implementing its standards with all the support service (Godward and Deck, 2010)
Operations systems that are aptly controlled enable the firm measure performance from its component systems and subsystems with a feedback system that ensures customer satisfaction even in global operations where local personnel are the majority staff. From control of the inputs (raw materials, human resources, energy and information) to the transformation within the department stores that is vastly controlled and to the output, Tesco has managed to utilise an operation system management process exceptionally. The modern value chain management has enabled the firm retain lowered prices as envisioned by its founder. As globalisation and worldwide economic recession control to impact negatively on consumer spending habits, Tesco’s emphasis on low price models will reap even more dividends as shoppers from the higher end segments are forced down to cheaper prices.
Tesco is United Kingdom’s largest and most lucrative supermarket chain constantly keeping alive their adage “under one roof” feasible in its mega markets. Tesco has almost 400,000 employees employed in the over 5,000 stores within the UK and globally (Tescoplc.com, 2011). Its operations encompass the grocery stores and supermarkets, fuel retailing (Tesco Express), diminutive municipal stores (Tesco Metro), hypermarkets (Tesco Extra), and financial services (Tesco Personal Finance) with the total revenue streams generating 4.3 billion growing at over 20 percent annually. In addition, Tesco.com is UK’s foremost online delivery service able to deliver products across the country while controlling 31 percent of the country’s grocery retail market (Corporatewatch.org, 2004).
Nevertheless, behind all the glitter of its shelves and profits, Tesco like other global supermarket chains is infamous for exploiting poor farmers worldwide with its low price regime. Similarly, the firm has poor labour relations and is also accused of driving small corner shops out of business.
Summary
Operations entail the daily functions within an organisation while systems are a group of interrelated components that have an associated objective which are the drivers of the whole. Operation system management within an organisation therefore describes open systems that interact with other systems within the wider network thus taking consideration of the environment within its sphere of operations to formulate strategies that give it a competitive advantage.
Within contemporary organisations, innovative strategic management requires astute operations systems that have constant measurable performance appraisals. A system process approach therefore aptly traces the performance of the various systems and subsystem along the value chain from inputs to the transformation process and to the final output while keeping a close watch on the overall external resources like human resources and suppliers performance as gauged from the client’s perspective.
Reference List
Barnat, R. (2005). Management Control. [Online]. Web.
Computing.co.uk. (2007). Tesco upgrades supply chain systems. Web.
Corporatewatch.org. (2004). TESCO: A Corporate Profile. Web.
De Lima E. Pinheiro, Gouvea da Costa S. E. and Reis de Faria A. (2007). “Structuring Plans for Operations Strategy Action”. 19th International Conference on Production Research (pp. 1-6). Parana, Brazil: Pontifical Catholic University of Parana.
Drucker, P. (1954). The Practice of Management. New York: Harper and Row.
Godward, T. and Deck M. (2010). Operational Strategy: Bold Moves, Breakout Performance. Web.
Heil, K. and Droege S. B. (2007). OPEN AND CLOSED SYSTEMS. Web.
McFarlane, D. and Sheffi Y. (2003). The Impact of Automatic Identification on Supply Chain Operations. Cambridge: Cambridge University.
Roper, M. & Millar L. (2008). Analysing Business Systems. London: International Records Management Trust.
Slack, N., Chambers S. and Johnson R. (2010). Operations strategy. Web.
Stevenson, J. W. (2007). Production/Operations Management. Irwin: McGraw-Hill.
Suárez-Barraza, M. F., Ramis-Pujol J. & Heras M. Á. (2010). “Reflecting Upon Management Systems: Content Analysis and Synthesis”. International Journal of Business Research and Management (IJBRM), 1: 2, 64-82.
Tescoplc.com. (2011). Hoover’s Company Profiles:Web.